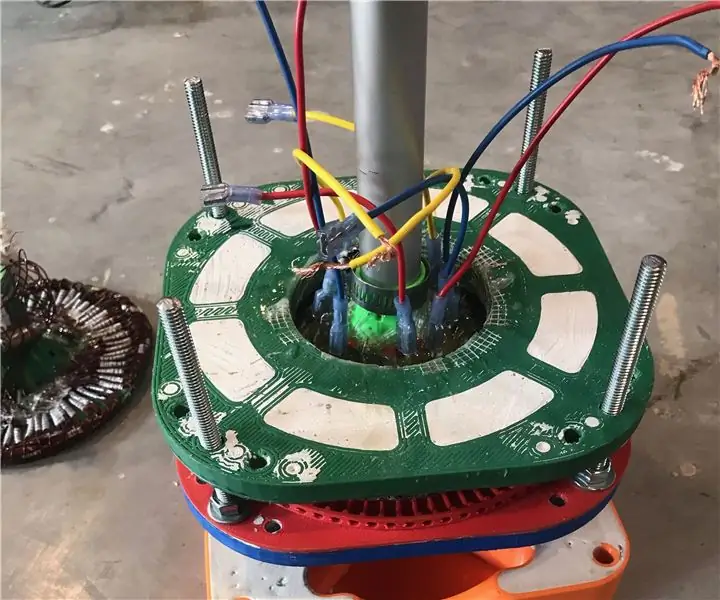
Innholdsfortegnelse:
2025 Forfatter: John Day | [email protected]. Sist endret: 2025-01-23 15:02
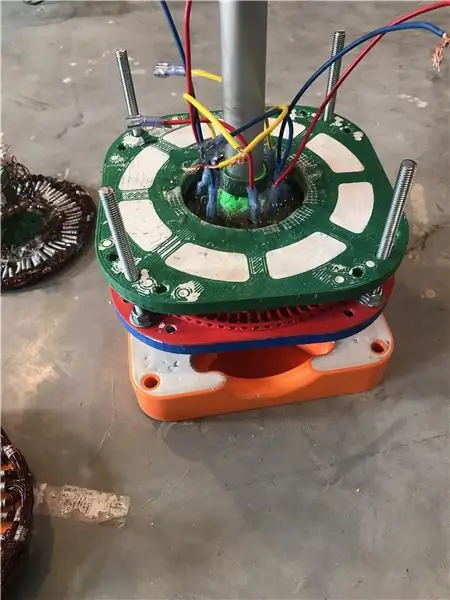
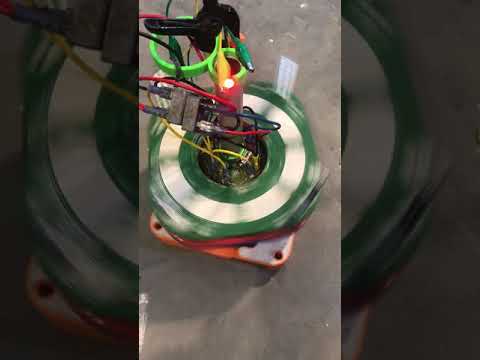
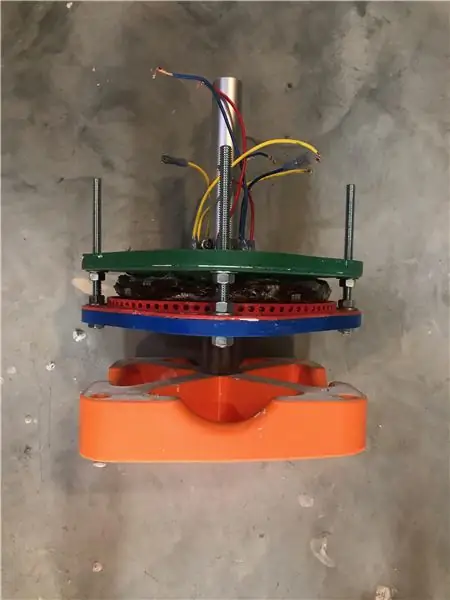
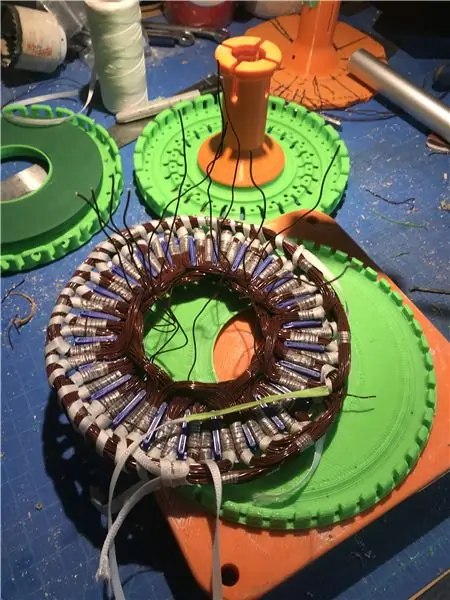
STOPPE!! LES DETTE FØRST !!! Dette er en oversikt over et prosjekt som fortsatt er under utvikling. Du er velkommen til å tilby støtte.
Mitt endelige mål er at denne typen motor/dynamo kan bli en parametrert åpen kildekode -design. En bruker bør kunne angi noen parametere, for eksempel dreiemoment, hastighet, strøm, volt/o/min, vanlige magnetstørrelser og kanskje ledig plass, og en serie med 3D -utskrivbare.stl- og.dxf -kuttfiler bør genereres.
Det jeg har gjort er å lage en plattform som kan validere et simulert design, som deretter kan utvikles til en mer optimal enhet etter fellesskap.
Delvis er dette en grunn til at jeg har satt opp dette med et dynamometer. Et dynamometer måler dreiemoment og hastighet for å tillate hk, eller akselen Watt å måle. I dette tilfellet har jeg bygget dynamoen med en gjennomgående, stasjonær aksel, noe som gjør det enklere å sette opp et dynamometersystem, og så kan den konfigureres til å bli drevet som en motor av en RC ESC (håper jeg), og dreiemoment måles på utgang, samt hastighet, V og forsterkere, slik at motoreffektivitet kan bestemmes.
For mitt formål kan den drives av en motor med variabel hastighet (overskudd fra batteridrevet bor, med trinnvis gir), og inngang på akselmoment måles, samt V og ampere ut, slik at ekte effektivitet kan genereres og forventede turbinbelastninger som skal simuleres.
