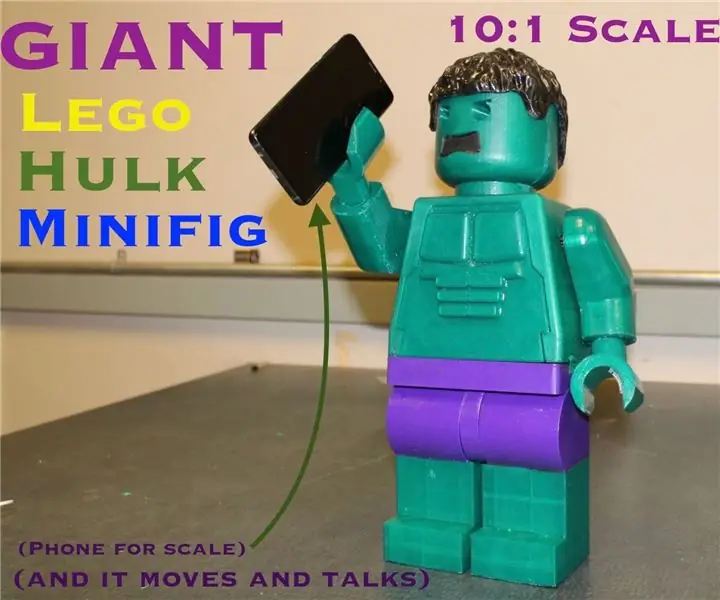
Innholdsfortegnelse:
- Trinn 1: Materialregning
- Trinn 2: Del og erobre
- Trinn 3: [Valgfritt] Design og 3D -utskrift: Design
- Trinn 4: Design og 3D -utskrift: 3D -utskrift
- Trinn 5: [Valgfritt] Utjevning av 3D -utskrifter
- Trinn 6: [Delvis] Montering: Montering av hodet
- Trinn 7: Elektronikk: Lodding av PCB og bulk av elektronikken
- Trinn 8: Elektronikk: Adapter for batterikontakt
- Trinn 9: Kode: Kompiler og last opp kode
- Trinn 10: Montering: Monter elektronikkomponenter
- Trinn 11: Montering: Montering av servomotorer
- Trinn 12: Montering: Fest bena
- Trinn 13: Montering: Torso
- Trinn 14: Stem på meg
2025 Forfatter: John Day | [email protected]. Sist endret: 2025-01-23 15:02
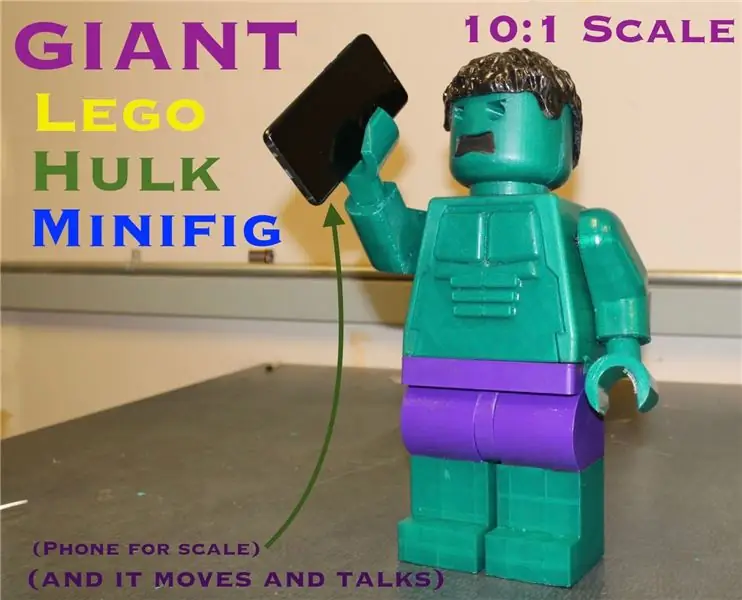


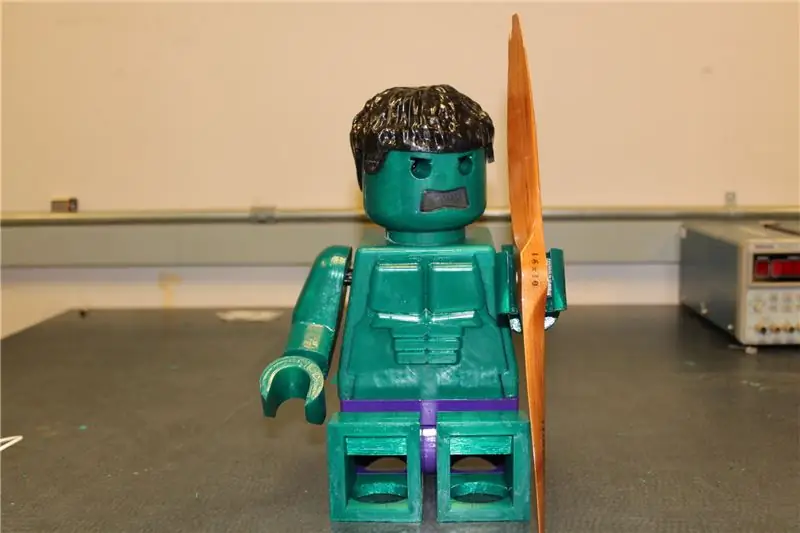
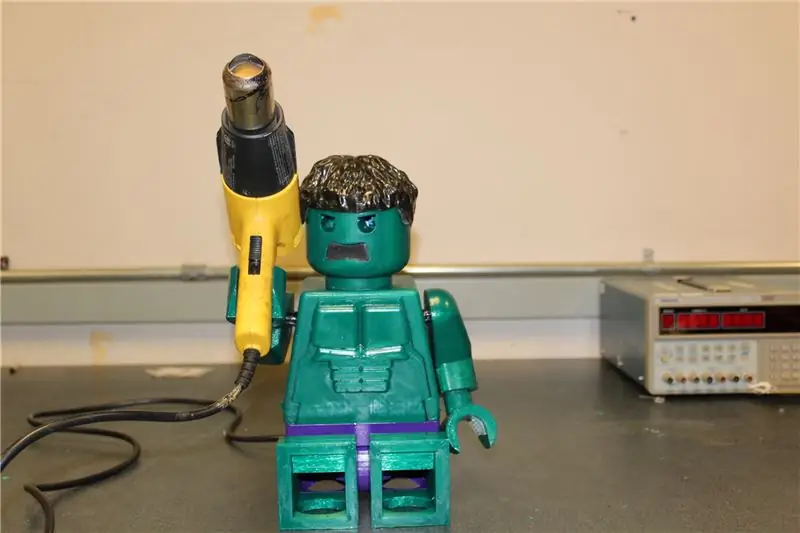
Fusion 360 -prosjekter »
Jeg har alltid lekt med lego som barn, men jeg hadde ikke noen av de 'fancy' legoene, bare klassiske legoklosser. Jeg er også en stor fan av Marvel Cinematic Universe (MCU), og min favorittperson er Hulk. Så hvorfor ikke kombinere de to, og lage en gigantisk hulk minifigur, fordi større er alltid bedre, ikke sant? Så jeg bestemte meg for å lage en 10: 1 -modell av de originale lego minifigurene.
En Giant Lego Hulk Minifig (jeg antar at den skulle hete megafig) er ikke nok, jeg bestemte meg for å ha det litt morsommere og få den til å leve. Jeg har også lagt til noen nye nye funksjoner som gjør at den både kan bevege seg og snakke ved å legge til 3 servomotorer, en MP3-spillermodul og en høyttaler med en innebygd forsterker.
Siden den har en MP3 -spillermodul og en høyttaler, kan du faktisk laste opp alle favorittlåtene dine på et SD -kort og bruke den som høyttaler også!
Elektronikken og maskinvaren til dette prosjektet er også lett hentet og relativt billig. På den måten er dette prosjektet enkelt reproduserbart av massene (og Instructables -samfunnet). Anslaget mitt for prosjektkostnaden er rundt $ 50-80-dette vil avhenge av hvor du kjøper varene. Hvis du er villig til å vente på eBay eller Aliexpress, blir det billigere, hvis ikke sendte DFRobot min via DHL, og jeg fikk den på 2 dager. Samme argument kan sies for kvaliteten på filamentet du brukte. Med tanke på at du kan hente en liten for $ 5 fra Amazon, vil jeg si at prisen stiger ganske lineært, eller mindre gitt at dette har mange flere funksjoner enn noen lego-figurer som er kjøpt i butikk.
