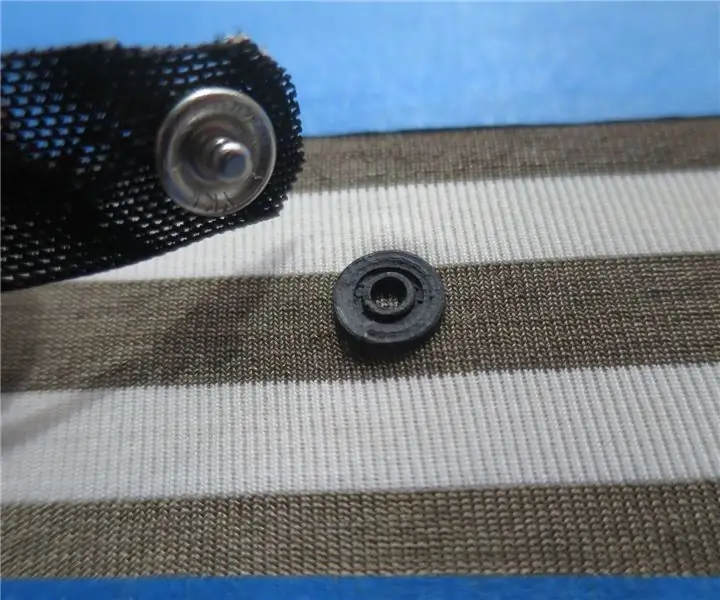
Innholdsfortegnelse:
- Trinn 1: Fusion360 -filer
- Trinn 2: Skriv ut test og oppsett
- Trinn 3: 3D -utskrift på et ledende stoffspor
- Trinn 4: Test konduktivitet
- Trinn 5: Skrive ut på forskjellige overflater
- Trinn 6: Flere utskriftstester
- Trinn 7: Lesemotstand
- Trinn 8: Fest festene på nytt med konduktiv epoxy
- Trinn 9: Konklusjon og neste trinn
2025 Forfatter: John Day | [email protected]. Sist endret: 2025-01-23 15:02
Av rachelfreirewww.rachelfreire.com Følg mer av forfatteren:
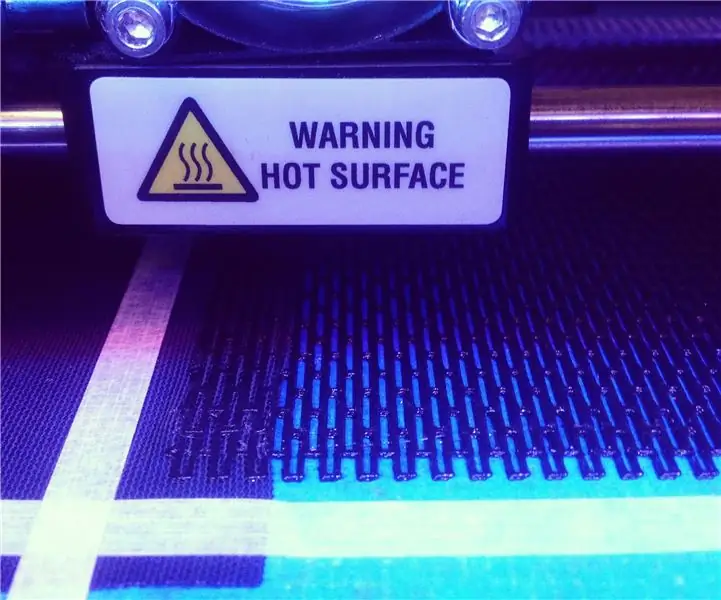
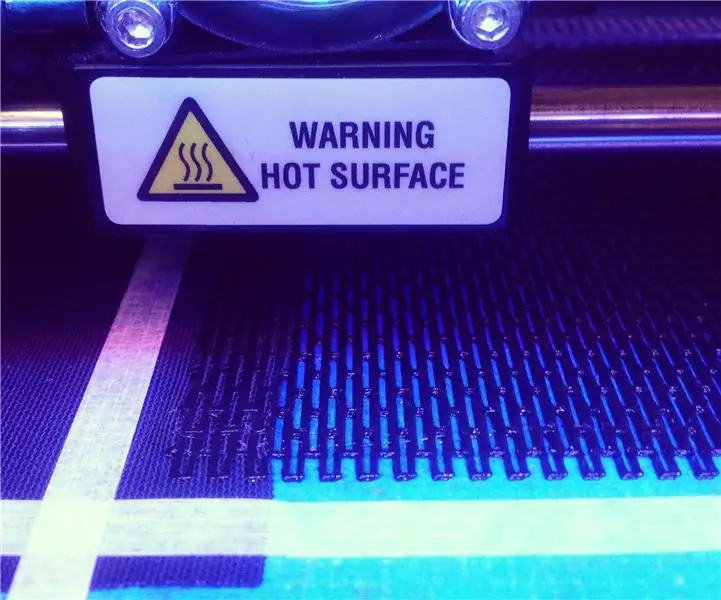
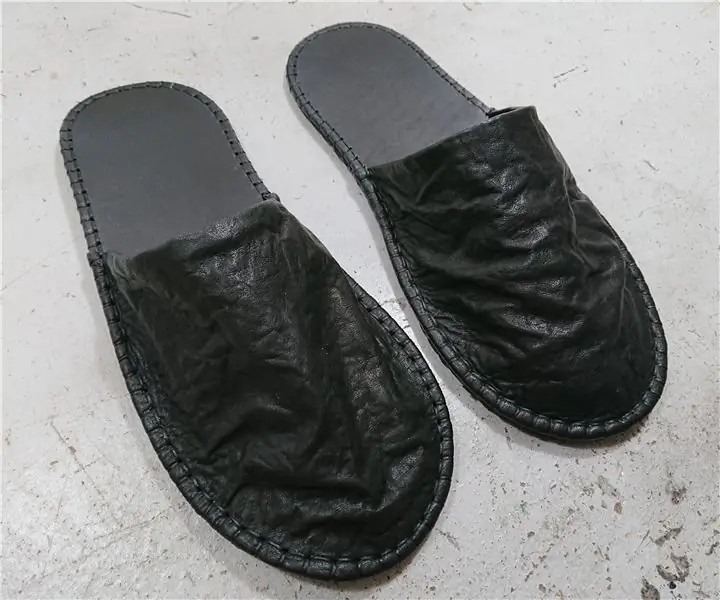
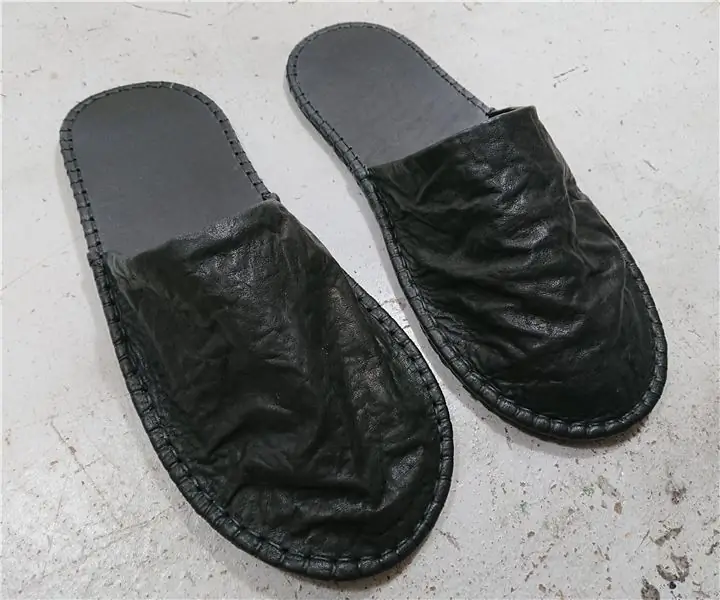
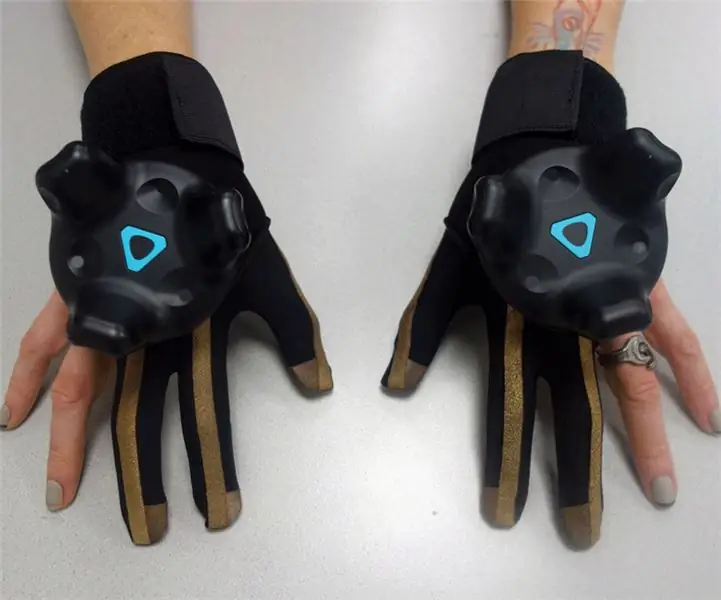
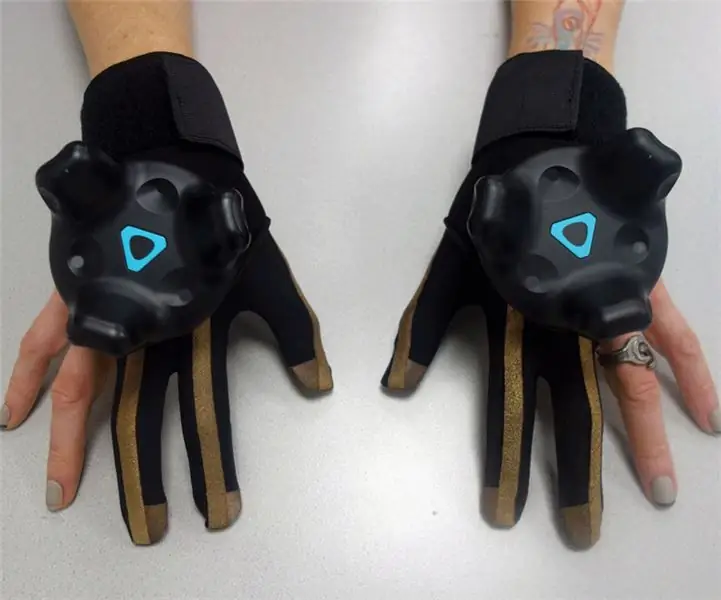
Om: designer, lær ninja, tech explorer, ruiner av manikyr Mer om rachelfreire »