I denne modusen håper jeg å bruke en RC ESC som er i stand til regenerativ bremsing, og kanskje en Arduino for å kontrollere belastningen min VAWT bærer for å oppnå MPPT (Multi Power Point Tracking).
MPPT brukes både i sol- og vindturbinkontroll, men det er litt annerledes for vind. Med vindkraft er et stort problem at etter hvert som vindhastigheten dobles 10 km/t til 20 km/t, øker energien som er tilgjengelig fra vinden med kuben, så med 8 ganger. Hvis 10W var tilgjengelig i 10 km/t, så er 80W tilgjengelig ved 20 km/t. Det er flott å ha mer energi, men generatorens utgang dobler bare som hastigheten dobler. Så hvis du har den perfekte dynamoen for en vind på 20 km/t, kan belastningen være så sterk at den ikke starter med 10 km/t.
Det MPPT gjør er å bruke en kraftig solid state -bryter for å koble fra og deretter koble en dynamo til igjen veldig raskt. Den lar deg justere hvor mye belastning en dynamo bærer, og Multi, av MPPT, betyr at du kan angi forskjellige belastninger for forskjellige hastigheter.
Dette er veldig nyttig, ettersom alle typer turbiner samler sin maksimale energi når lasten er tilpasset den tilgjengelige energien, eller vindhastigheten.
SÅ
Dette er ikke en oppskrift, selv om jeg tror den kan kopieres fra det jeg har lagt ut, og vil gjerne gi ytterligere informasjon, men jeg foreslår at det beste alternativet ville være å foreslå forbedringer for meg før krets- og sensorkonkurransen avsluttes, slik at jeg kan vurdere, svare og kanskje forbedre dette instruerbart.
Jeg vil fortsette å oppdatere, revidere og legge til informasjon, så hvis det er interessant nå, vil du kanskje sjekke inn igjen om litt, men jeg håper å få gjort en god del før Sensors -konkurransen avsluttes 29/19 juli.
Jeg er heller ikke et spesielt sosialt dyr, men jeg liker et klapp på skulderen nå og da, og det er en av grunnene til at jeg er her:-) Fortell meg om du liker å se arbeidet mitt, og vil se mer, er du snill:-)
Dette prosjektet kom fordi jeg ønsket en kontrollerbar belastning for å teste mine turbinedesigner, og jeg ville at den skulle være lett reproduserbar, slik at andre også kunne bruke den. For dette formål begrenset jeg meg til å designe noe som bare kunne bygges med bare en FDM -skriver, ingen andre maskinverktøy trengs. Det ser ikke ut til å være mange kommersielle produkter som dekker behovet for et høyt dreiemoment, lav hastighet, ikke -cogging -generator, selv om det er noen få fra Kina. Generelt er det ikke mye etterspørsel fordi girsystemer er så billige og elektrisitet er så billig.
Det jeg ønsket var noe som produserte rundt 12V ved 40-120 o / min, og rundt 600-750W ved 120-200rpm. Jeg ønsket også at den skulle være kompatibel med rimelige 3 -fase PMA -kontrollere fra RC -verdenen (ESCs elektroniske hastighetskontrollere). Et siste krav var at det skulle være en utløper (etui eller skall med magneter roterer, mens aksel med stator er stasjonær), med en aksel som passerer helt gjennom saken, og en stator som klemmer seg til akselen.
Dette instruerbare er et pågående arbeid, og jeg legger det ut slik at folk kan få et syn på prosessen, ikke så mye fordi jeg synes de burde kopiere den. En viktig ting jeg vil endre er at trådplaten jeg bygde ikke er nær sterk nok til å kanalisere magnetfeltene rundt ringen, så mye av magnetfluksen som betales for disse magnetene er bortkastet på baksiden. Når jeg gjør om designet, som jeg skal gjøre om kort tid, vil jeg sannsynligvis gjøre det med de magnetiske bakplatene som cnc -kuttede stålplater. Stål ville være ganske billig, mye sterkere, og ville forenkle det meste av dette bygget. Det var interessant å gjøre FDM/wire/gips -komposittene som jeg har illustrert her, og med jernbelastet PLA hadde ting også vært annerledes. Jeg bestemte meg for at jeg ville ha noe som virkelig ville vare, så stålplater.
Jeg har gjort gode fremskritt med denne versjonen, som jeg skal bruke til å teste denne VAWT. Jeg er ikke helt der når det gjelder lavspenningsytelse ennå. Jeg tror min effekt/dreiemoment er i riktig ballpark, jeg oppdaterer etter hvert som ting utvikler seg, men på dette tidspunktet har det jeg har en god sjanse til å være den kontrollerbare belastningen jeg trenger. Når den er kortsluttet ser det ut til å kunne gi ganske mye momentmotstand, mer enn nok til å teste turbinen. Jeg trenger bare å sette opp en kontrollert motstandsbank, og jeg har en venn som hjelper meg med det.
En ting jeg kort vil ta opp er at som mange andre nå, har jeg hatt en 3D (FDM-brukende PLA) skriver i noen år, som jeg har hatt 20-30 kg glede av. Jeg synes det er frustrerende, men deler av hvilken som helst størrelse/styrke er enten dyre og veldig trege å skrive ut, eller billige, raske og spinkle.
Jeg vet hvor mange tusen av disse 3D -skriverne som finnes, ofte gjør ingenting fordi det tar for lang tid, eller det koster for mye å lage nyttige deler. Jeg har kommet med en interessant løsning på sterkere raskere deler fra samme skriver og PLA.
Jeg kaller det en "hellet struktur", der det trykte objektet (som består av 1 eller flere trykte deler, og noen ganger lagre og aksler), er laget med hulrom designet for å bli helt med et herdende flytende fyllstoff. Selvfølgelig vil noen av de åpenbare valgene for en hellet fylling være noe som epoksy lastet med hakket glassfiber med korte tråder, som kan brukes til sammenstillinger med høy styrke og lett vekt. Jeg prøver ut noen lavere kostnader, mer miljøvennlige ideer også. Den andre siden av denne "heltekonstruksjonen" -enheten er at hulrommet eller hulrommet du skal fylle, kan ha elementer med høy strekkfasthet med liten diameter, forspent på den trykte "formen/pluggen", noe som gjør den resulterende strukturen en kompositt i materialer, og i struktur, del Stressed Skin (PLA -kappen), men med en høy komprimert stregth -kjerne som også inneholder elementer med høy strekkfasthet. Jeg skal gjøre en andre instruks som inneholder dette, så jeg vil snakke om det her, bare for å dekke hvordan det gjelder denne bygningen.