Trinn 1: Materialregning
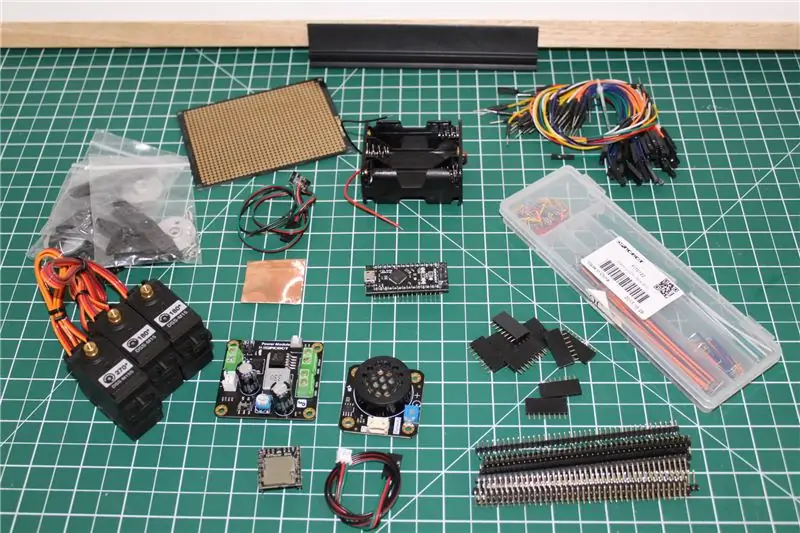
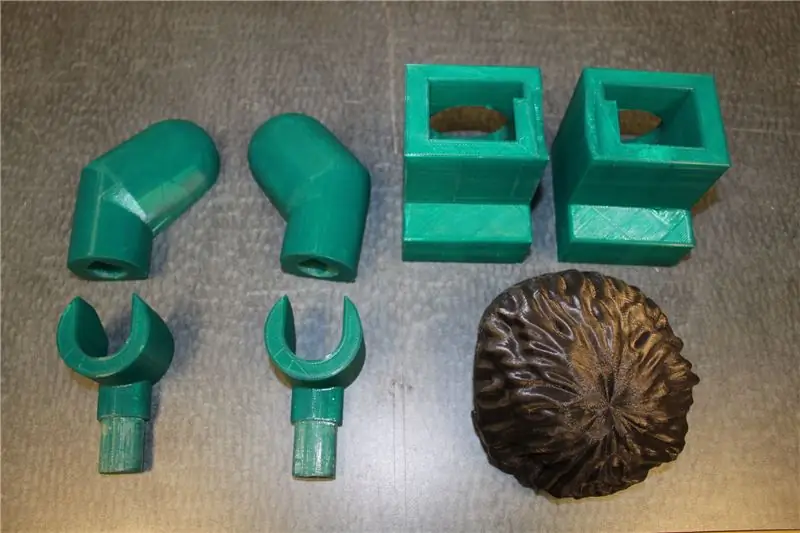
Maskinvare
Assorterte M3 muttere og bolter
1 kg grønn PLA (jeg har massevis av filament for en god handel på Kijiji, men du kan få din fra Amazon eller filaments.ca hvis du er i Nord -Amerika)
200g Purple PLA (jeg brukte merket CCtree fra Amazon, og det overgikk mine forventninger til prispunktet)
200 g svart PLA (jeg brukte mitt favoritt, men litt dyrt merke, Innofil)
Epoxy Resin and Hardening Agent (dette er for utjevning og glans av utskriften, du kan også bruke XTC3D, men jeg syntes de er veldig dyre)
CA Lim og Accelerant eller Superlim (førstnevnte er å foretrekke fordi du kan akselerere herdetiden til bare sekunder)
Foam Brush (jeg fikk min fra en lokal kunstbutikk, Currys, som ga meg studentrabatt!)
Pro Tips / morsomt faktum: CA Lim er faktisk bare superlim, der CA står for Cyanoacrylate (omtrent som når du kjøper Tylenol vs Acetaminophen på et apotek, sistnevnte er et generisk merke med det faktiske kjemiske navnet). Fordelen med å bruke CA Lim er at du kan kjøpe den med akselerant som reduserer herdetiden til et par sekunder, så du trenger ikke å klemme den eller holde den før den tørker.
Forsiktig: Vær forsiktig så du ikke får noen CA -lim + akselerantblanding på hendene, fordi det brenner seg.
Elektronikk
Arduino Pro Nano
MP3 -spiller modul
Høyttaler og forsterkermodul
180 og 270 graders servoer (jeg valgte å bruke 2180 grader for armen og 1 270 grader for hodet)
Voltage Step-Down Converter (Du kan også bruke en 7805, men de kan ikke levere så mye strøm som denne, pluss at dette også fungerer for en 3-cellers LiPo!)
1K Ohm motstand (jeg er sikker på at du sannsynligvis har noen liggende, eller du kan kjøpe en pakke som varer livet ut)
PCB protoboard
Jumper ledninger
Brødbrett ledninger
2 -cellers litiumpolymer (LiPo) batteri eller 6V AA batteriholder (jeg foretrekker LiPo siden den er oppladbar og kan gi 7,2V til servomotorene)
Pinnehoder (M / F)
XT60 -kontakt (hvis du velger å bruke et litiumpolymerbatteri med en xt60)
JST Crimp Pins (Eller du kan bare lodde de kvinnelige endene på hoppetråden - jeg eide allerede en crimper og hadde JST Crimp pins, så jeg brukte dette for å få det til å se mer profesjonelt ut)
Heat Shrink (Mye ryddigere og mer profesjonelt utseende enn elektrisk tape!)
Verktøy
3D -skriver
Loddejern, Lodde, Avlodingspumpe
Multimeter (for feilsøkingskretser)
Crimper (Hvis du velger å bruke et litiumpolymerbatteri med en XT60 -kontakt)
X -acto kniv - Jeg fikk min i en lokal kunstbutikk for rundt $ 2 med studentrabatt
Sandpapir - 400 korn, 600 korn, 1000 korn, 200 korn
"Men jeg har ikke en 3D -skriver"
Ikke noe problem! Du kan sende STL -ene til 3D -utskriftstjenester som Shapeways og 3DHubs
Jeg vet at listen ser skremmende og lang ut. Jeg prøvde å gjøre det så omfattende som mulig, samtidig som jeg ga begrunnelser og detaljer om hvordan jeg gikk til designvalgene mine. På den måten kan du velge og endre og endre prosjektet for å gjøre det til ditt eget. Målet mitt er å alltid gjøre det mulig for brukerne å være kreative og lage sine egne prosjekter mens de bruker mine som en guide i stedet for bare lasteskjæring, men dupliser gjerne det også!
3D -utskrift blir også mer vanlig, så kanskje du har en venn som har en 3D -skriver som du kan bruke. Filamenter blir billigere, og du kan få en spole på 1 kg for mindre enn $ 20CAD eller AUD (eller <$ 15 USD)!
Trinn 2: Del og erobre
Denne bygningen virker kanskje ikke kompleks, men den omfatter de grunnleggende blokkene for robotikk - elektromekanisk, kretsløp og innebygd programmering. Som sådan ville noen forhåndsplanlegging i stor grad hjelpe til med byggingen.
Jeg har delt denne bygningen inn i 5 segmenter:
- Design og 3D -utskriftsfase
- Etterbehandling
- Elektronikk
- Kode
- montering
Splitt og hersk! Mens du venter på at utskriftene skal være ferdige, kan du komme i gang med elektronikk og koding.
Trinn 3: [Valgfritt] Design og 3D -utskrift: Design
![[Valgfritt] Design og 3D -utskrift: Design [Valgfritt] Design og 3D -utskrift: Design](https://i.howwhatproduce.com/images/011/image-30025-8-j.webp)
Siden mine Fusion360 -ferdigheter er begrensede, fikk jeg en venn til å hjelpe meg med å CAD disse filene. Du trenger ikke å designe din egen hvis du følger denne veiledningen nøyaktig. Bare gå til neste trinn, og skriv dem ut i 3D. Alle dimensjoner er metriske!
Men hvis du velger en annen PCB eller høyttaler, må du kanskje endre størrelsen på hullene og kutte ekstruderinger der komponentene skal være.
Men hvis du vil ha andre lego minifigurer som ikke er hulken, kan du gjerne CAD din egen. Noen, vennligst lag en gigantisk lego batman -versjon av dette!
Pro Tips: Design med 3D -utskrift i tankene
(1) Riveformede sirkler kan skrives ut uten støtter, så ta med rivende former for sirkulære utskjæringer i stedet for sirkler
(2) 45 graders vinkler eller brattere kan skrives ut uten støtter, så gjør at overhengene dine har 45 graders vinkler for å støtte dem.
Trinn 4: Design og 3D -utskrift: 3D -utskrift
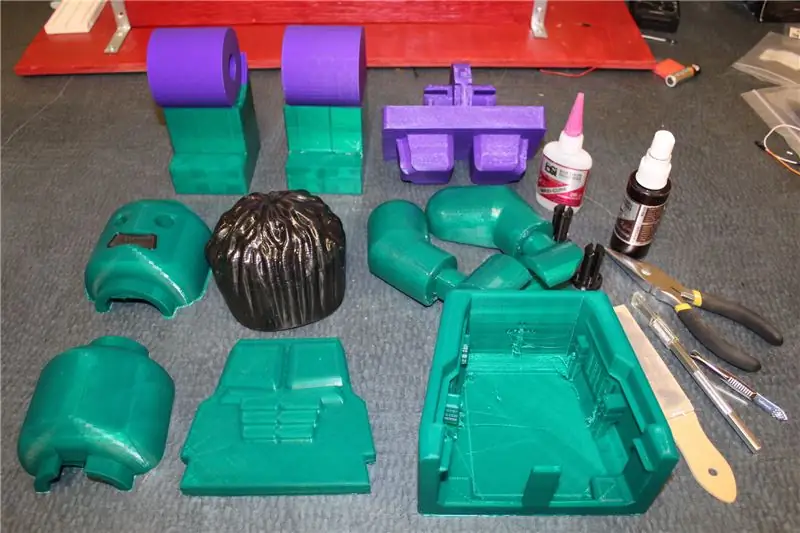
Dette trinnet er ganske rett frem, ta tak i SD -kortet ditt, lagre g -koden fra skjæreren din for hvilken STL -fil du vil skrive ut og skrive den ut eller bare bestill det fra Shapeways eller 3DHubs.