Dette instruerbare dokumentet mitt første forsøk på 3D -utskrift av konduktive snaps på stoff. Jeg ville 3D -skrive ut en kvinnelig snap som ville koble til en vanlig metallhanknapp.
Filen ble modellert i Fusion360 og skrevet ut på en Makerbot Rep2 og en Dremel ved bruk av Black Magic 3D ledende grafen PLA.
Trykknappene er YKK 'Snapet' åpne stikklåser (størrelse 12L) og er 7,5 mm over. De brukes ofte av eTextiles -praktikere, ettersom de er de minste tilgjengelige. Du kan kjøpe dem i forskjellige størrelser fra forskjellige leverandører, men de ser ut til å være et standardisert design. Kjøp størrelse 12 her.
Målet mitt er å utforske måter å lage et plagg på som er ledende og elastisk og helst ikke bruker harde metaldeler. Å lage kontakter som er kompatible med eksisterende snaps som kan kjøpes, vil gjøre det lettere å teste og gjenta.
Denne testen fungerte overraskende bra, og filen er verdt å skrive ut, men den trenger definitivt mye mer justeringer. Foreløpig kan den skrives ut og testes som den er, men er definitivt et bevis på konseptet i stedet for en fullt fungerende snap som kan skrives ut pålitelig f.eks. PLA har en tendens til å krympe, og snapsene har en begrenset levetid.
Hvis du skriver ut denne filen, vennligst legg igjen en kommentar og fortell meg funnene dine!
Flere bilder her:
Disse undersøkelsene er en del av et større prosjekt kalt Second Skin, en prototypedrakt for eTextiles. Jeg vil laste opp alle filene, mønstrene og dokumentasjonen etter hvert som de er ferdige. Du kan følge prosjektet her, eller via nettstedet mitt:
Du bør også sjekke ut Rewear av Lara Grant. Hun har jobbet med et modulært system for wearables basert på et brødbrett med snaps 3D trykt på stoff. Hun har også fokus på bærekraften til disse teknikkene, noe jeg også ser på som en integrert del av deres fremtidige utvikling. Vi vil snart integrere våre eksperimenter i et dedikert nettsted for etextile -kontakter, så sørg for å sjekke Laras nettsted og Instructables også!