Trinn 1: Materialeliste og prosess
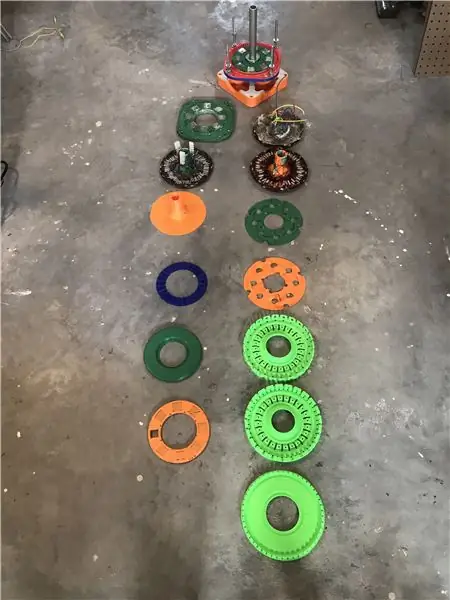
PMA består av 3 samlinger, hver samling inneholder eller bruker en rekke deler og materialer.
Fra toppen (lagersiden) til bunnen (statorsiden), 1. Lagerbærer og topplager
2. Stator
3. Nedre magnetoppstilling
1. bæringsbæreren og toppmagneten
Til dette brukte jeg 3D -trykte deler oppført ovenfor
- 150 mm 8 -polet øvre mag og lagerstøtte CV5.stl,
- innvendig plate på lagersiden
- ytre plate på lagersiden
- 1 "ID selvjusterende lager (som brukt i standard puteblokker ++ legg til internettkobling),
- 25 'av 24g galvanisert ståltråd
- 15 '10g galvanisert ståltråd
- 2 ruller grov stålull
Alternativt kan den tunge ståltråden og stålullen erstattes med stålplater, laser / vannstrålesnitt eller en 3D -trykt magnetisk bakplate kan være mulig (men tung ståltråd er fortsatt en god idé, da den vil motstå plastisk deformasjon over tid). Jeg har prøvd å støpe en underlagsplate med epoksy fylt med jernoksidpulver og lyktes. Forbedring av flusskoblingen mellom magneter i matrisen lateralt ved å bruke en mer effektiv bakplate bør øke voltene ved lavere omdreininger. Det er også godt å huske på at dette er den viktigste strukturelle komponenten, og bakplaten overfører kreftene fra magnetene til jekkstolpene. De magnetiske kreftene som trekker platene mot hverandre kan være hundrevis av kilo, og kreftene øker eksponentielt (Cubed, til den tredje kraften) når platene kommer tett sammen. Dette kan være svært farlig, og forsiktighet må utvises med verktøy og andre gjenstander som kan tiltrekkes av den monterte platen eller den er tilbake!
Jeg brukte omtrent 300 fot 24g belagt magnettråd i viklingene som jeg vil dekke i detalj senere.
Trinn 2: Fremstilling av magnetplatene
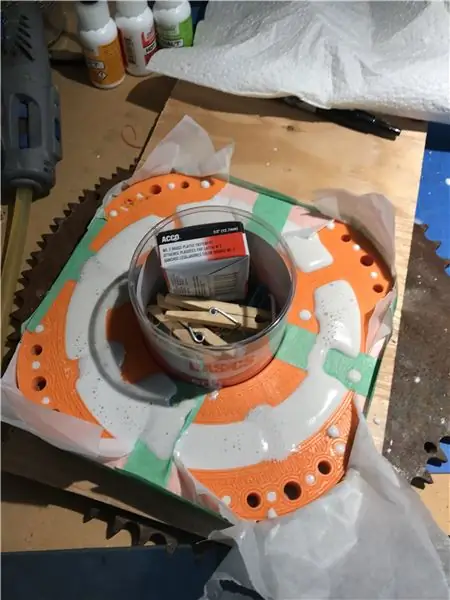
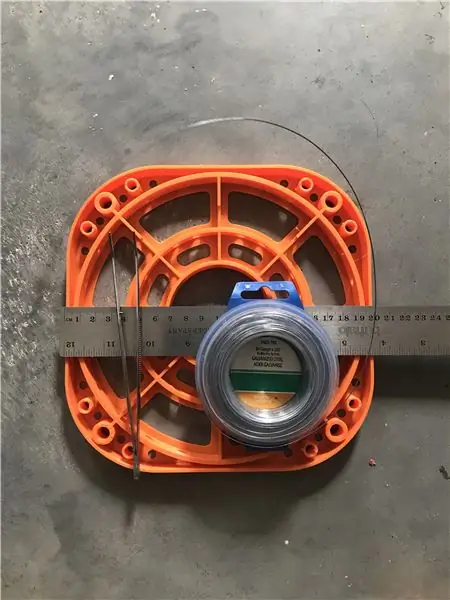
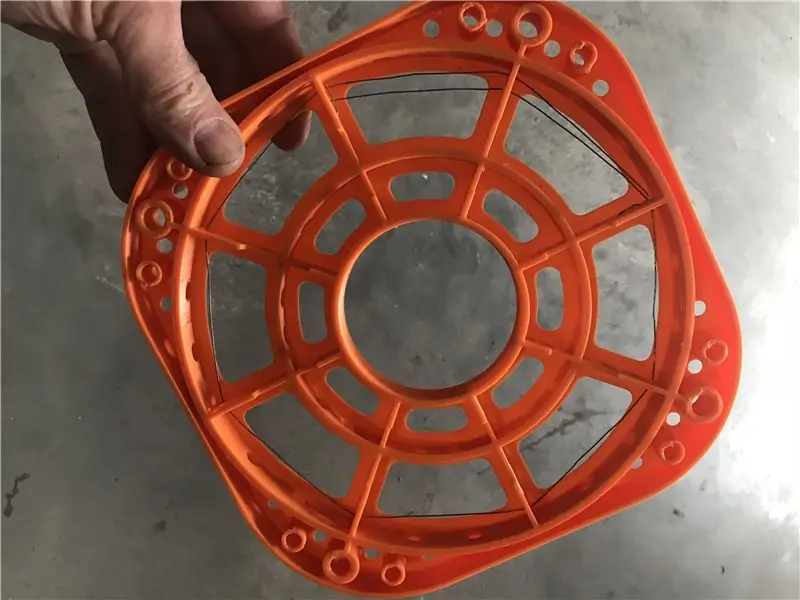
I denne aksialstrømgeneratoren bruker jeg to magnetfiler, en på hver side av statorspolene, for å minimere tannhogging og maksimere ytelsen. Dette betyr at ingen magnetisk kjerne er nødvendig for å trekke magnetfeltet gjennom kobberviklingene, slik de fleste motor/alt geometrier gjør. Det er noen aksiale fluksdesigner som bruker pariserekjerner, og jeg kan prøve noen eksperimenter på den måten i fremtiden. Jeg vil prøve 3D -trykkbart jernbelastet materiale.