Den totale utskriftstiden for alle utskriftene var rundt 80 timer. Den brukte totalt litt over 1 kg materiale ved bruk av svarte, lilla og grønne filamenter - for det meste grønt fordi hulk er grønn, duh. Du kan alltid skrive den ut i enfarget og deretter spraymale de enkelte bitene, noe som er en annen metode for å jevne den ut (se neste trinn).
Pro Tips 1: Bekjemp den gjennomsiktige filamenten
Hvis du har en gjennomsiktig filament som jeg fikk for greenen min, kan du slippe unna med at den fremdeles ser ugjennomsiktig ut ved å (1) øke skalltykkelsen eller (2) bruke et dynamisk utfyllingssett for å fylle opptil 50% i trinn på 5%. Dessverre, siden harpiks er gjennomsiktig, dekker det ikke til gjennomsiktigheten av filamentet.
Pro Tips 2: Håndtere ikke-plastisk deformasjon
For deler som trenger å bøye seg litt, skriv den ut med en høyere utfylling enn standardinnstillingen, rundt 50%, så den er ikke for sprø når du må klemme pinnene sammen. Du kan forlate standard veggtykkelse. Det tok meg rundt 5 forsøk før jeg fikk den riktige kombinasjonen av utfylling og veggtykkelse. Bruk også filament av høy kvalitet. CCTree-filamentet fra Amazon er utmerket siden det gir mulighet for en ikke-plastisk deformasjon på pinnene.
Tips 3: Redusere utskriftstiden
Det er ingen gratis lunsj hvis du vil spare tid på 3d -utskrift. Det er nesten alltid en avveining du må gjøre. Her er noen jeg brukte som ikke påvirket utskriftskvaliteten særlig:
(1) Bruk en høyere laghøyde - rundt 0,2 mm er akseptabelt for hodet og fronten av kroppen og 0,3 mm for alt annet.
(2) Senk utfyllingstettheten til rundt 5-10% eller bruk dynamisk fylling som angitt i ProTip 1.
(3) Slå på kamemodus for å redusere reisetiden.
(4) Bruk brims eller flåter-Det kan være kontraintuitivt å bruke brims og rafts, men det vil spare deg for tid fra mislykkede utskrifter som kom av utskriftssengen fra dysen og slo noen lett av z-aksen utskrifter gjentatte ganger.
(5) Bruk færre støtter. For utskrifter som krever et stort antall støtter som håret, bruker du støtter med lavere tetthet rundt 5-10% vil fortsatt gi en vellykket utskrift.
Trinn 5: [Valgfritt] Utjevning av 3D -utskrifter
![[Valgfritt] Utjevning av 3D -utskrifter [Valgfritt] Utjevning av 3D -utskrifter](https://i.howwhatproduce.com/images/011/image-30025-10-j.webp)
![[Valgfritt] Utjevning av 3D -utskrifter [Valgfritt] Utjevning av 3D -utskrifter](https://i.howwhatproduce.com/images/011/image-30025-11-j.webp)
![[Valgfritt] Utjevning av 3D -utskrifter [Valgfritt] Utjevning av 3D -utskrifter](https://i.howwhatproduce.com/images/011/image-30025-12-j.webp)
Dette er en lang og belastende prosess, men likevel veldig givende. Du trenger ikke gjøre det, men det får sluttresultatet til å se så mye bedre ut. Etter BrittLivs guide valgte jeg å glatte utskriften min med epoksybelegg, bortsett fra at jeg bestemte meg for å slipe den ned til 1000 korn først (helst 2000, men jeg hadde ingen).
Bland epoxy med en 30 minutter til 1 times arbeidstid slik at du kan få alle bitene ferdig før den stivner. Deretter vil det ta ytterligere 24 - 48 timer å herde, avhengig av hvor tykt lag du brukte.
Forsiktig: Bruk hansker ved epoksing. Du kan bli allergisk mot epoxy, noe som vil føre til kontaktdermatitt, slik at du ikke vil ha noe på hendene. I tillegg trenger du ikke å møysommelig slipe fingeravtrykkene dine på utskriftsjobben som bare tok 12 timer å skrive ut.
Dette trinnet er ganske langt og omfattende, selv om handlingene som er tatt for å jevne utskriften er ganske enkle. Det var mange teknikker som ble brukt og prøvd gjennom hele prosessen, og jeg ønsket å dele alt jeg har lært.
Pro Tips 1: Utjevning av strøk Bruk en papirplate eller en flat overflate som en "palett" før du maler, i motsetning til å dyppe skumbørsten på en kopp full av epoxy. Dette lar deg kontrollere og påføre jevnt belegg på utskriftsjobben.
Profftips 2: Bruk en skumbørste Jeg har ingen forkunnskaper innen kunsten eller noe relatert til det, så når det gjaldt å plukke en pensel fra en lokal kunstbutikk, hadde jeg ingen anelse om hva jeg skulle velge, så jeg ba om hjelp. Et veldig godt poeng ble brakt opp til meg, hvis du bruker en typisk pensel, vil slagene fra børstene være synlige, så bruk en skumbørste siden det ikke er børster.
Tips 3: Forhindre klebrighet ved å blande riktig forhold og måle nøyaktig
Bruk en skala for å måle det riktige forholdet mellom harpiks og herder. I motsetning til online råd om å blande mer herder for å tørke raskere, bruk alltid riktig forhold. Det er enkel vitenskap, eller kjemi snarere. Harpiks og herder som blandes sammen er en kjemisk reaksjon - faktisk kan du se at det er en eksoterm reaksjon fordi epoksyet varmes opp når du blander dem. Forholdet som foreslås er de støkiometriske forholdene som gjør at all harpiks og herder kan reagere sammen for å danne epoksyen, og dermed vil alt som er i overkant ikke reagere, og du vil sitte igjen med et lag klebrighet.
Leksjoner lært
1) Ikke suge i vann når det er gjort
Jeg hadde ikke en god overflate å legge de 3d -trykte delene på, så jeg la den bare oppå papirskrap. Som forventet dryppet epoksyen ned og ble limt med papiret. Det er faktisk ikke vanskelig å fjerne fordi du bare kan suge papiret i vann og gni det av - det vil si hvis du ikke la epoxy på området ved å komme i kontakt med papiret (du burde ikke). Dessverre ble det slik at den epoksyte utskriften ble dyppet i vann, og den så flekkete ut - som en bil du prøvde å vaske, men ikke tørket ordentlig.
Det var ingenting jeg kan gjøre for å bli kvitt flekken selv om jeg tørket den ordentlig. Den eneste løsningen var å slipe det hele igjen - og sliping av epoxy er ikke morsomt i det hele tatt - til det er glatt (sand opp til 2000 korn), og deretter belegge det igjen i epoxy som betyr mer ventetid.
Det er en sølvfôr, men etter at jeg gjentok den kjedelige prosessen med utjevning og epoksing så sluttresultatet betydelig bedre ut! Jeg kan tenke meg at det er et poeng med redusert avkastning til dette, og på et tidspunkt er det ikke noe poeng å gjenta dette, der første strøk har størst effekt.
2) Ikke varm pistolen
IKKE bruk en varmepistol for å gjøre epoksyherden raskere. Plasten blir myk og deformeres selv om du varmer den på avstand. Jeg hadde et eksempel på PLA, og jeg lærte at det er bedre å bare ha tålmodighet og vente.
3) Fortsett å slipe
Jeg var motvillig til å slipe det først fordi det fikk det til å se hvitt og riper opp, og jeg var bekymret for at når jeg dekker det med et lag epoxy, vil det beholde den kjedelige riper. Jeg tok feil. Faktisk ga det beste resultatet å slipe det til det er glatt og veldig riper opp.
Hvordan virker det?
Når du pusser det, blir du kvitt eventuelle ufullkommenheter og ujevnheter, slik at du får en myk utskrift, men det fyller ikke noen av hullene og sprekker. Når du bruker epoxy på en utskrift, fyller du effektivt alle hullene som er igjen av lagene og eventuelle ujevnheter i utskriften. Legg merke til at hvis du dypper den 3d -trykte delen i vann, ser den mykere ut mens den er våt - det er fordi vannet fyllte hullene, men det fordamper. Harpiksen fyller den inn permanent og etterlater ingen misfarging siden den er fargeløs.
