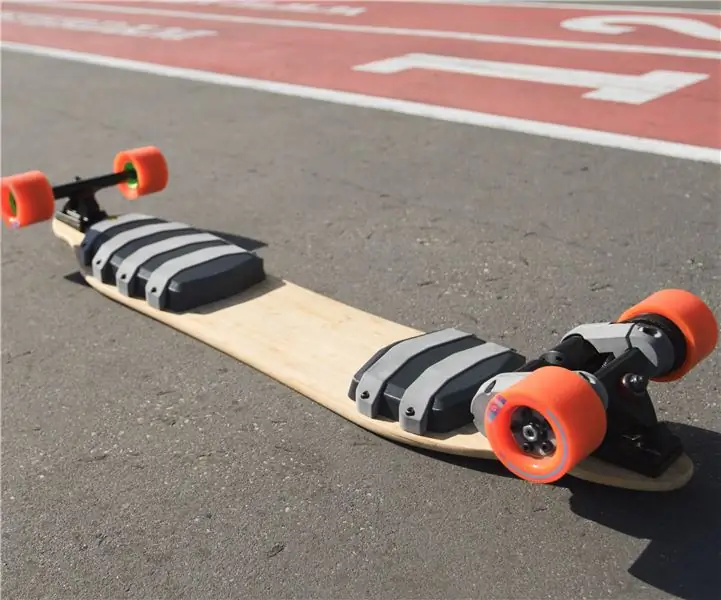
Innholdsfortegnelse:
2025 Forfatter: John Day | [email protected]. Sist endret: 2025-01-23 15:02
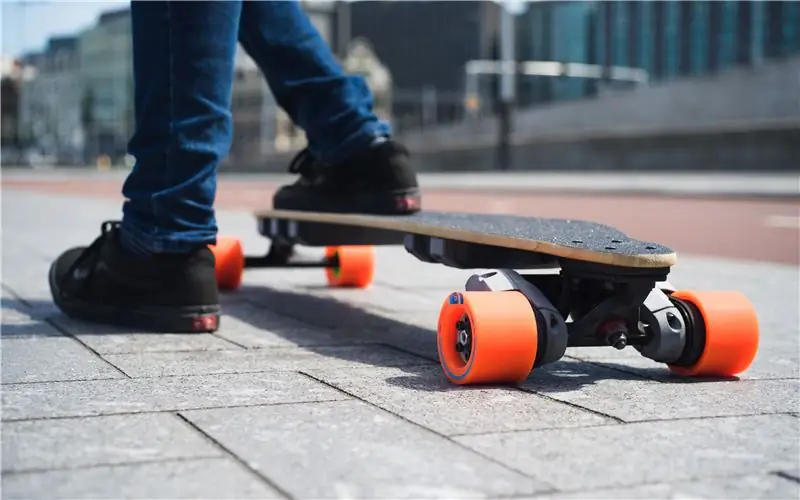
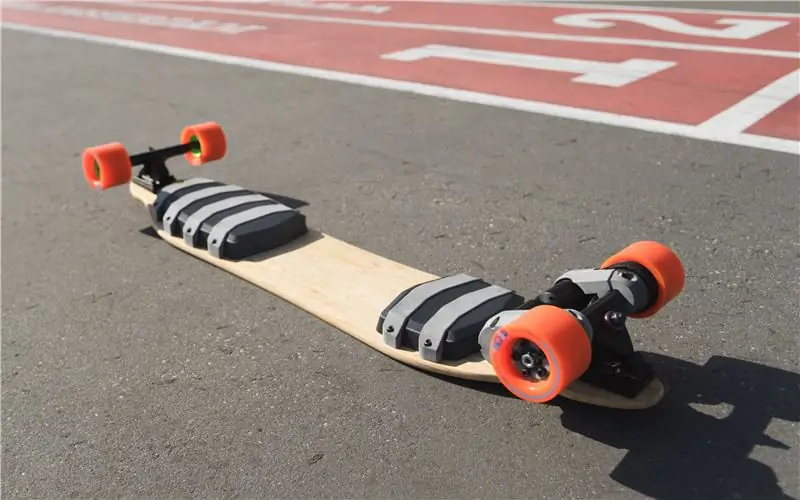
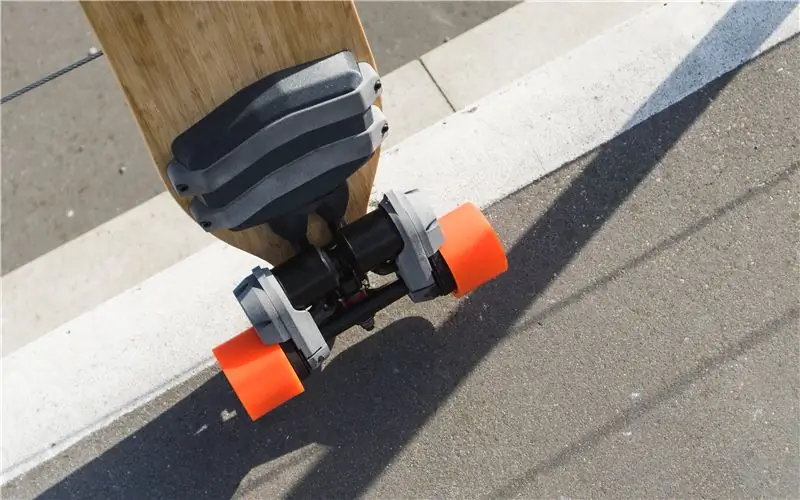
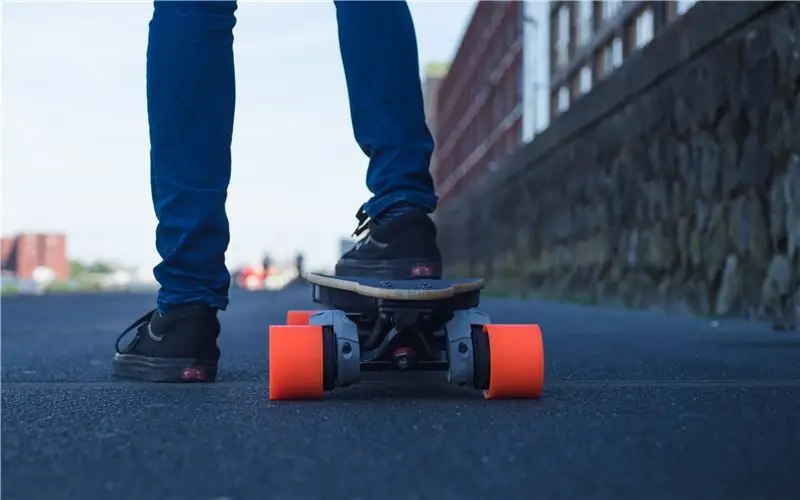
Denne instruksjonsboken er en oversikt over byggeprosessen for Fusion E-Board som jeg designet og bygde mens jeg jobbet på 3D Hubs. Prosjektet fikk i oppdrag å markedsføre den nye HP Multi-Jet Fusion-teknologien som tilbys av 3D Hubs, og vise frem flere 3D-utskriftsteknologier og hvordan de effektivt kan kombineres.