I dette tilfellet har jeg valgt en 8 -polet magnetoppstilling i omtrent en 150 mm sirkel, ved bruk av 1 "x1" x0,25 "sjeldne jordartsmagneter. Denne størrelsen skulle sikre at alle delene ville passe på en 210 mm x 210 mm utskriftsseng. Generelt har jeg dimensjonert denne generatoren først ved å forstå at jo større diameter, jo bedre når det gjelder volt per omdreininger, så den gjorde den så stor som den som passer komfortabelt til min utskriftsseng. magneter, jo lenger magneter er fra sentrum, desto raskere reiser de, og det er også mer plass til kobber! Alle disse tingene kan legge seg fort! Men en konklusjon jeg har kommet til er at i dette størrelsesområdet er en konvensjonell Flux -systemet kan være et bedre hjem. Små rotorer har ikke mye plass, og ting kan bli ganske tette, spesielt hvis du gjør en gjennomgående aksel som jeg har gjort i denne designen. Også hvis magneten din (radiell lengde) er liten i forhold til rotordiameteren din, som i denne, (omtrent 6 "diameter til 1" magnet), og deretter ng blir litt rart med den indre endeviklingen som bare er omtrent 1/2 lengden på utsiden.
Tilbake til instruksjonen! Måten jeg har satt sammen magnetplatene på denne generatoren er å først lime magnetplaten (grønn) til den røde flensen/bakplaten. Jeg la deretter magnetplaten på noen få tynne lag med kryssfiner (ca. baksiden av magnetplatene. Dette gikk ikke helt som jeg hadde håpet. Det sterke magnetfeltet trakk ledningen mot midten av magnetene, og jeg lyktes ikke med å bøye hver rad, av tråd for å passe perfekt til neste sted, uten å forstyrre den første viklingen. Jeg hadde håpet at jeg bare kunne spole inn ledningen, og den magnetiske strømmen ville låse den. Deretter prøvde jeg å kutte ringringer, og dette var bedre, men fortsatt langt fra det jeg hadde håpet på å få en fin konsistent bakplate fra wire. Mer komplekse måter å få dette gjort på er mulig, og kan være verdt fremtidige eksperimenter. Jeg prøvde også å bruke stålull, komprimert i magnetfeltet, som en bakplate eller flux Dette syntes å fungere, men den faktiske jerntettheten så ikke ut til å være særlig høy, så jeg di Jeg testet ikke effektiviteten, delvis fordi jeg trodde at trådstrukturen var viktig for de mekaniske belastningene på magnetplatene. Stålullen kan også være verdt fremtidig undersøkelse, men vannstråleskårne stålplater er sannsynligvis det neste alternativet jeg vil prøve.
Deretter tok jeg den oransje 3D -trykte delen, og flettet ledning gjennom og rundt den, langs det som virket for meg som retningene for høyeste belastning, bolt til bolt og bolt for å sentrere et par ganger i hvert hjørne. Jeg viklet den også rundt bolthullene der all trådstang passerer som jekkestolper for å beholde og justere avstanden mellom platene.
Etter å ha blitt fornøyd med at magnetplaten og flensen var god nok, og den oransje bakplaten var tilfredsstillende gjenget med forsterkningstråd, skjøt jeg de to med lim. Det må utvises forsiktighet, da denne limfugen må være vanntett eller tett. Jeg hadde lekkasjer de to første gangene, og det er rot, sløser med mye gips og er mer stress enn du trenger. Jeg vil anbefale å beholde litt blå kliss eller annen tyggegummi som ikke permanent lim rundt for å lappe lekkasjer raskt. Når delene er festet, fyller du med forsterkningsmaterialet du ønsker. Jeg brukte en hard gips, modifisert med PVA -lim. Gipset skal nå 10 000 psi komprimerende, men ikke mye i spenning (dermed ledningen). Jeg vil prøve epoksy med hakket glass og cabosil, eller betong og tilsetningsstoffer.
En praktisk ting med gipset er at når det sparker har du ganske lang tid der det er vanskelig, men skjøre og lekkasjer eller klatter kan lett skrapes eller slås av.
I denne designen er det to magnetplater. Den ene har peiling, en standard 1 puteblokk selvjusterende enhet. Jeg presset min inn i magnetoppsettet tidlig. For applikasjonen jeg har designet den for, vil et andre lager være plassert i turbinen over dynamoen, så jeg brukte bare det ene selvjusterende lageret. Dette var litt vondt til slutt. Disse delene kunne også settes sammen med hver magnetplate som har et lager, hvis utgangstrådene fra statoren ble ført innvendig gjennom den monterte akselen. Dette ville la kontra roterende propeller monteres på en felles, ikke -roterende aksel/rør.
Trinn 3: Opprette Stator

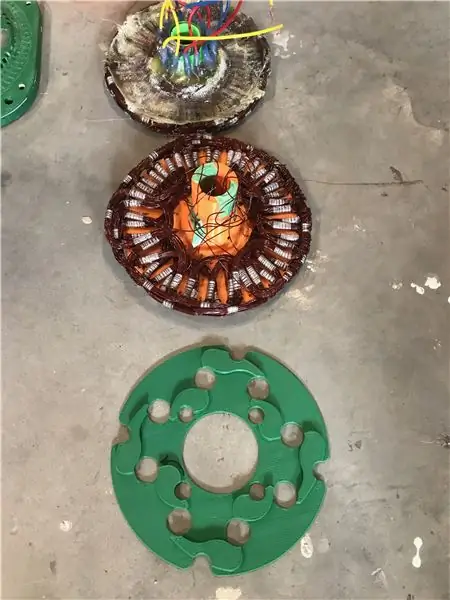
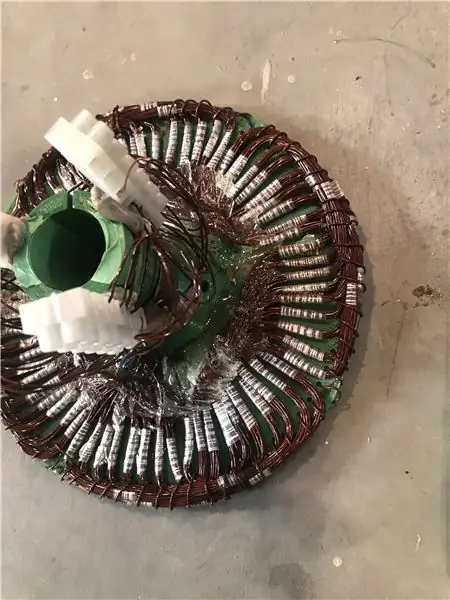
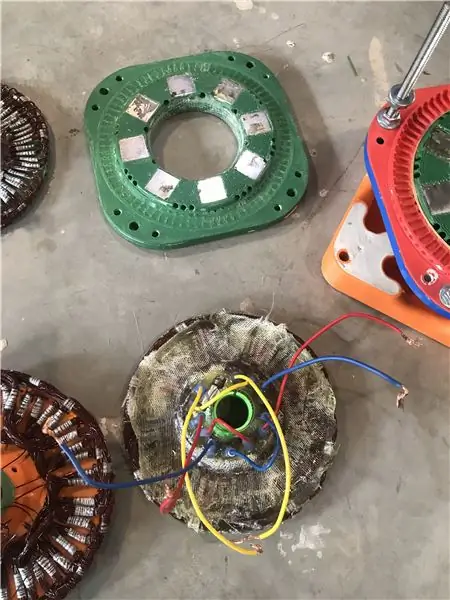
I tråd med temaet mitt om å prøve å forklare hva jeg har gjort, og hvorfor det virket som en god idé den gangen, vil statoren kreve litt mer plass.