Trinn 6: [Delvis] Montering: Montering av hodet
![[Delvis] Montering: Montering av hodet [Delvis] Montering: Montering av hodet](https://i.howwhatproduce.com/images/011/image-30025-13-j.webp)
![[Delvis] Montering: Montering av hodet [Delvis] Montering: Montering av hodet](https://i.howwhatproduce.com/images/011/image-30025-14-j.webp)
![[Delvis] Montering: Montering av hodet [Delvis] Montering: Montering av hodet](https://i.howwhatproduce.com/images/011/image-30025-15-j.webp)
Det er noen elektroniske komponenter du ikke trenger å lodde takket være den modulære PCB -designen jeg ga. Dette er servomotorer og høyttalermodulen. Siden servomotoren og høyttalermodulen er uavhengig av kroppen, kan vi plassere dem i hodet og fullføre hodemonteringen.
Plasser høyttaleren foran på hodet. Det er pinner for høyttaleren å skru i, men siden disse to stykkene skal klemmes sammen av servoen og håret, er det ikke nødvendig å skru den inn - og den kommer ikke fra hverandre med mindre du tvinger den til.
Trinn 7: Elektronikk: Lodding av PCB og bulk av elektronikken
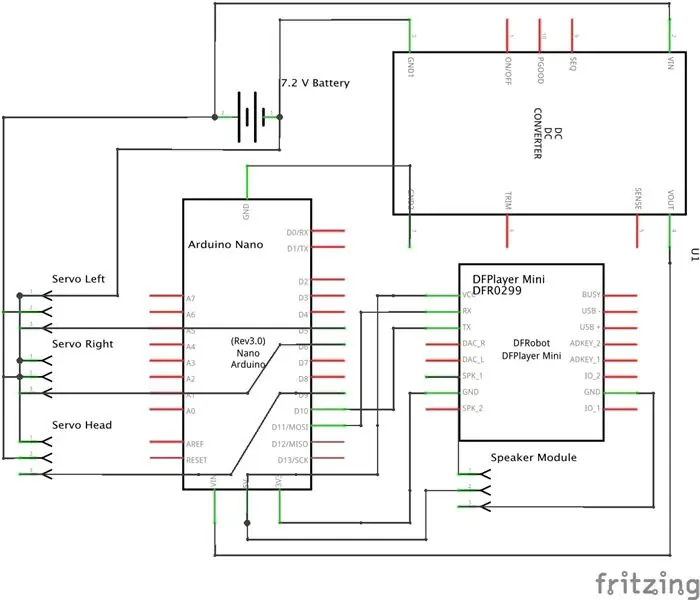
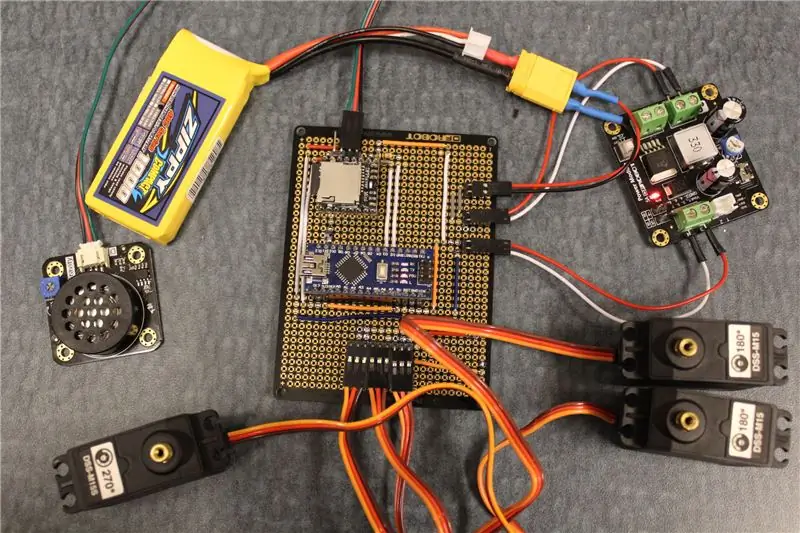
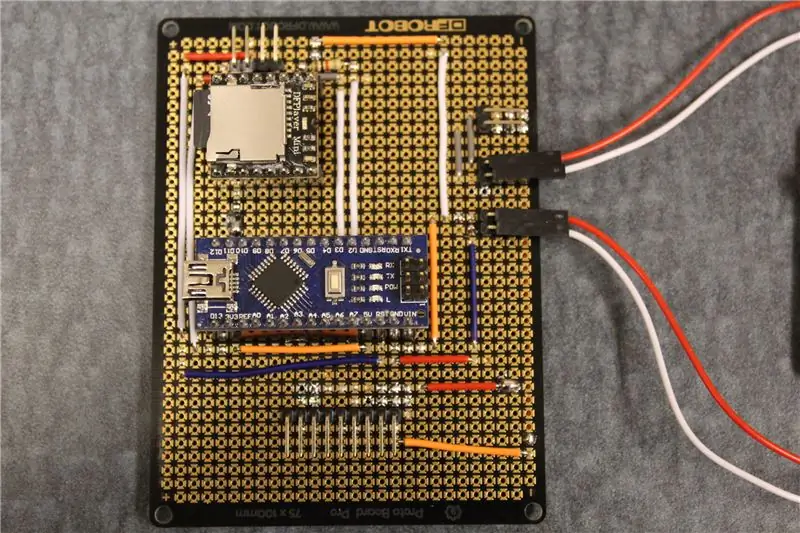
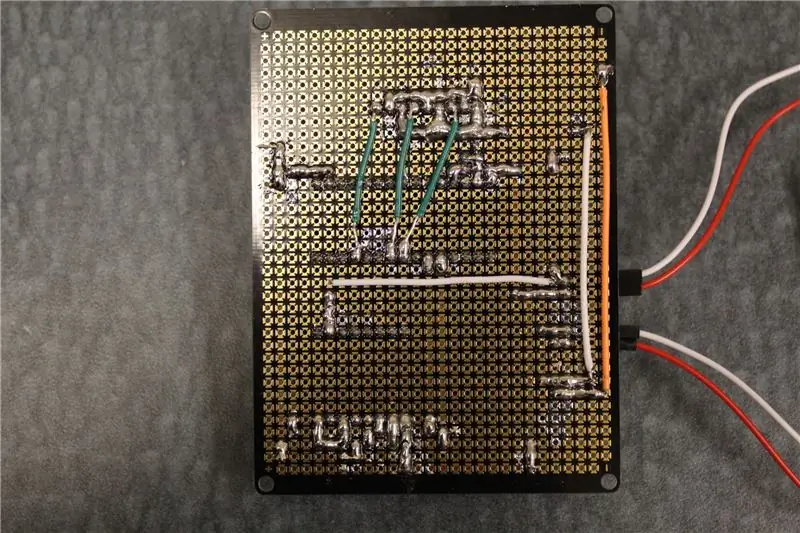
Lodd PCB -en basert på skjemaet som følger med. Jeg har også lagt til Fritzing-dokumentet, slik at du kan åpne det på Fritzing og kjøre automatisk ruting for PCB og få det skrevet ut hvis du ikke vil lodde bussbanene selv.
For å gjøre kretsen penere og modulær brukte jeg noen få teknikker som er nevnt nedenfor:
- Bruk kvinnelige pinhoder som tilpassede IC -kontakter for Arduino Nano og DFPlayer Mini.
- Bruk mannlige pinhoder for å koble til servomotorer og høyttalere. På denne måten loddes de ikke direkte på PCB og kan fjernes når som helst.
- Legg til mannlige pinhoder for inngang og utgang for batteriinngang og trinn-ned-omformer. På denne måten kan du enkelt rute og legge til flere bussbaner til riktig spenning. Dette er ikke nødvendig, men det gjør ledningene enklere og gir mulighet for færre ledninger som henger på nedtrekksspenningsomformeren. Som du kan se brukte jeg bare 2 par.
Dette krever en moderat mengde loddeerfaring og ferdigheter på grunn av antall broforbindelser du må gjøre og hvor nær tappene er til hverandre.
Så hvordan får du et godt resultat på lodding av kretskortet?
Få et godt loddejern med temperaturkontroll og et PCB med firkantede pads. Bruk et meiselspiss (flatt) jern for å øke kontakten mellom komponenten og puten. Jeg liker også å bruke 2/3 tinn og 1/3 bly siden bly har en lavere smeltetemperatur som gjør lodding litt lettere.