Jeg designet og bygde et elektrisk motorisert longboard, som kan brukes til korte til moderate reiser eller kombinert med offentlig transport for å tilby et mye større reiseområde. Den har høy toppfart, er svært manøvrerbar og er lett å bære når den ikke er i bruk.
Trinn 1: Designprosess
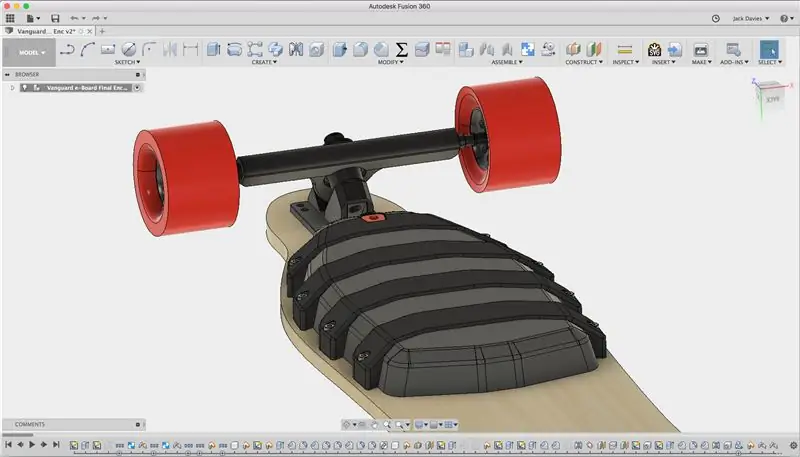
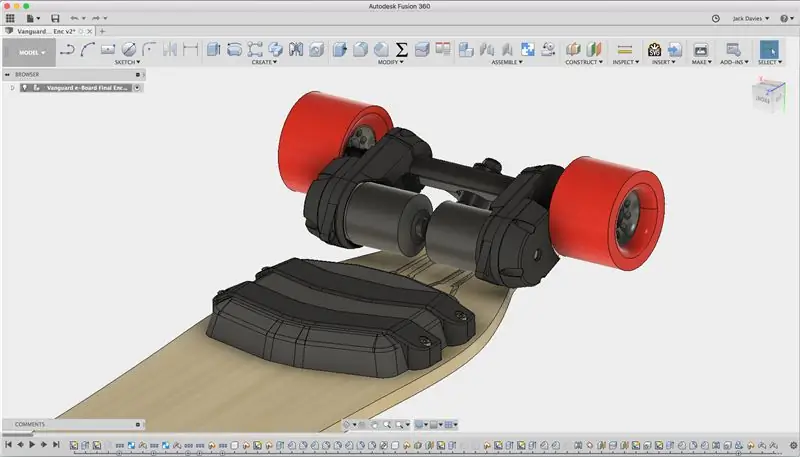
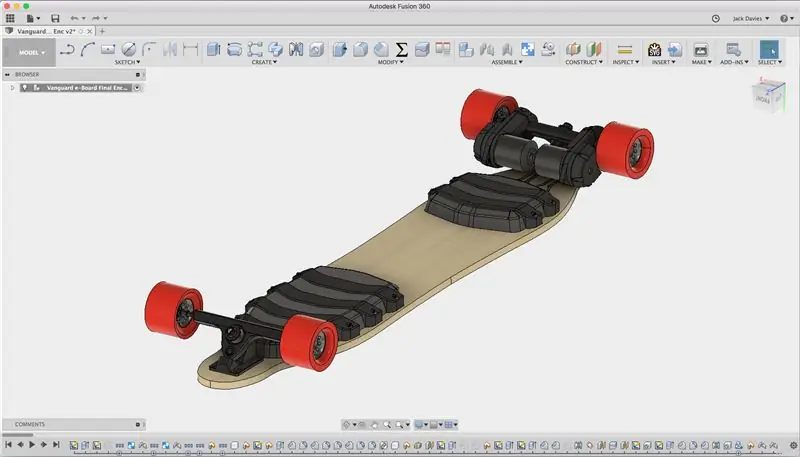
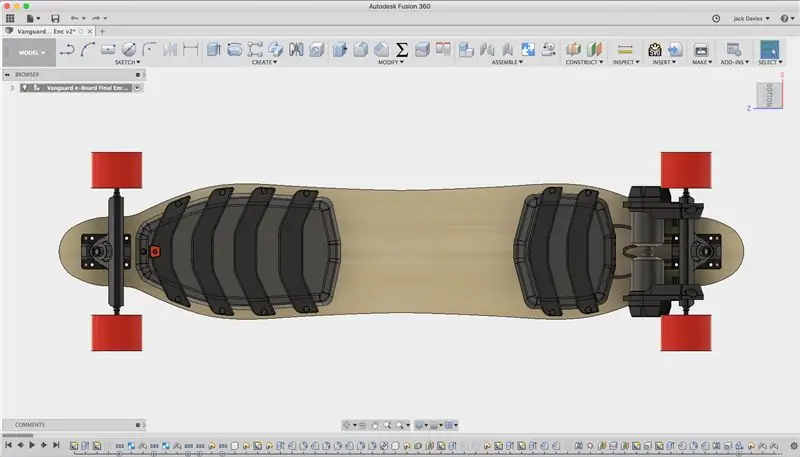
Jeg startet prosjektet med å identifisere de viktigste standardkomponentene i longboardet; lastebiler, dekk og hjul. Disse var utenfor hylledelene, så jeg brukte disse som utgangspunkt for designet. Den første fasen var å designe drivverket, dette inkluderer motorfester, giroppsett og inkluderte noen modifikasjoner av lastebilene. Størrelsen og posisjonen til motorfestene vil diktere størrelsen og plasseringen av skapene, så det var viktig at dette ble fullført først. Jeg beregnet ønsket topphastighet og dreiemomentkrav som deretter gjorde det mulig for meg å velge motorer og batteri til brettet. Utvekslingsforholdet ble også beregnet og remskivestørrelsene ble valgt, sammen med drivremlengden. Dette gjorde at jeg kunne finne ut riktig størrelse på motorfestene som sikret et godt strammet belte.