I en PMA er viklingene vanligvis stasjonære, mens de magnetiske enhetene roterer. Dette er ikke alltid tilfelle, men nesten alltid. I en aksial fluksenhet, med forståelse av den grunnleggende "høyre håndsregelen", er det forstått at enhver leder som støter på et roterende magnetfelt, vil ha strøm og spenning generert mellom endene av ledningen, med mengden nyttig strøm som er proporsjonal til feltets retning. Hvis feltet beveger seg parallelt med ledningen (f.eks. I en sirkel rundt rotasjonsaksen), vil det ikke bli generert noen nyttig strøm, men det vil genereres betydelige virvelstrømmer som motstår bevegelsen av magnetene. Hvis ledningen går vinkelrett, vil den høyeste spenningen og strømutgangen nås.
En annen generalisering er at rommet i statoren, gjennom hvilken magnetfluksen passerer gjennom rotasjonen, for maksimal effekteffekt, bør fylles med så mye kobber, alt radielt lagt, som mulig. Dette er et problem for aksialstrømningssystemer med liten diameter, ettersom området i kobber nær akselen i denne saken er en brøkdel av området i ytterkanten. Det er mulig å få 100% kobber på det indre området som magnetfeltet støter på, men innenfor denne geometrien får du bare 50% på ytterkanten. Dette er en av de sterkeste årsakene til å holde seg borte fra aksial fluxdesign som er for liten.
Som jeg har sagt tidligere, handler denne instruksen ikke om hvordan jeg ville gjøre det igjen, det er mer å peke i noen retninger som virker lovende, og vise frem noen av hullene som kan nås på denne veien.
Ved utformingen av statoren ønsket jeg å gjøre den så fleksibel som mulig når det gjelder utgangseffekt per rpm, og jeg ønsket at den skulle være 3 -faset. For maksimal effektivitet, ved å minimere virvelstrømmer som genereres, bør ethvert "ben" (hver side av en spole betraktes som et "ben") bare støte på en magnet om gangen. Hvis magneter er nær hverandre, eller berører som tilfellet er i mange høyeffektive rc -motorer, vil det i løpet av tiden "benet" passerer gjennom magnetflux -reversering, utvikles betydelige virvelstrømmer. I motorapplikasjoner betyr dette ikke så mye, ettersom spolen får strøm fra kontrolleren når den er på de riktige stedene.
Jeg dimensjonerte magnetoppsettet med tanke på disse konseptene. De åtte magneter i matrisen er hver 1 "på tvers, og mellomrommet mellom dem er 1/2". Dette betyr at et magnetisk segment er 1,5 "langt, og det har plass til 3 x 1/2" "ben". Hvert "ben" er en fase, så når som helst ser det ene benet nøytral fluks, mens de to andre ser akskerende fluks og fallende fluks. Perfekt 3 -faset utgang, men ved å gi nøytralpunktet så mye plass (for å minimere virvelstrømmer), og ved å bruke firkantede (eller kakeformede) magneter, flyter flussen nesten tidlig, holder seg høy og faller deretter raskt til null. Denne typen utgang tror jeg kalles trapezformet, og kan være vanskelig for noen kontrollere jeg forstår. 1 "runde magneter i samme apparat ville gi mer av en sann sinusbølge.
Vanligvis har disse hjemmebygde generatorene blitt bygget ved hjelp av "spoler", smultringformede trådbunter, hvor hver side av smultringen er et "ben" og antall spoler kan festes sammen, i serie eller parallelt. Donuts er arrangert i en sirkel, med sentrene på linje med midten av magnetbanen. Dette fungerer, men det er noen problemer. Et problem er at siden lederne ikke er radielle, passerer en stor del av lederen ikke ved 90 grader til magnetfeltet, så det genereres virvelstrømmer som vises som varme i spolen og motstand mot rotasjon i magnetarrayene. Et annet problem er at fordi lederne ikke er radiale, pakker de ikke like godt sammen. Utgangen er direkte proporsjonal med mengden ledning du kan passe inn i dette rommet, så effekten reduseres med ikke -radiale "ben". Selv om det ville være mulig og noen ganger er gjort i kommersielle design, krever det en dobbelt så mye endevikling som en serpentinvikling der toppen av det ene benet er forbundet med toppen av det ene benet for å spole en spole med radiale "ben, sammenføyde topp og bunn. neste passende ben, og deretter er bunnen av det benet forbundet med det neste passende benet, og videre og videre.
Den andre store faktoren i aksialstrømgeneratorer av denne typen (roterende magneter over og under stator) er gap mellom platene. Dette er et kubelovforhold, ettersom du reduserer avstanden mellom platene med 1/2, den magnetiske fluxtettheten øker med 8x. Jo tynnere du kan lage din stator, jo bedre!