Trinn 8: Elektronikk: Adapter for batterikontakt
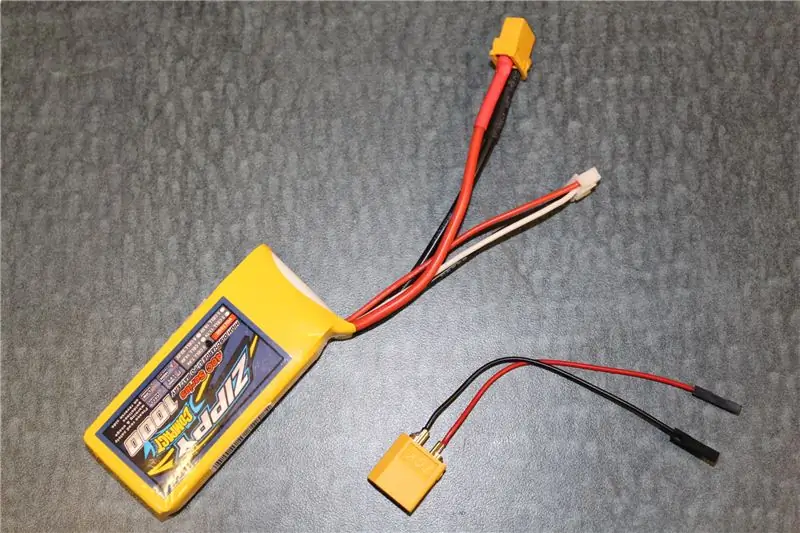
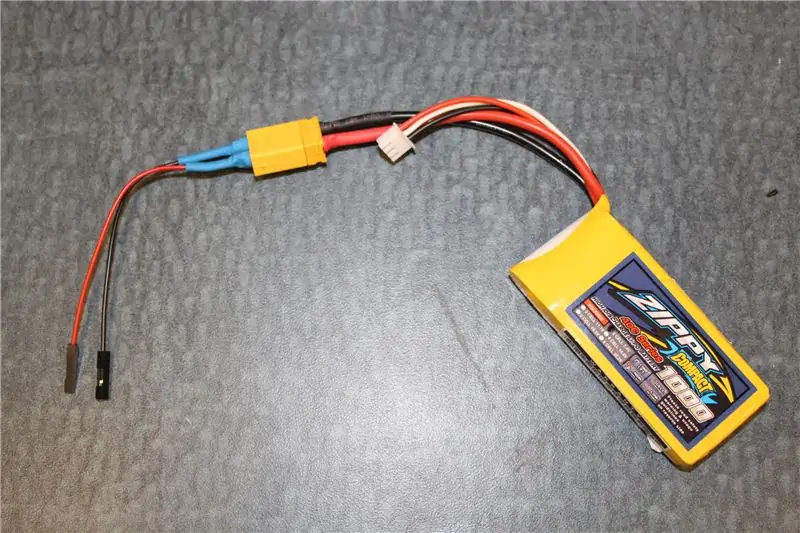
Utgangen til det 2 -cellers LiPo -batteriet er skjønt XT60 -kontakt, som er en standard i RC -fly. Jeg ville ikke kutte den fordi XT60 er standarden for mange plugger for børsteløse motorer som jeg bruker og kan også håndtere opptil 60A strøm - som jeg trenger for andre applikasjoner.
1. Loddetinn XT60
Så i stedet valgte jeg en mer modulær løsning. Lodd en XT60 -adapter med en XT60 -mann til JST -hunn (merket ovenfor) - negativ til negativ (svart ledning) og positiv til positiv (rød ledning).
2. Crimping/lodding JST Female Pins til XT60
Plasser de uklemte pinnene på krymperen og stram den slik at den holder pinnene godt fast mens du fortsatt lar ledningene gli gjennom - den danner en åpen terning. Sett den avisolerte ledningen inn på den åpne terningen, og krymp den deretter. Gjenta dette for både de røde og svarte ledningene, og skyv deretter de to krympede pinnene inn i JST -huset.
Alternativt kan du bare kutte av hanenden av M/F -jumperkabelen og lodde ledningen på XT60 som jeg gjorde.
3. Varm krymp kontaktene
Sørg for å varme krympe kontaktene slik at de ikke ved et uhell kortsluttes. Disse litiumbaserte batteriene vil lage noen vakre, om enn ikke så fine fyrverkerier hvis de er korte
Pro Tips 1: Lodding XT60s
Når du lodder de tynne ledningene til XT60, tenner du først ledningene og fyller hulrommene på XT60 med loddetinn halvveis. Behold strykejernet på kontaktene, dypp de fortinnede ledningene inn og fjern strykejernet mens du fortsatt holder ledningen. La den stå stille i noen sekunder og varmekrym den når den er avkjølt.
Pro -tips 2: Forebygge koblingsdeformasjon
For å forhindre at XT60 -kontakten deformeres av høy varme, fest hunnen og hannen (usolgte kontakter IKKE batteriene!) Til hverandre før lodding. På den måten vil de beholde kontaktformen og forhindre at lederne beveger seg siden den sitter tett.
Trinn 9: Kode: Kompiler og last opp kode
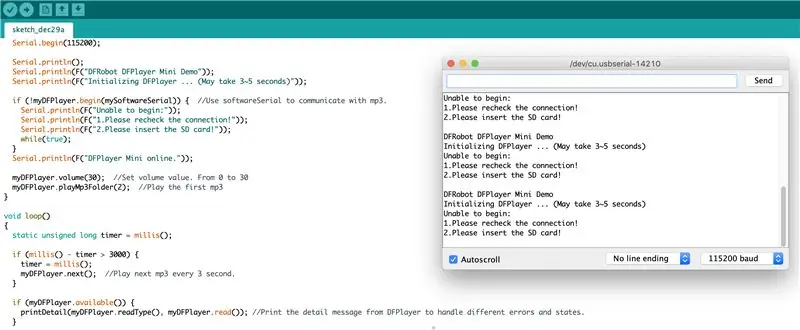
Last ned koden vedlagt og last den opp til Arduino Nano. Dette er ansvarlig for å kjøre 4 forskjellige bevegelsesmoduser fra servoen, samt å slå lydeffekter gjennom MP3 -modulen. MP3 -modulen spiller lydene basert på hvilken rekkefølge MP3 -filene lastes opp til SD -kortet.
Hvis du vil bruke den som høyttaler, bruker du bare følgende funksjon for å spille av tilfeldige musikkfiler i en loop.
myDFPlayer.randomAll ();
For mer informasjon om alle kommandoene som kan gis til MP3 -spilleren, kan du finne den fra produsentens spesifikasjon.
I mitt tilfelle er alt som trengs å spille av en bestemt MP3 -fil. Måten jeg sørget for at MP3-modulen skulle spille av riktig fil i stedet for å stole på ordren, bruker den innebygde metoden, forutsatt at den er i mappen som heter MP3 (ikke store og små bokstaver):
myDFPlayer.playMP3Folder (1);
hvor argumentet 1 er filnavnet, 0001.mp3.
Ved å bruke metoden som er avhengig av filopplastingsrekkefølgen:
myDFPlayer.play (1);
antar at den er i rotmappen og ikke krever et bestemt filnavn.
Trinn 10: Montering: Monter elektronikkomponenter
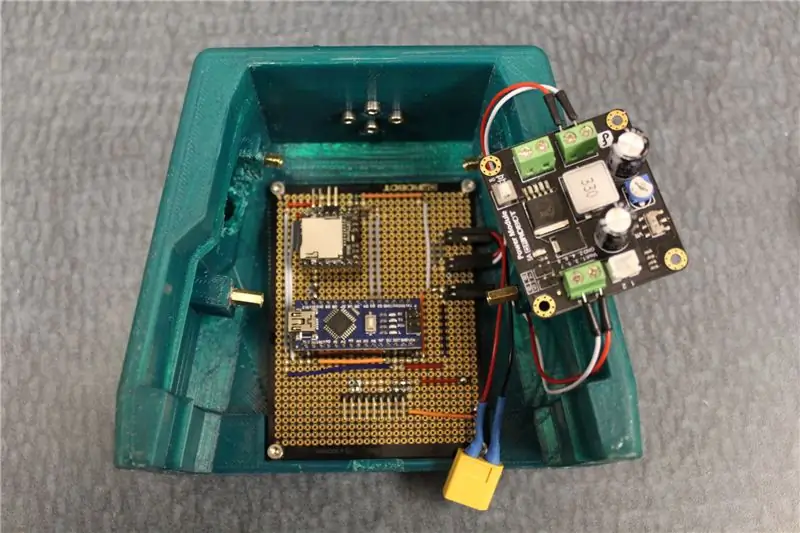
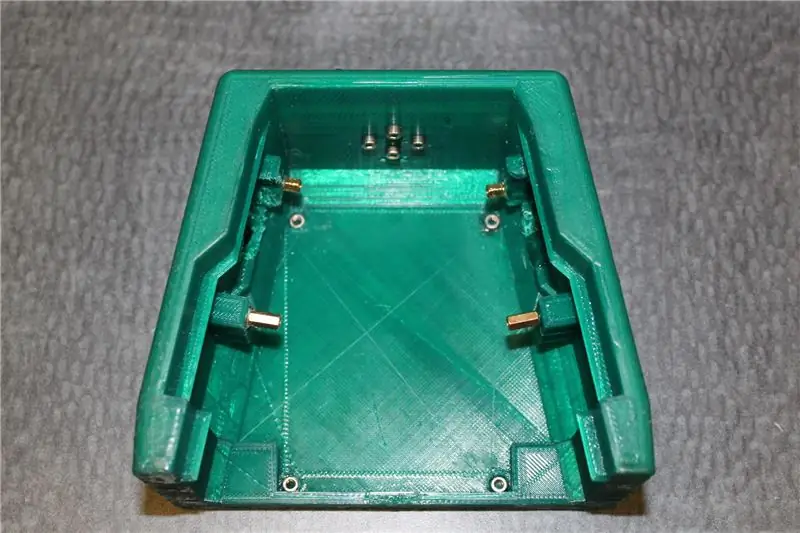
Vi skal begynne med kretskortet og de elektroniske komponentene, og deretter fortsette å feste servomotorene.