Det neste trinnet var å designe batteri- og hastighetskontrolleren (ESC). Det valgte dekket består hovedsakelig av bambus, så det er ganske fleksibelt og bøyer seg vesentlig i midten. Dette har fordeler med å være behagelig å kjøre, ettersom det absorberer støtene i veien og ikke overfører dem til rytteren. Imidlertid betyr dette også at et delt kabinett er nødvendig for å huse batteriet og elektronikken, ettersom et kabinett i full lengde ikke ville kunne bøye seg med brettet og ville komme i kontakt med bakken under drift. De elektroniske hastighetskontrollerne (ESC) ble plassert nærmest motorene på grunn av elektriske begrensninger. Fordi motorene er festet via lastebilene, endres posisjonen under svinger, så kabinettet måtte være designet for å tillate klaring av motorene.
Batterisystemet ble plassert i den andre enden av dekk og inneholdt elektronikken knyttet til strøm. Dette inkluderte batteripakken, som består av 20 litiumion 18650 celler, batteristyringssystemet, av/på -bryter og ladekontakt.
Jeg brukte Autodesk Fusion360 for hele designprosessen, denne programvaren gjorde det mulig for meg å raskt modellere komponenter inne i hovedmonteringen, noe som fremskyndet utviklingstiden betraktelig. Jeg brukte også simuleringsfunksjonene i Fusion360 for å sikre at delene ville være sterke nok, spesielt motorfestene. Dette gjorde det mulig for meg å faktisk redusere størrelsen på festene, ettersom jeg kunne kontrollere kravene til styrke og nedbøyning og fjerne materiale, samtidig som jeg opprettholdt en passende sikkerhetsfaktor. Etter at designprosessen var fullført, var det veldig enkelt å eksportere de enkelte delene for 3D -utskrift.
Trinn 2: Drivlinje
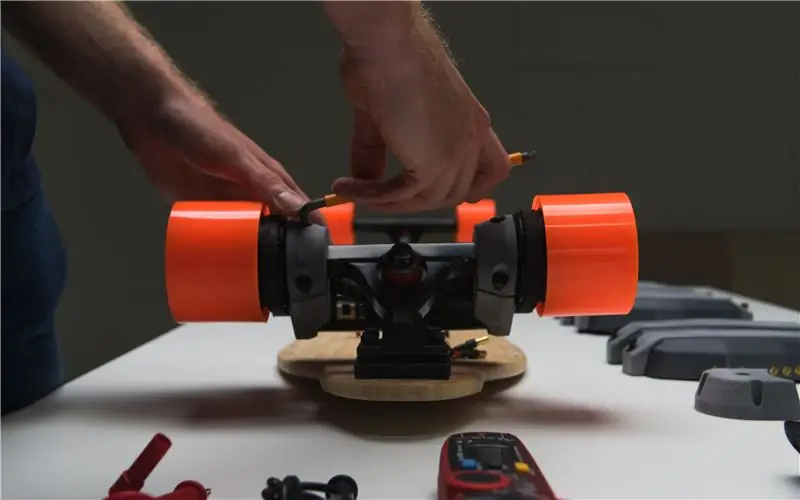
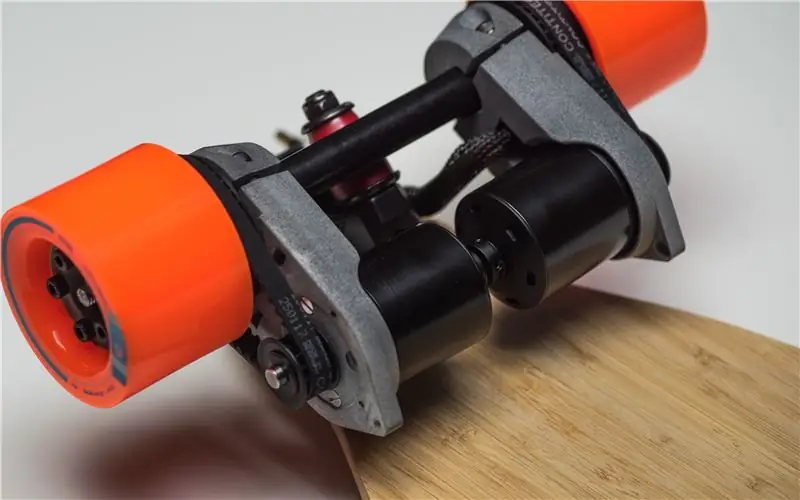
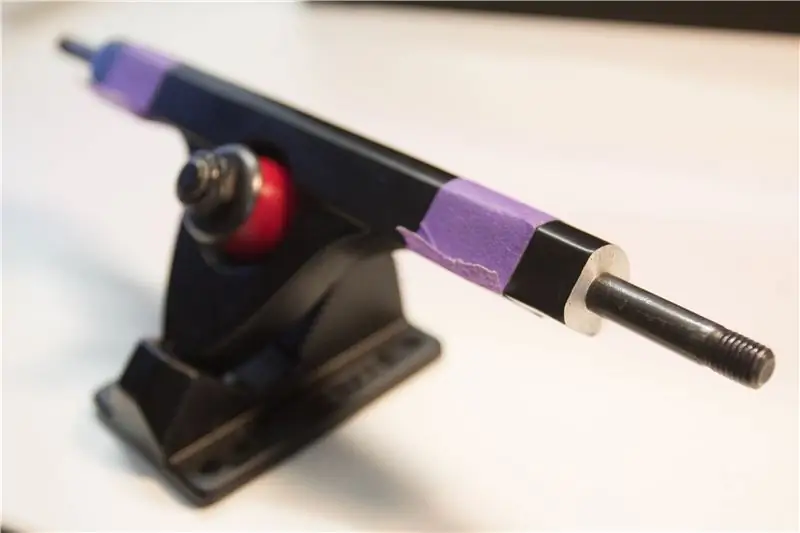
Jeg fullførte byggingen av drivverket først, for å sikre passende klaring for elektronikkhuset. Jeg valgte Caliber -lastebiler å bruke ettersom de har en firkantet profil som var perfekt for å feste motorfestene på. Akselen var imidlertid litt for kort til at de to motorene kunne brukes på samme lastebil, så jeg trengte å forlenge denne slik at hjulene passet.