Med dette i bakhodet laget jeg en 4 -flikket svingete jig, satte opp et system for måling av omtrent 50 fot trådtråder og pakket jiggen 6 ganger, og lagde trådbunter med en diameter på 6 mm. Disse passer jeg på den blå avstandsringen, og binder dem ned gjennom hullene slik at trådendene kom ut på baksiden. Dette var ikke lett. Det ble hjulpet litt ved å ha teipet buntene forsiktig så de ikke var løse, og ved å ta meg tid og bruke et glatt treformingsverktøy for å skyve ledningene på plass. Når de alle var festet på plass, ble den blå avstandsringen plassert i den største av de lysegrønne karene, og ved hjelp av det mørkegrønne smultringformingsverktøyet, på den andre siden av det lysegrønne karet, presset forsiktig flatt med en benkeskrue. Dette formbadekaret har et spor for å sno båndtrådene. Dette tar tid og tålmodighet mens du roterer forsiktig omtrent 1/5 omdreining, trykker, roterer og fortsetter. Dette danner disken flat og tynn, samtidig som endeviklingene kan stables. Du vil kanskje legge merke til at min 4 -flikede vikling har rette "ben", men de indre og ytre forbindelsene er ikke runde. Dette skulle gjøre det lettere for dem å stable. Det fungerte ikke så bra. Hvis jeg gjorde det igjen, ville jeg få innvendig og utvendig endevikling til å følge sirkulære baner.
Etter å ha fått det flatt og tynt, og kantene pakket ned, viklet jeg et flatt bånd rundt kanten for å komprimere det, og et annet opp, ned og rundt hvert ben og deretter til det ved siden av det også. Etter at dette er gjort kan du fjerne festetrådene og bytte til det mindre pressekaret og gå tilbake til skruen og trykke den så tynn og flat som mulig. Når den er flat, fjerner du den fra presskaret. I stedet for den komplekse prosessen med forsiktig voksing og belegg av former som dette med frigivelsesforbindelser, bruker jeg vanligvis bare et par lag med strekkfolie (fra kjøkkenet). Legg et par lag i bunnen av formen og legg glassfiber på strekkfolien. Legg deretter til statormonteringsrøret, som passer til toppen av det lysegrønne formbadet, men har laget av strekkfolie og glassfiber mellom. Deretter legger du til statorviklingen tilbake på plass for å skyve ned både strekkomslaget og glassfiber og låse statormonteringsrøret på plass. Gå deretter tilbake til skruen og trykk flat igjen. Når den passer godt inn i karet, med strekkfolien og glassfiber smykket inn, blir glassfiberduk tilsatt (med et hull i midten for statormonteringsrøret).
Nå er det klart å helle bindematerialet, epoksy eller polyesterharpiks brukes ofte. Før dette er gjort, er nøye forberedelser viktig, ettersom du først kan starte denne prosessen. Jeg brukte en 3D -trykt bunnplate jeg tidligere hadde laget, med et 1 "hull i midten og en flat plate rundt det. Jeg brukte et 16" stykke 1 "aluminiumsrør, som statormonteringsrøret ville passe over og være holdt vinkelrett på den flate platen. Den grønne formbadekaret, statorviklingen og statormonteringsrøret ble skyvet ned for å sitte på den flate platen. Før jeg blandet epoxy, la jeg først 4 biter av krympepapir og plasserte et femte stykke forsiktig på mørkegrønn formende doughnut, så den ville ha minimale rynker i ansiktet mot statorviklingen. Etter å ha blandet epoksyet og hellet den på glassfiberduken, la jeg forsiktig ned strekkfolien rundt 1 "-røret og la den grønne danner ring på toppen av den. Jeg hadde også forberedt et par gamle bremsrotorer, som ga litt vekt, og satt pent på den grønne formende smultringen. Etter dette la jeg en omvendt gryte på toppen av bremserotorene, og på toppen av gryten stablet jeg omtrent 100 kg ting. Jeg forlot dette i 12 timer, og det kom ut ca 4-6 mm tykt.
Trinn 4: Testing og sensorer
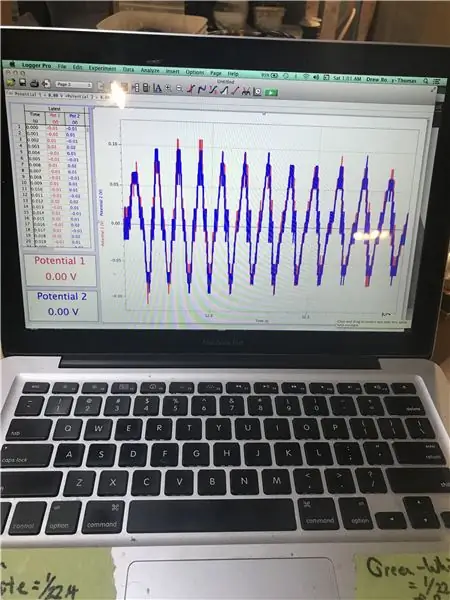
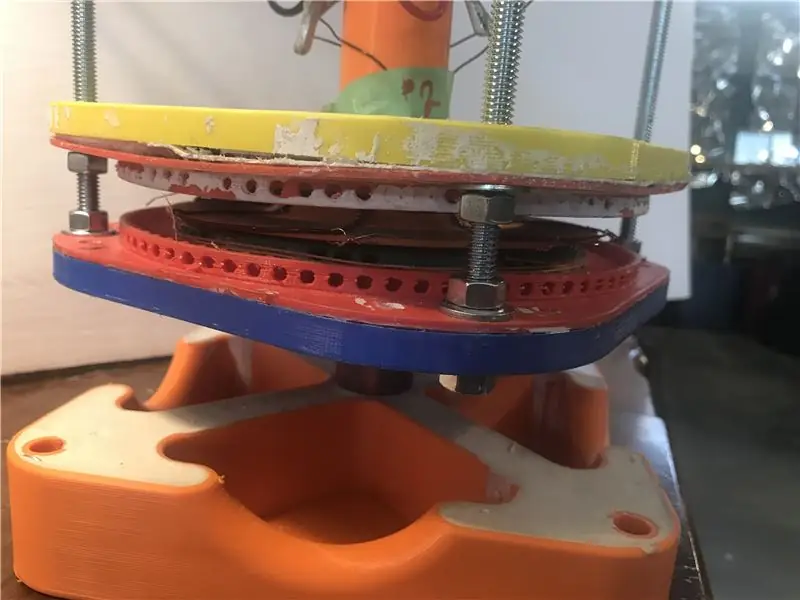
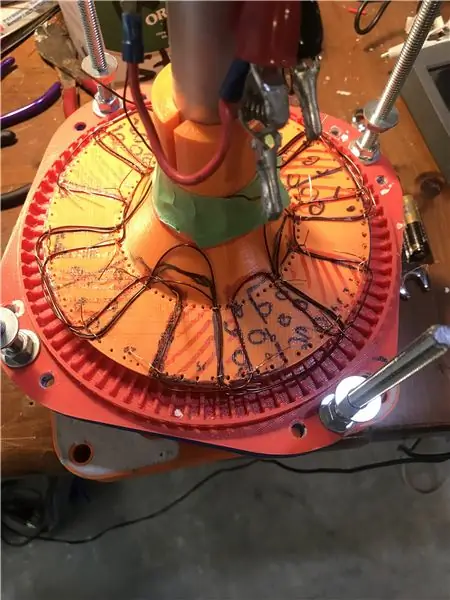
Det er en rekke målbare innganger og utganger fra dynamoen, og å måle dem alle, samtidig er ikke lett. Jeg er veldig heldig som har noen verktøy fra Vernier som gjør dette mye enklere. Vernier lager produkter på utdanningsnivå, ikke sertifisert for industrielt bruk, men veldig nyttig for eksperimenter som meg selv. Jeg bruker en Vernier datalogger, med en rekke plug and play -sensorer. På dette prosjektet bruker jeg hallbaserte strøm- og spenningssonder, for å måle generatorens utgang, en optisk sensor for å gi generatorens hastighet og en lastcelle for å måle dreiemomentinngang. Alle disse instrumentene blir samplet omtrent 1000 ganger i sekundet og registrert på min bærbare datamaskin, ved hjelp av Vernier -loggeren som en AD -passthrough -enhet. På min bærbare datamaskin kan den tilhørende programvaren kjøre sanntidsberegninger basert på inngangene, kombinere dreiemoment- og hastighetsdata for å gi sanntids inngangsakseleffekt i watt og utdata i sanntid i elektriske watt. Jeg er ikke ferdig med denne testen, og innspill fra noen som har en bedre forståelse ville være nyttig.