For det første, for å gjøre monteringen enklere, G og koble fra komponentene.
Legg merke til hvordan det er noen sekskantede kuttekstruder for å fikse en mutter på legemet og hodet på Lego -brikken. Det er her mutteren skal limes med CA -lim - vær forsiktig når du limer den slik at du ikke tilfeldigvis legger til lim på trådene.
Sett deretter kretskortet inn og juster hullene til mutrene og skru det inn med M3 -bolter. Dette bør være en ganske rask og triviell oppgave.
Trinn 11: Montering: Montering av servomotorer
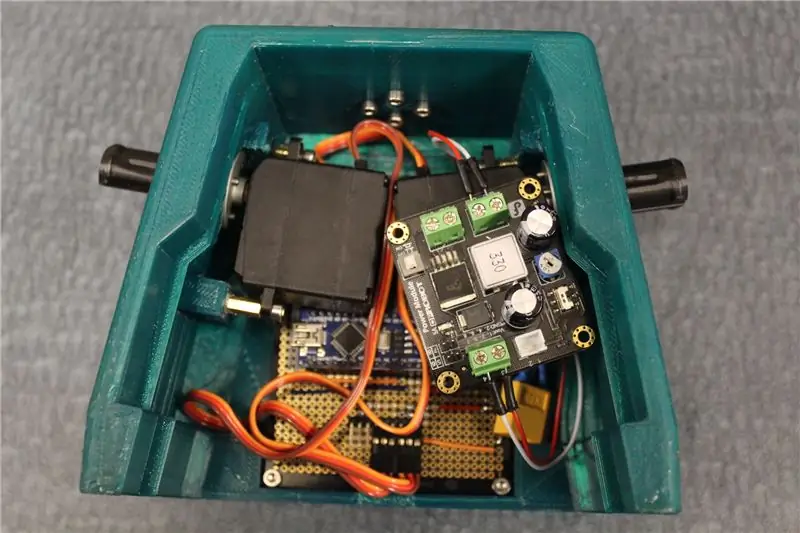
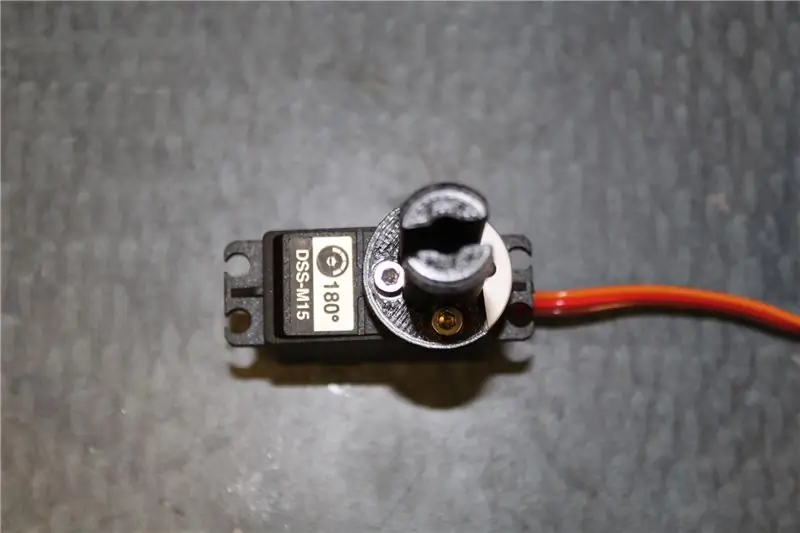
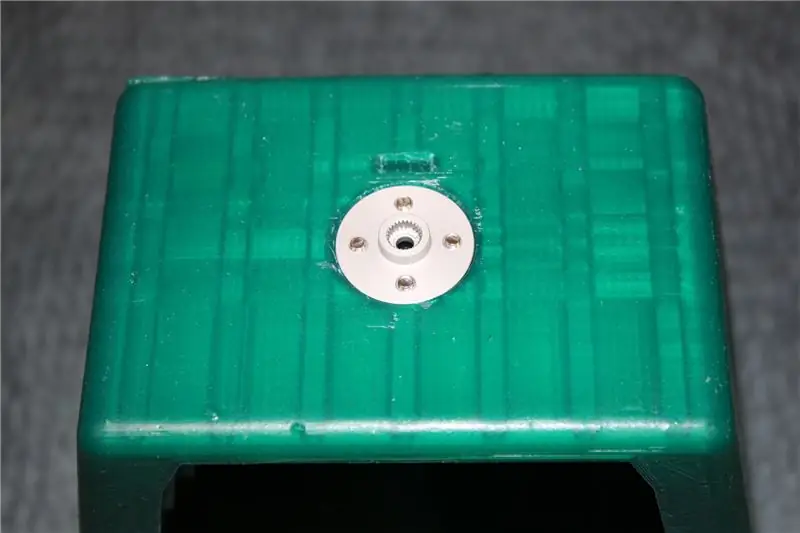
Det er to ting som må festes til servomotorene fysisk (1) Det sirkulære metallservohornet (merket ovenfor) og (2) Servokroppen til legostykket. Skruene som brukes til hele dette prosjektet er standardisert; de er alle M3 muttere og bolter.
Det har 3 servohorn som må festes i kroppen. En for hodet og to for armpinnene som skal drives av servomotoren. Det er en bestemt rekkefølge de skal settes sammen slik at du ikke trenger å plassere hendene på en vanskelig måte.
- Skru inn servohornet for hodet øverst på kroppen ved hjelp av 4 m3 skruer mot hornet.
- Skru armpinnene på servohornet og deretter på 180 graders servomotor med skruene som følger med servoen. Skru det inn mot hornet siden hullene på hornet er gjenget.
- Plasser distanser på sidene av kroppen der servoen skal monteres. Avstandene skal løse gapet mellom servoen og monteringsplattformen på grunn av designfeil. Dette vil bli løst, og du trenger ikke å gjøre dette trinnet.
- Deretter skruer du bare inn servomotorenes chassis og servohornet til karosseriet som vist på bildene. Hvis du ikke bruker distanser trenger du selvskruende skruer som følger med servomotoren. Servoene i kroppen sitter ganske tett, så du må fikle med den til du kan få begge inn.
Trinn 12: Montering: Fest bena
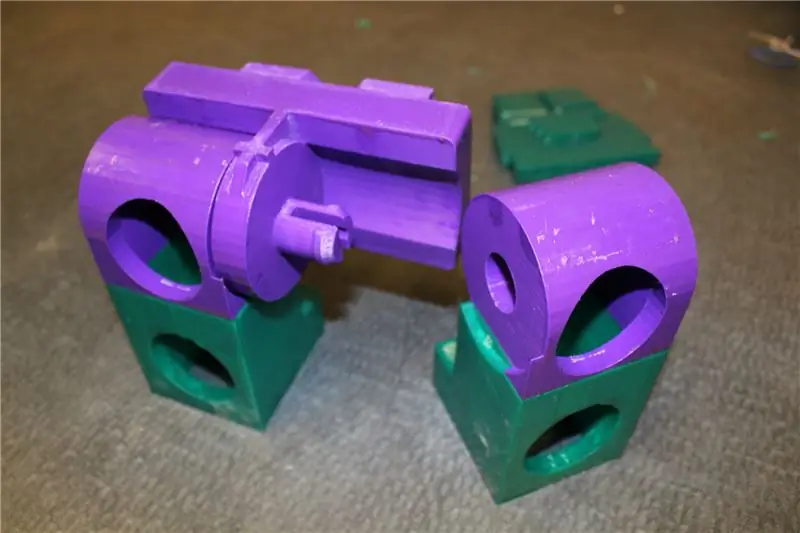
Det siste vi må gjøre er å sette sammen alle brikkene, akkurat som klassisk Lego.
- Lim de to halvdelene av bena, under (grønn PLA) og over kneet (lilla PLA) sammen med CA -lim
- Fest bena sammen til hoftene. Hvis det er litt sta, klemmer du bare de to pinnene litt sammen og skyver bena på hoften.
Dette er grunnen til at du bruker kvalitetsfilament (jeg brukte CCTree fra Amazon for de lilla bitene, og det er overraskende ikke sprøtt og fargerikt for prispunktet).