Jeg oppnådde dette ved å kutte ned noen av aluminiums lastebilkroppen og avsløre mer av stålakslen. Jeg klippet deretter det meste av akselen ned og etterlot rundt 10 mm som jeg deretter kunne trå med en M8 -dør.
En kobler kan deretter skrus på og en annen gjenget aksel legges til som effektivt forlenger akselen. Jeg brukte Loctite 648 festemasse for å sikre koblingen og den nye akselen permanent for å sikre at den ikke skrues av under bruk. Dette tillot de to motorene å passe på lastebilen og ga god klaring for hjulene.
Drivverket ble først og fremst trykt ved hjelp av HP Multi-Jet Fusion-teknologi for å sikre stivhet og styrke under høy akselerasjon og bremsing, der de største kreftene ville bli overført.
En spesiell remskive ble designet for å låse seg fast i bakhjulene, som deretter ble koblet til motorhjulet med et HTD 5M -belte. Et 3D -trykt omslag ble lagt til for å beskytte remskivenheten.
Trinn 3: Ribbe kabinetter
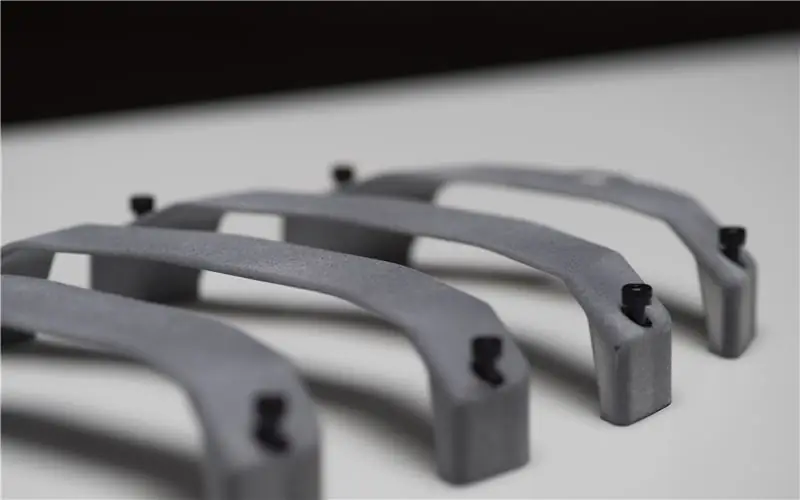
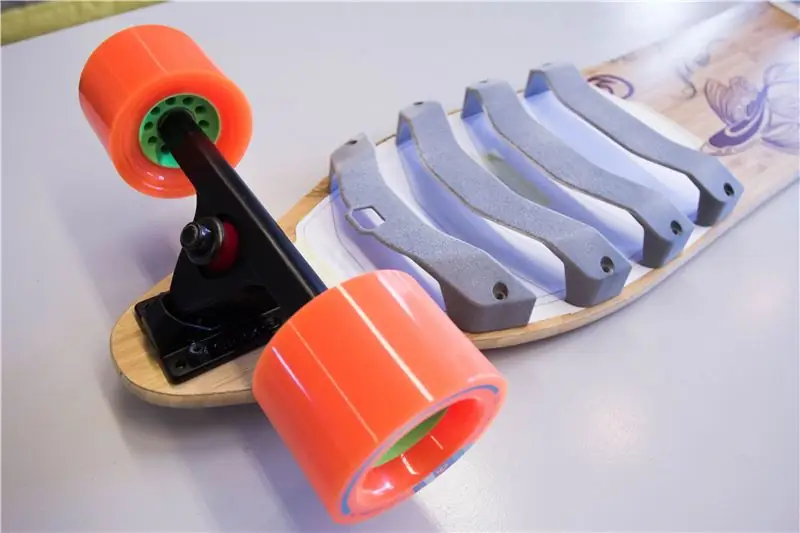
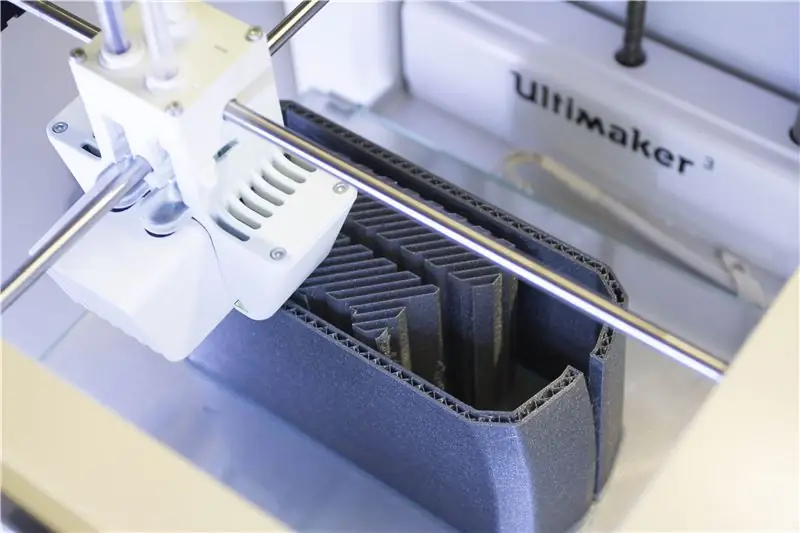
En av de viktigste designbeslutningene jeg tok var å skille skapene, noe som resulterte i et rent utseende og gjorde at det fleksible dekket kunne fungere uten ekstra stivhet fra skapene. Jeg ønsket å formidle de funksjonelle aspektene ved HP Multi Jet Fusion -teknologien, så jeg bestemte meg for å FDM skrive ut hoveddelen av skapene som reduserte kostnadene, og brukte deretter HP -delene til å støtte og feste dem til dekk. Dette ga en interessant estetikk samtidig som den var veldig funksjonell.