Trinn 1: Fusion360 -filer
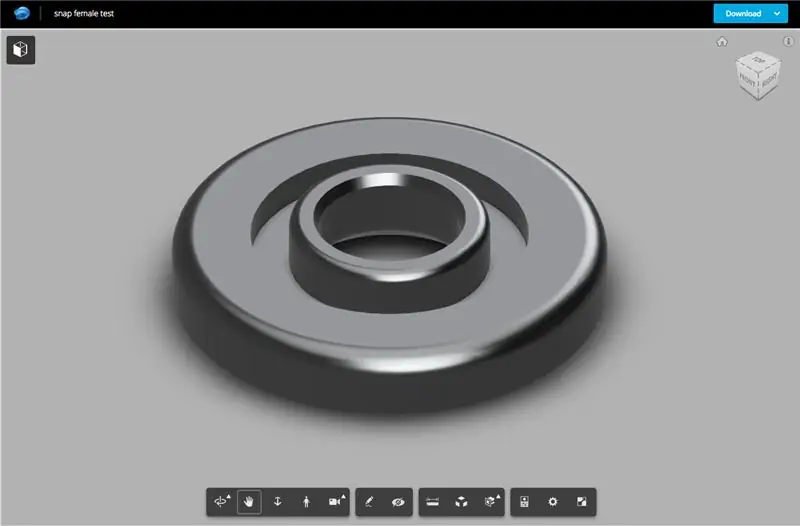
Filen ble modellert ganske raskt ved hjelp av Fusion360.
Jeg tok så mange målinger som mulig fra en eksisterende snap og laget en grov design. Fordi snapet er så lite, ble noen av de indre proporsjonene gjort ved hjelp av gjetninger og vil derfor trenge mer lek.
Lenke for å laste ned nåværende versjon her:
Filen som er vedlagt denne instruksjonsboken var mitt første forsøk. Det fungerte ganske bra. Den koblede filen (ovenfor) ble justert, noe som gjorde foten til bunnen mer solid. tanken er at det vil hjelpe det til å holde seg til stoffet bedre. Selv om dette hjalp noe, er begge filene fortsatt verdt å teste hvis du vil skrive ut en versjon av dette. Jeg hadde suksess og fiaskoer med begge.
Jeg vil også påpeke at jeg er en total Fusion-nybegynner og hadde ninja-hjelp til å justere filen fra JON-A-TRON. Du bør ta en titt på 3D -utskriftskursene hans!
Hvis du vil bruke større snaps (for eksempel 15 mm som er mer vanlig), ville jeg forvente at denne filen kan endres i størrelse og skrives ut med de riktige dimensjonene, og at den også kommer til større versjoner av denne snap -designen. Jeg har ikke prøvd dette enda, da jeg prøver å gjøre alt så lite som mulig.
Disse metallklipsene er fantastiske, men ofte er matrisen vanskelig å finne. Jeg bruker Prym vario tang for å påføre snaps for hånd, og det er vanskelig å finne snap -døen for å passe. Så jeg lagde en utskrivbar fusjonsfil for 12L Snapets;) Igjen er den ikke perfekt ettersom 3D -utskrifter har en tendens til å krympe og forvrenges og til slutt gå i stykker. Men jeg har nettopp skrevet ut nye når dette skjer! Filer er festet til innsiden (kontaktdelen) og utsiden (ringfeste) dør. Den ene er en brøkdel større enn den andre. Hvis du bruker dem på feil måte, vil klemmen sette seg fast i matrisen.