Trinn 13: Montering: Torso
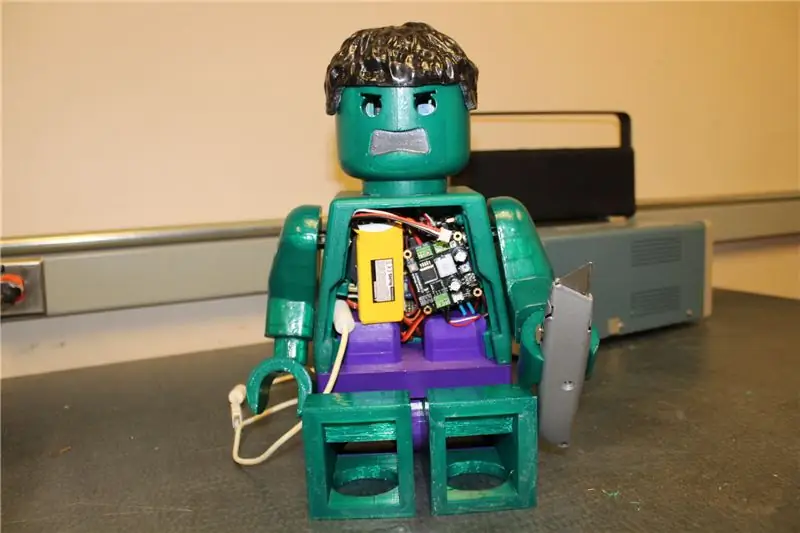
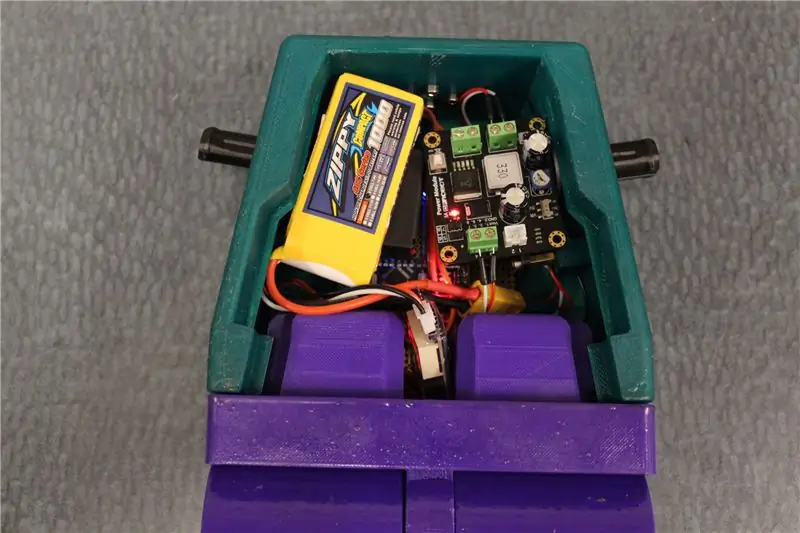
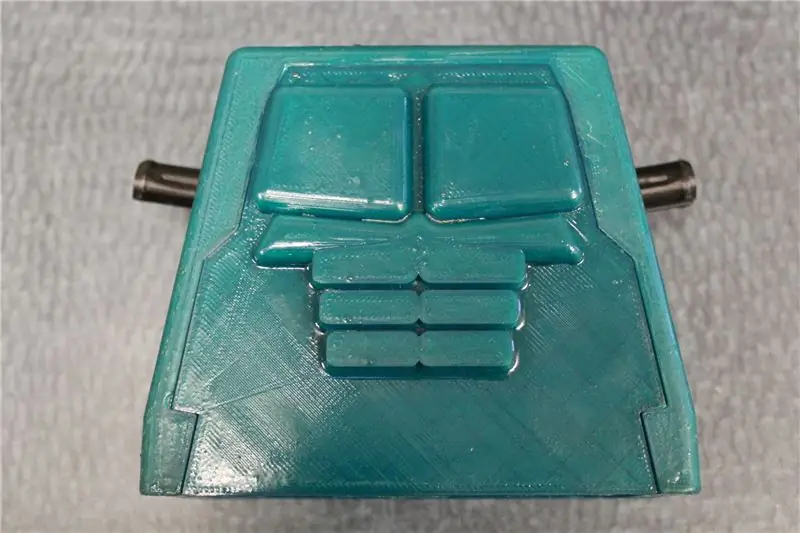
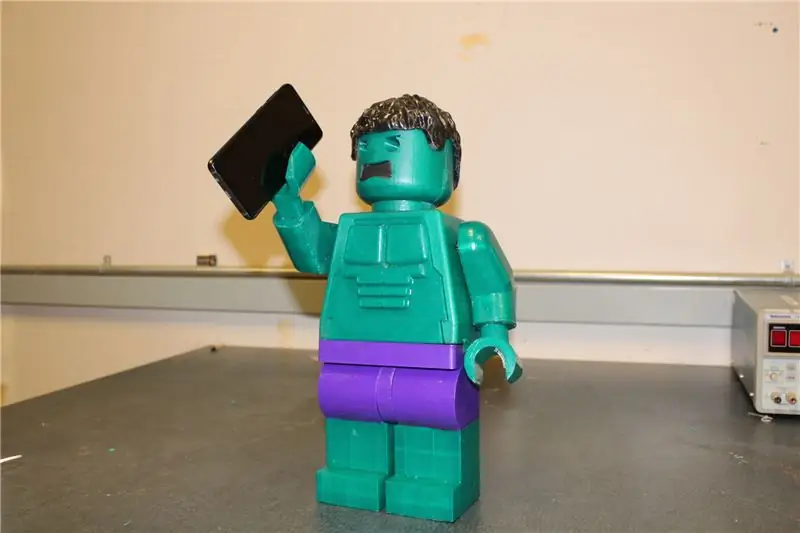
- Skyv hendene mot armene - armene kan trenge litt sliping avhengig av toleransene til 3d -print.
- Snap passe armene sammen til armpinnene akkurat som bena til
- Trykk ned høyttaleren og servoledningene gjennom hullet på kroppen og sett den inn i de riktige stifthodene du loddet.
- Skru hodeservoen på kroppens servohorn for å fullføre monteringen. Legg deretter brystplaten på toppen av kroppen.
Du er ferdig! Slå på den og nyt din Lego Hulk Mega Figur!
Trinn 14: Stem på meg
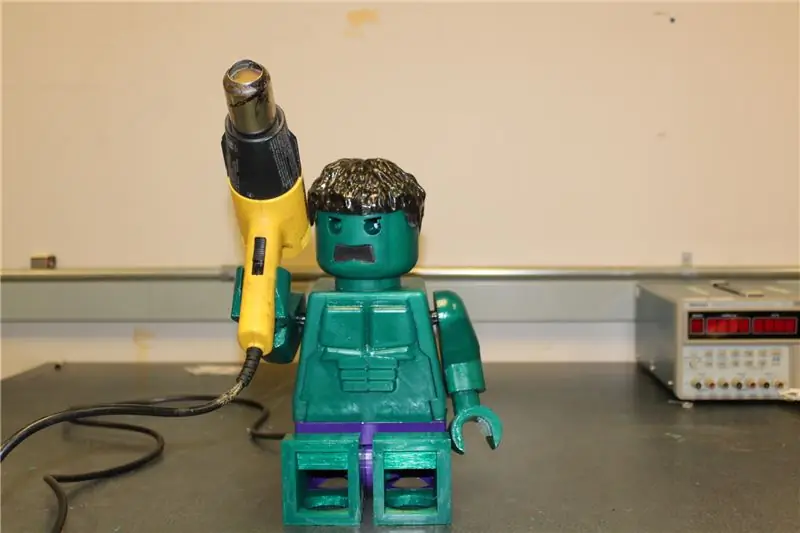
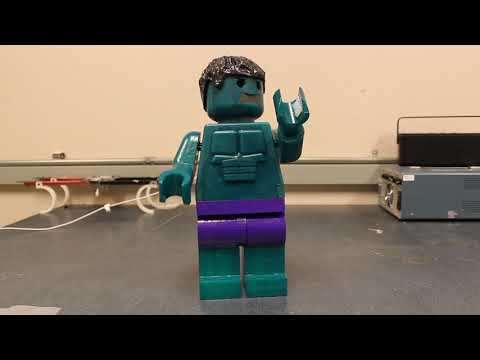
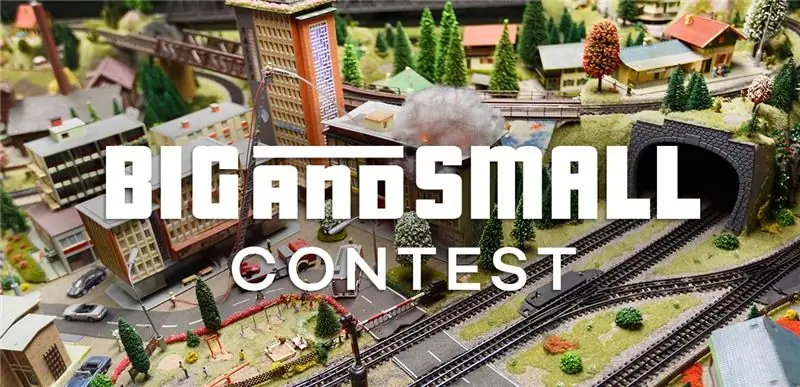
Jeg deltok i denne store og små konkurransen, så stemmene dine vil bli verdsatt hvis du likte dette.