FDM -trykte skap ble delt i to for å hjelpe til med utskrift, ettersom støttemateriale kunne fjernes fra utsiden. Splittlinjen ble nøye plassert for å sikre at den ble skjult av HP -delen når den ble festet til brettet. Hull for motorforbindelsene ble lagt til og gullbelagte kulekontakter ble limt på plass til
Gjengede innsatser ble lagt inn i bambusdekket for å feste skapene til brettet, og ble pusset i flukt med brettoverflaten for å sikre at det ikke var noe mellomrom mellom dekket og skapet.
Trinn 4: Elektronikk
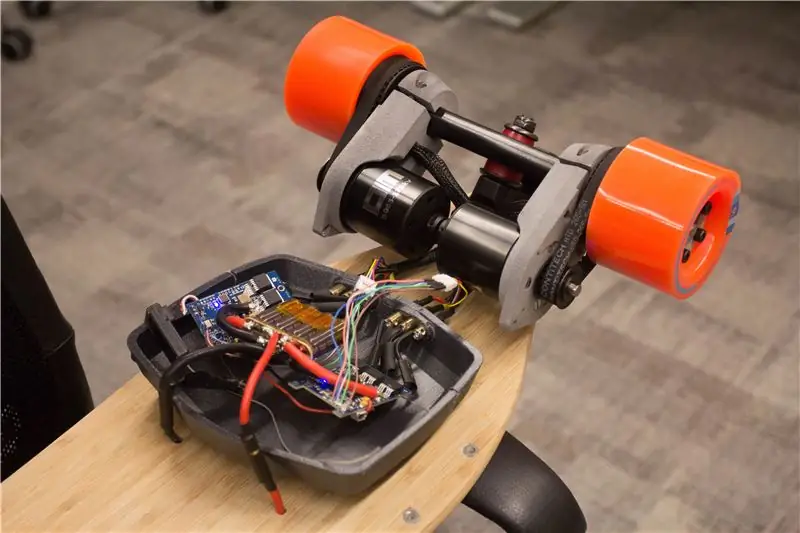
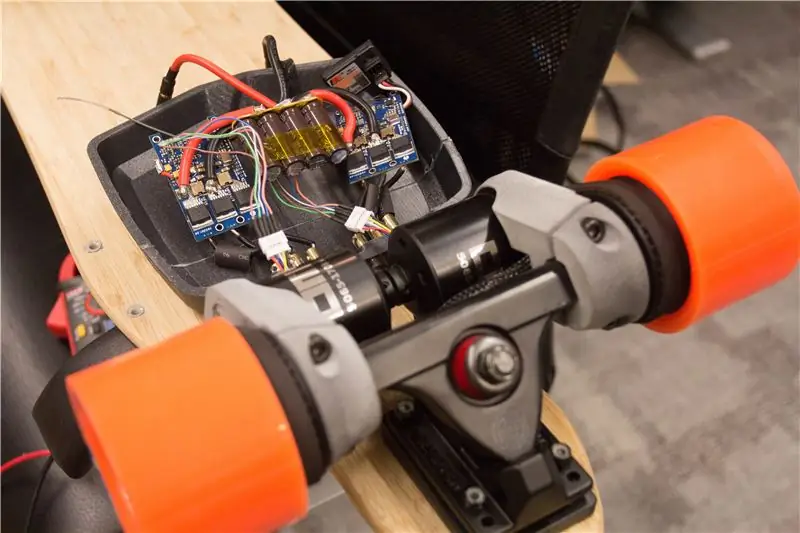
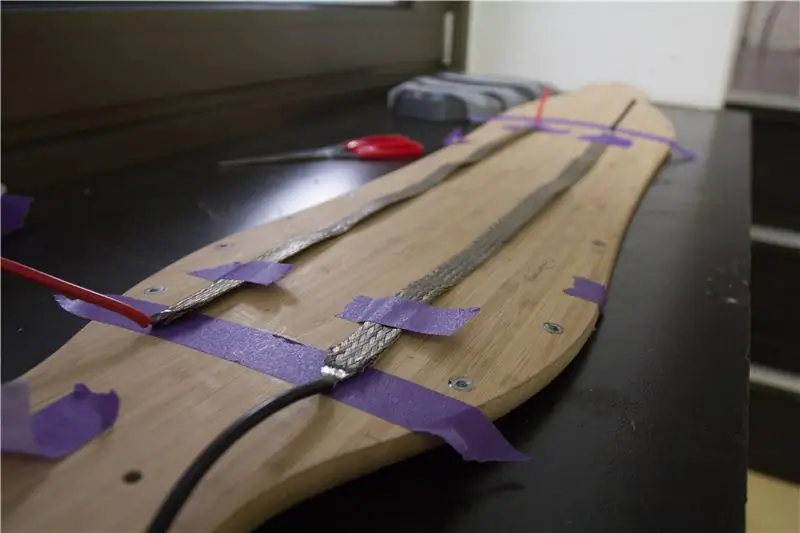
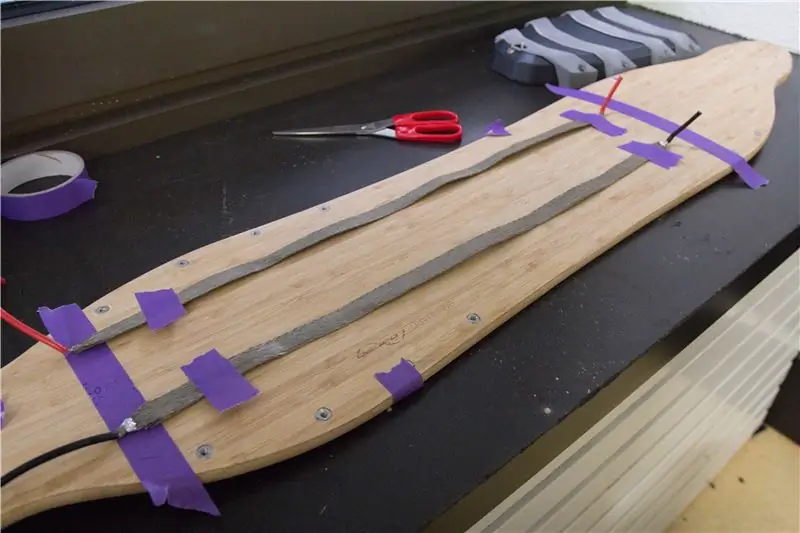
Elektronikken ble nøye valgt for å sikre at brettet var kraftig, men også intuitivt å bruke. Dette brettet kan potensielt være farlig hvis det skulle oppstå feil, så pålitelighet er en veldig viktig faktor.
Batteripakken består av 20 individuelle 18650 litiumionceller som er punktsveiset sammen for å danne en 42v pakning. 2 celler er sveiset parallelt og 10 i serie; cellene jeg brukte var Sony VTC6. Jeg brukte en punktsveiser til å sveise nikkeltappene for å danne pakken, ettersom lodding skaper for mye varme som kan skade cellen.