Et problem jeg har er at denne dynamoen virkelig er et sideprosjekt, og derfor vil jeg ikke bruke for mye mer tid på det. Som det er, tror jeg at jeg kan bruke det til en kontrollerbar belastning for min VAWT -forskning, men til slutt vil jeg gjerne jobbe med folk for å foredle det, slik at det er en effektiv match for turbinen min.
Da jeg begynte med VAWT -forskning for omtrent 15 år siden, skjønte jeg at testing av VAWT og andre drivere er mer komplekst enn de fleste skjønner.
Et hovedproblem er at energien som er representert i en væske i bevegelse, er eksponentiell for bevegelseshastigheten. Dette betyr at når du dobler hastigheten til en strøm, øker energien i strømmen 8x (den er i terninger). Dette er et problem, ettersom dynamoer er mer lineære og generelt, hvis du dobler turtallet på en generator, får du omtrent 2x watt.
Denne grunnleggende mismatchen mellom turbinen (energiinnsamlingsenhet) og dynamoen (akseleffekt til nyttig elektrisk kraft) gjør det vanskelig å velge en generator for et vindturbin. Hvis du velger en dynamokamp for vindturbinen din som vil generere mest mulig kraft fra 20 km/t vind, vil det ikke sannsynligvis begynne å snu før 20-25 km/t ettersom belastningen på turbinen fra dynamoen vil være for høy. Med den dynamikkampen, når vinden er over 20 km, vil ikke bare turbinen fange opp en brøkdel av energien som er tilgjengelig i vinden med høyere hastighet, kan turbinen overfaste og bli skadet ettersom belastningen fra dynamoen ikke er høy nok.
I løpet av det siste tiåret har en løsning blitt mer økonomisk på grunn av prisfallet på kontrollelektronikk. I stedet for å prøve å matche en rekke hastigheter, beregner designeren maksimalhastigheten enheten er ment å operere med, og velger en generator basert på mengden energi og ideell hastighet for turbinen med den hastigheten, eller litt over. Denne dynamoen hvis den er koblet til belastningen, vil normalt gi for mye dreiemoment ved lavt turtallsområde, og den overbelastede turbinen vil ikke fange all energien den kan ha hvis den var riktig belastet. For å opprette riktig belastning, legges det til en kontroller som kobler dynamoen for en kort stund fra den elektriske lasten, slik at turbinen kan øke hastigheten til riktig hastighet, og dynamoen og lasten kobles til igjen. Dette kalles MPPT (Multi Power Point Tracking). Kontrolleren er programmert slik at etter hvert som turbinhastigheten endres (eller dynamospenningen stiger), blir dynamoen koblet eller frakoblet, tusen ganger i sekundet eller så, for å matche belastningen som er programmert for den hastigheten eller spenningen.