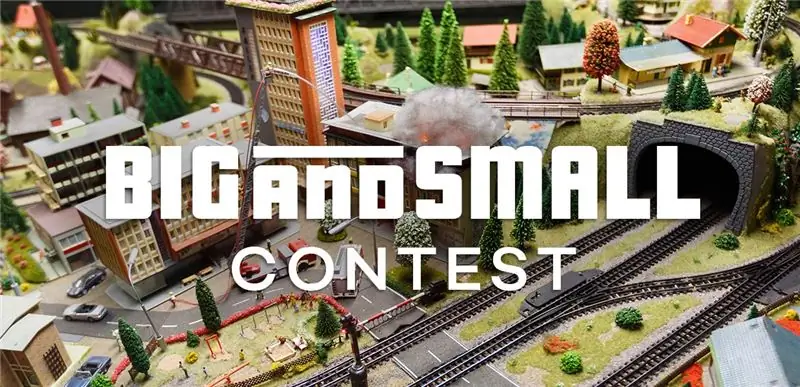
Andre pris i den store og små konkurransen
Anbefalt:
Arduino skala med 5 kg lastcelle og HX711 forsterker: 4 trinn (med bilder)
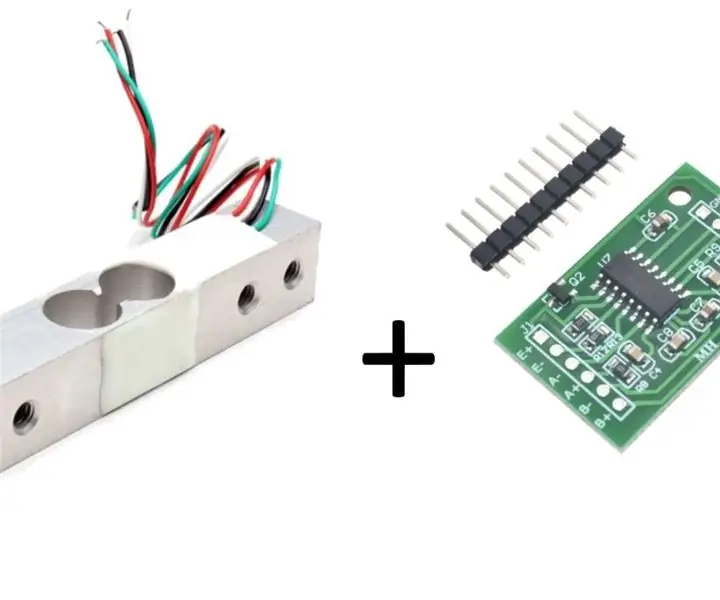
Arduino -vekt med 5 kg lastcelle og HX711 -forsterker: Denne instruksjonen beskriver hvordan du lager en liten veiervekt ved hjelp av lett tilgjengelige deler fra hyllen. Nødvendige materialer: 1. Arduino - denne designen bruker en standard Arduino Uno, andre Arduino -versjoner eller kloner skal fungere også2. HX711 på breakout
Real Life Moving Portraits From Harry Potter !: 11 trinn (med bilder)
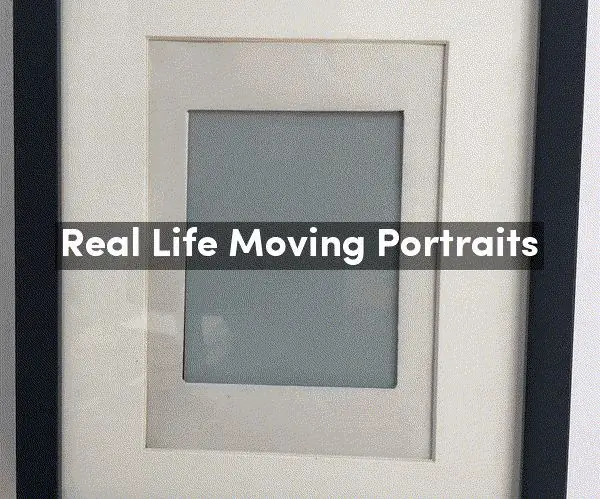
Real Life Moving Portraits From Harry Potter !: " Fantastisk! Fantastisk! Dette er akkurat som magi! &Quot; - Gilderoy Lockhart Jeg er en stor Harry Potter -fan, og en av tingene jeg alltid har elsket fra trollmannsverdenen er de bevegelige portrettene. Jeg snublet over Kyle Stewart-Frantzs animerte bilde
DIY Harry Potter Moving Portrait Project: 9 trinn (med bilder)
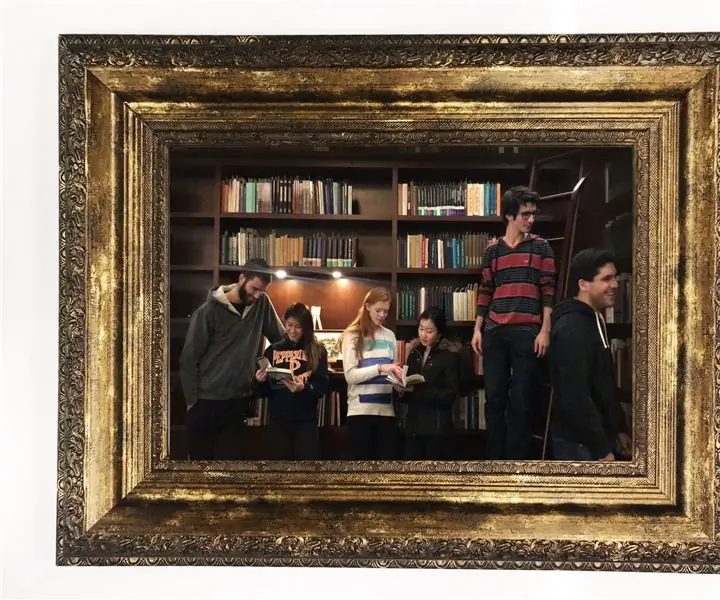
DIY Harry Potter Moving Portrait Project: Følgende er en instruks som er beregnet for renblodige trollmenn. Hvis du ikke er et rent blod, spesielt Slytherin, har du blitt advart om den uunngåelige fiaskoen og nederlaget du vil støte på som en squib, muggle, Hufflepuff eller mudderblod
Animatronic Mask With Moving Eyes: 13 trinn (med bilder)
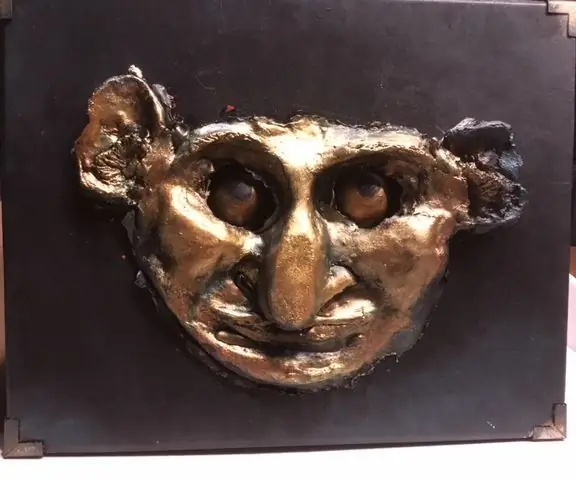
Animatronic Mask With Moving Eyes: Hei! For en skoleoppgave måtte vi oppdage Arduino. Så jeg bestemte meg for å lage en animatronisk maske. Det er mer som en veggdekorasjon. Hele funksjonen med det er å gjøre folk litt urolige, siden øynene vil bevege seg. Den er inspirert av
Utrolig HULK Nintendo Wii W/ Extra Usb: 6 trinn (med bilder)
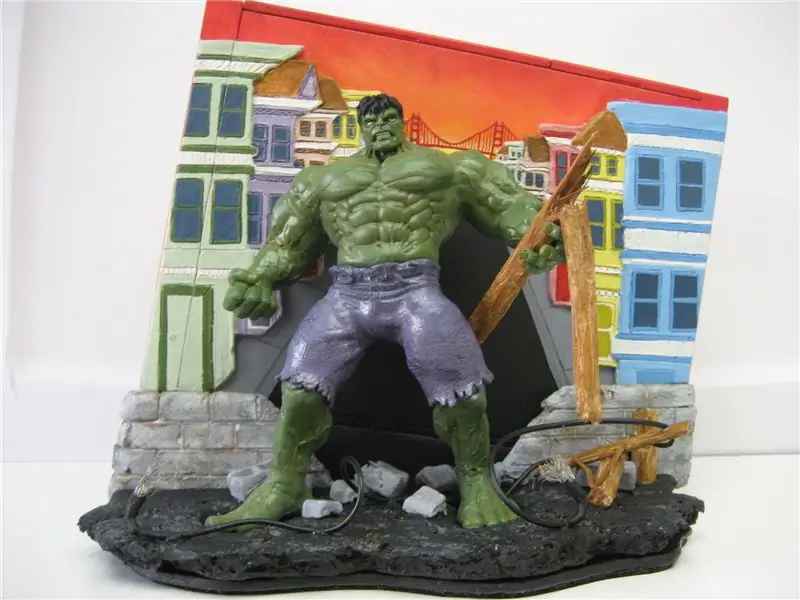
Utrolig HULK Nintendo Wii W/ Extra Usb: Vel, jeg ENDELIG fullførte min andre Wii Mod !!! The Incredible HULK tilpasset Wii. Jeg tok råd fra gutta dine og gjennom dette på e-bay allerede! Forhåpentligvis vil det gjøre meg litt deig! Denne instruksen vil være veldig lik min Super Mario Wii bortsett fra den