Strømmen fra batterihuset ble overført til hastighetsregulatorboksen ved hjelp av flat flettet kabel som ble ført like under gripebåndet på oversiden av dekket. Dette tillot at kablene ble "skjult" og eliminerte behovet for å føre kabler på undersiden som ville ha sett stygg ut.
Siden dette er et dobbeltmotorbrett, kreves det to hastighetskontrollere for å kontrollere hver motor uavhengig. Jeg brukte VESC -hastighetskontrolleren for denne bygningen, som er en kontroller som er spesielt designet for elektriske skateboards, noe som gjør den veldig pålitelig for denne bruken.
Motorene som brukes er 170kv 5065 utløpere som kan produsere 2200W hver, noe som er mye kraft for dette brettet. Med det nåværende giroppsettet er brettets maksimal hastighet rundt 35MPH, og akselererer veldig raskt.
Den siste fasen var å lage en fjernkontroll for å styre brettet. Et trådløst system ble foretrukket på grunn av den enklere betjeningen. Imidlertid var det viktig å sikre høy pålitelighet for overføring da et fall i kommunikasjonen kan ha alvorlige sikkerhetsproblemer, spesielt ved høye hastigheter. Etter å ha testet noen få radiooverføringsprotokoller bestemte jeg meg for at 2,4 GHz radiofrekvens ville være den mest pålitelige for dette prosjektet. Jeg brukte en RC -bilsender fra hyllen, men reduserte størrelsen betydelig ved å overføre elektronikken til et lite håndholdt etui som var 3D -trykt.