Anbefalt:
Ta flotte bilder med en iPhone: 9 trinn (med bilder)
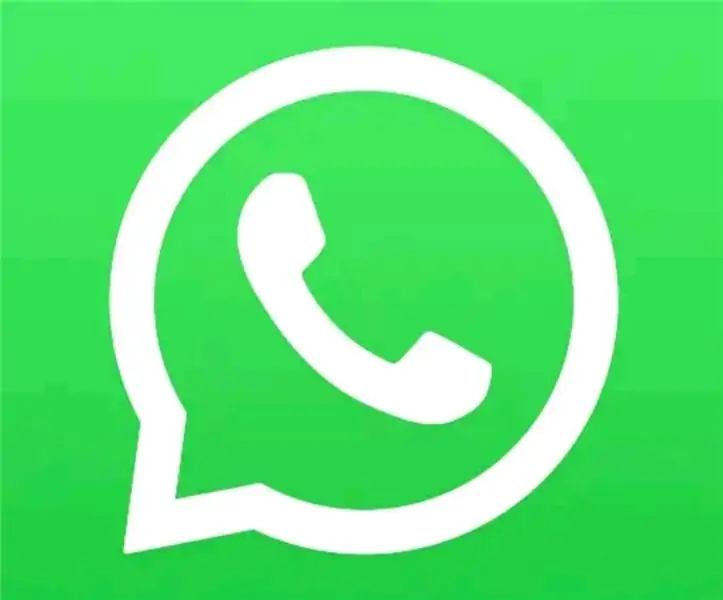
Ta flotte bilder med en iPhone: De fleste av oss har med oss en smarttelefon overalt i disse dager, så det er viktig å vite hvordan du bruker smarttelefonkameraet ditt til å ta flotte bilder! Jeg har bare hatt en smarttelefon i et par år, og jeg har elsket å ha et greit kamera for å dokumentere ting jeg
Raspberry Pi -eske med kjølevifte med CPU -temperaturindikator: 10 trinn (med bilder)
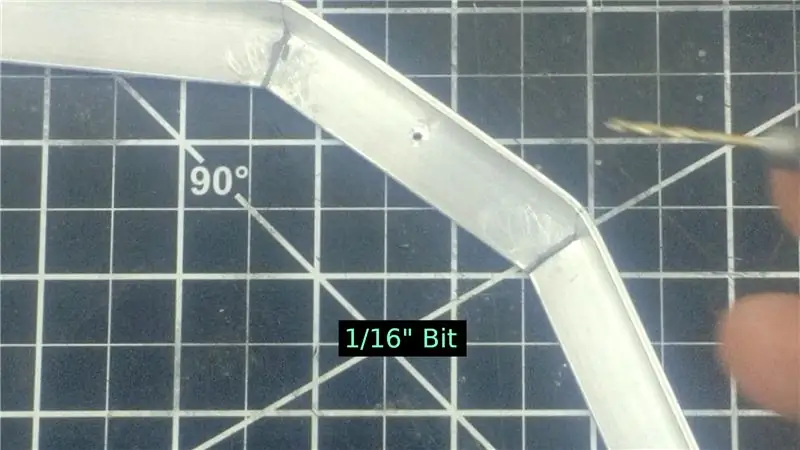
Raspberry Pi-eske med kjølevifte med CPU-temperaturindikator: Jeg hadde introdusert bringebær pi (heretter som RPI) CPU-temperaturindikatorkrets i det forrige prosjektet. Kretsen viser ganske enkelt RPI 4 forskjellige CPU-temperaturnivå som følger.- Grønn LED ble slått på når CPU -temperaturen er innenfor 30 ~
Slik gjør du det: Installere Raspberry PI 4 Headless (VNC) med Rpi-imager og bilder: 7 trinn (med bilder)
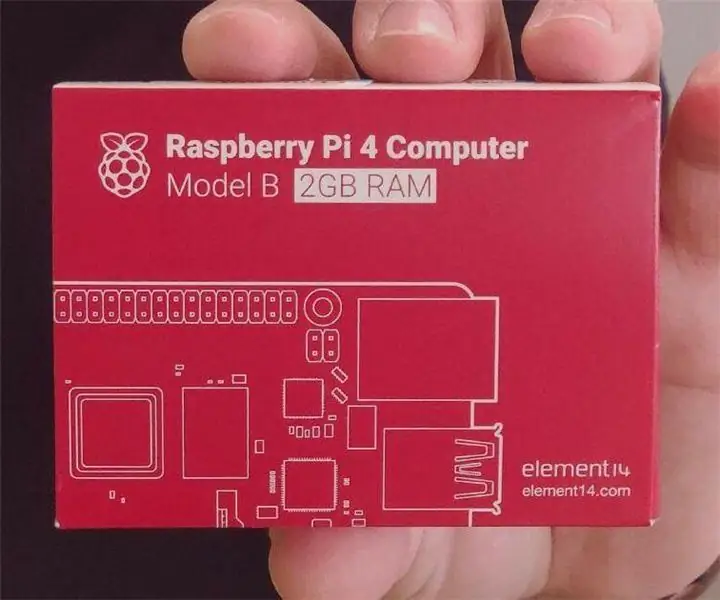
Howto: Installere Raspberry PI 4 Headless (VNC) Med Rpi-imager og bilder: Jeg planlegger å bruke denne Rapsberry PI i en haug med morsomme prosjekter tilbake i bloggen min. Sjekk det gjerne ut. Jeg ønsket å begynne å bruke Raspberry PI igjen, men jeg hadde ikke tastatur eller mus på min nye plassering. Det var en stund siden jeg konfigurerte en bringebær
Plattformspill med uendelige nivåer på GameGo med Makecode Arcade: 5 trinn (med bilder)
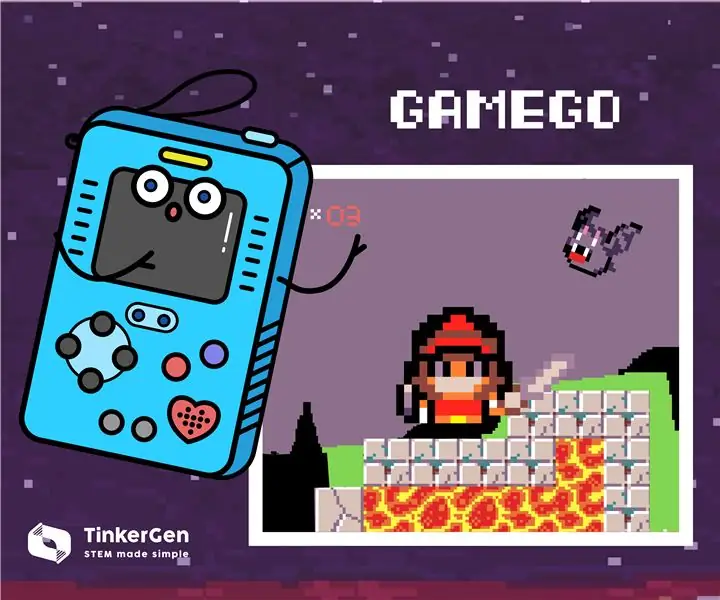
Plattformspill med uendelige nivåer på GameGo med Makecode Arcade: GameGo er en Microsoft Makecode -kompatibel retro spillkonsoll utviklet av TinkerGen STEM education. Den er basert på STM32F401RET6 ARM Cortex M4 -brikken og laget for STEM -lærere eller bare folk som liker å ha det gøy med å lage retro videospill
Slik demonterer du en datamaskin med enkle trinn og bilder: 13 trinn (med bilder)
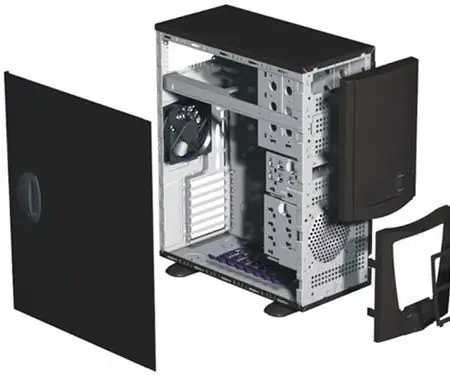
Slik demonterer du en datamaskin med enkle trinn og bilder: Dette er en instruksjon om hvordan du demonterer en PC. De fleste grunnkomponentene er modulære og fjernes lett. Det er imidlertid viktig at du er organisert om det. Dette vil bidra til å hindre deg i å miste deler, og også i å gjøre monteringen igjen