Trinn 5: Ferdig brett og reklamevideo
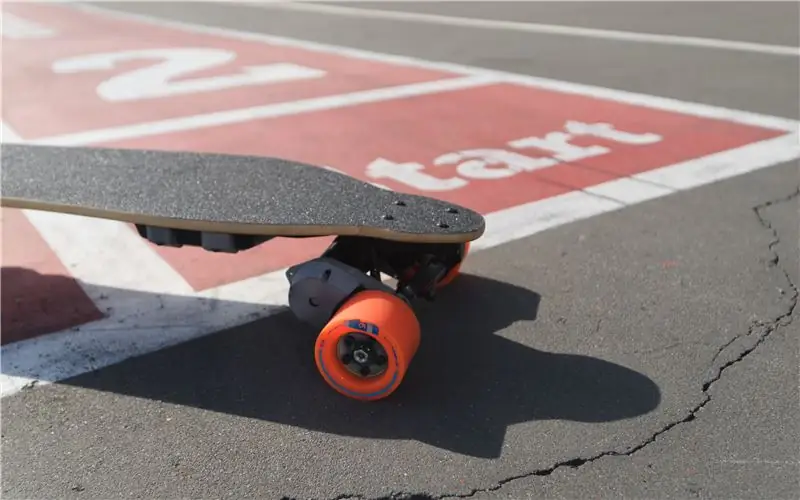
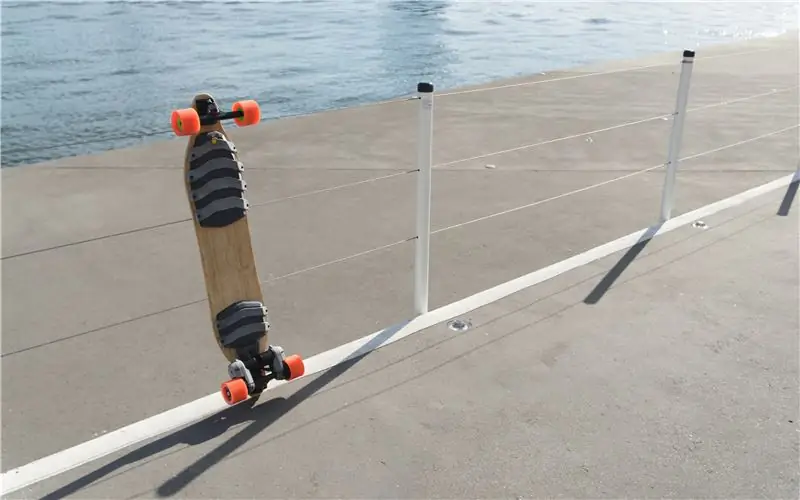
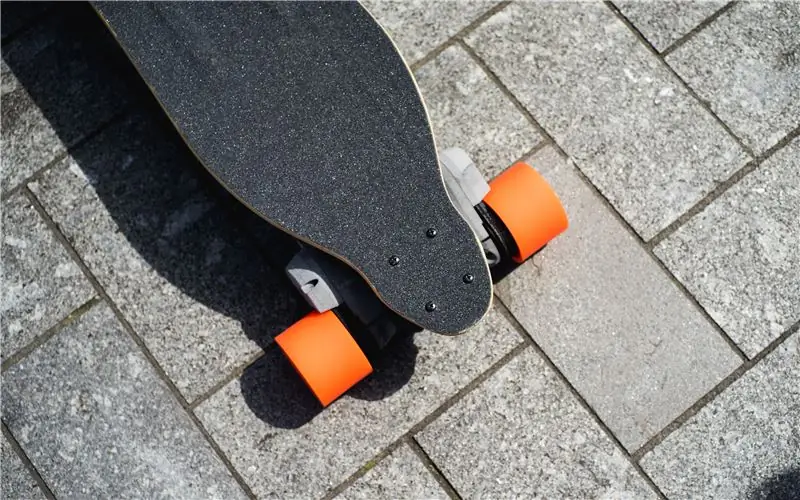
Prosjektet er nå ferdig! Vi laget en ganske fantastisk video av brettet i aksjon, du kan sjekke det ut nedenfor. Stor takk til 3D -hubber for at jeg gjorde dette prosjektet - sjekk dem her for alle dine 3D -utskriftsbehov! 3dhubs.com
Anbefalt:
Kontroller kraftig elektrisk skateboard E-Bike 350W DC-motor ved hjelp av Arduino og BTS7960b: 9 trinn
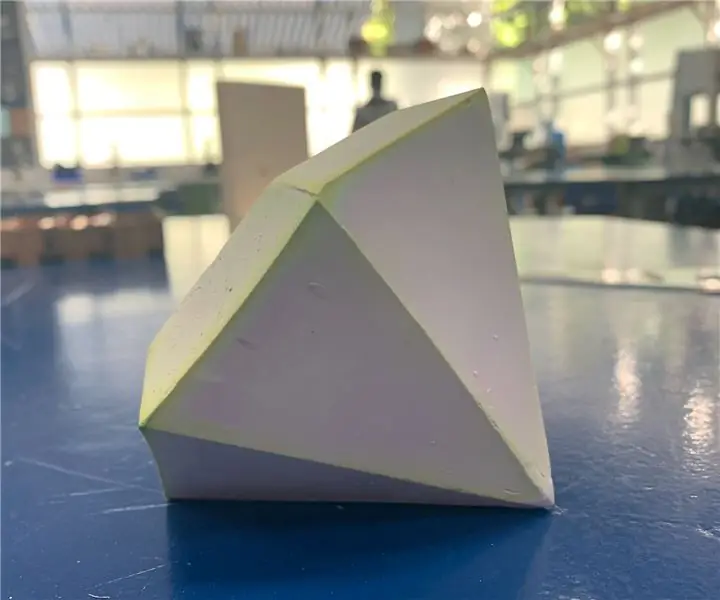
Kontroller kraftig elektrisk skateboard E-Bike 350W DC-motor ved hjelp av Arduino og BTS7960b: I denne opplæringen skal vi lære å kontrollere en DC-motor ved hjelp av Arduino og Dc driver bts7960b. Motoren kan være en 350W eller bare en liten leketøy arduino DC-motor så lenge strømmen ikke overstiger BTS7960b -driveren Maksimal strøm. Se videoen
Speedboard: Elektrisk skateboard: 5 trinn
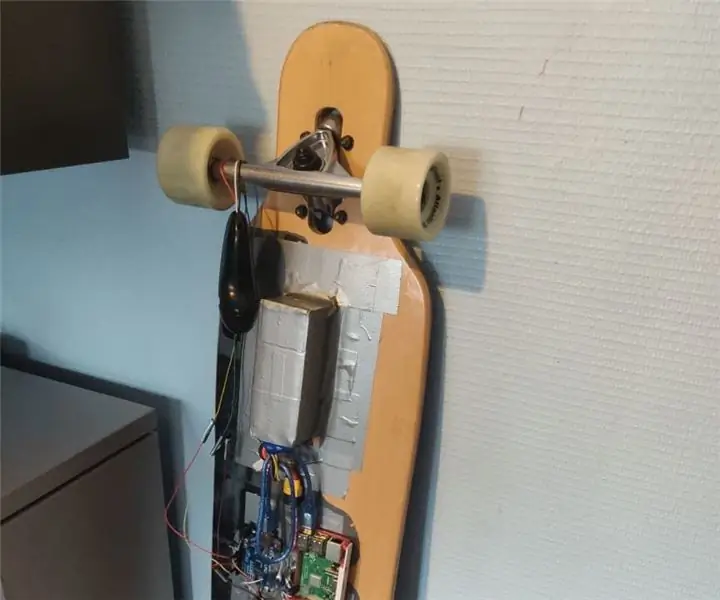
Speedboard: Elektrisk skateboard: Hei! Jeg er en MCT College Student fra Howest i Belgia. I dag vil jeg gi deg en trinnvis guide for hvordan du lager et elektrisk skateboard med bringebærpi og arduino. Jeg ble inspirert til å lage dette prosjektet av en berømt youtuber kalt Casey Neistat
Fjernkontroll for elektrisk skateboard: 7 trinn
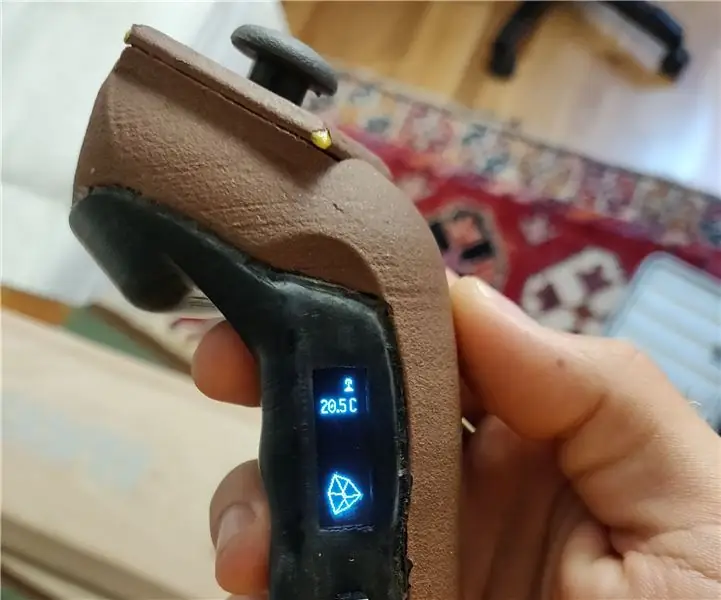
Elektrisk skateboard -fjernkontroll: Lag en elektrisk skateboard -fjernkontroll, i JAVASCRIPT! Bli med på reisen min, forhåpentligvis vil du lære noe. Dette vil ikke være en trinnvis opplæring. Det blir mer et utstillingsvindu hva jeg har brukt, hvordan jeg gjorde det, og jeg er sikker på at du kan gjøre det til. Jeg anbefaler til og med
Kilometerteller for elektrisk skateboard: 5 trinn
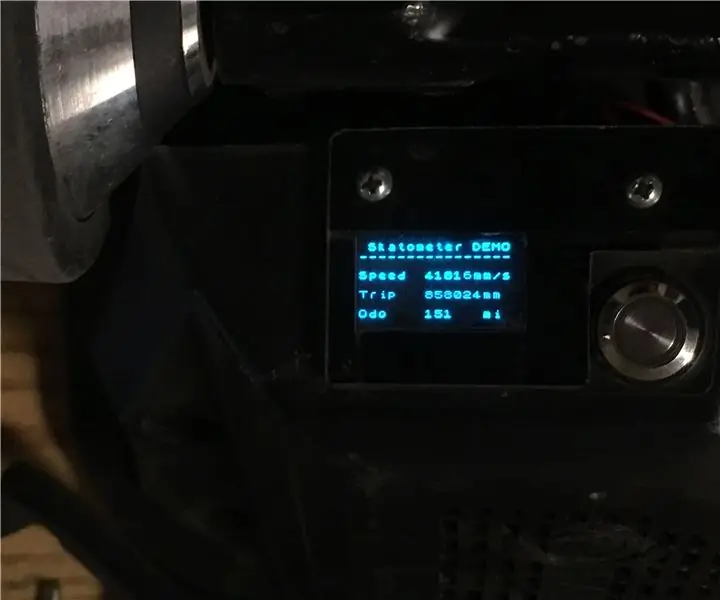
Kilometerteller for elektrisk skateboard: introduksjon De fleste high-end elektriske skateboardene rundt tusen dollar kommer med en telefonapp som viser informasjon om sanntid på skateboard, og dessverre kommer de mer kostnadseffektive skateboardene fra Kina ikke med dem. Så hvorfor ikke
DIY elektrisk skateboard: 14 trinn (med bilder)
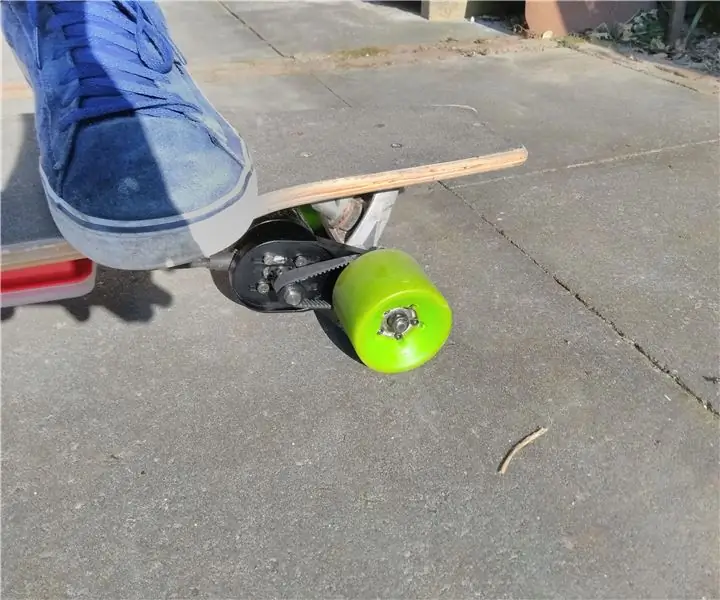
Diy Electric Skateboard: Etter 2 års forskning har jeg bygget mitt første elektriske skateboard. Siden jeg har sett en instruks om hvordan du bygger ditt eget elektriske skateboard, har jeg vært forelsket i DIY elektriske skateboard. Å lage ditt eget elektriske skateboard er en form for