Trinn 2: Skriv ut test og oppsett
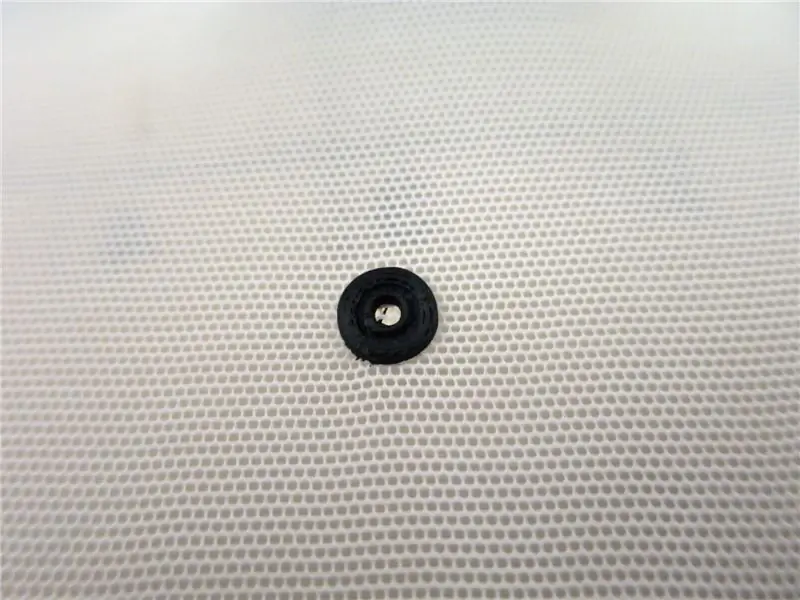
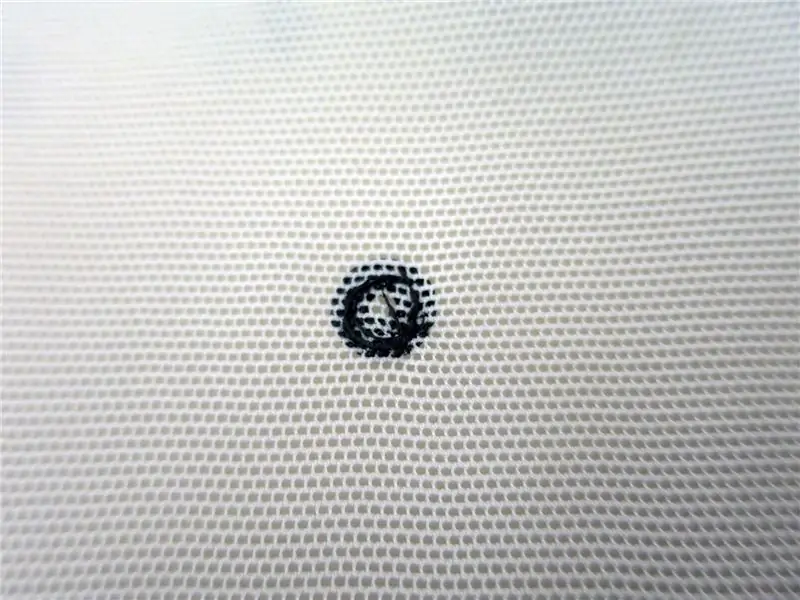
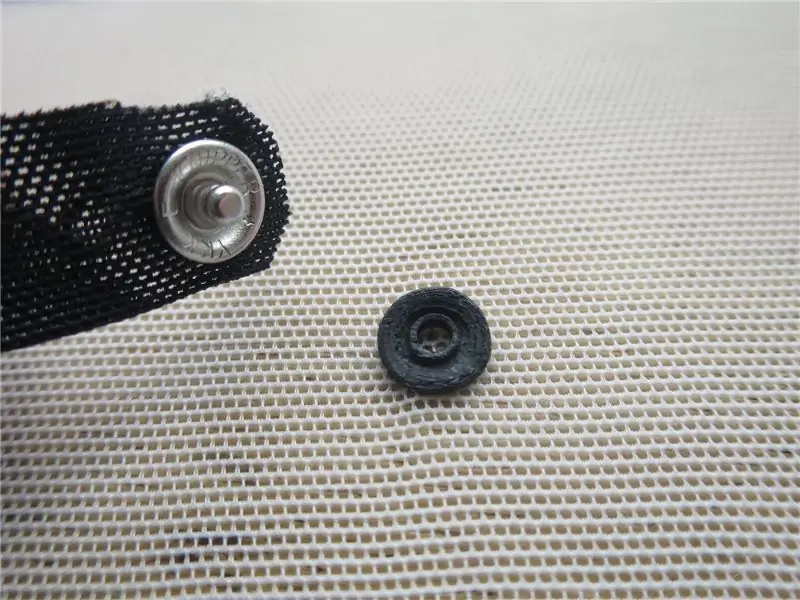
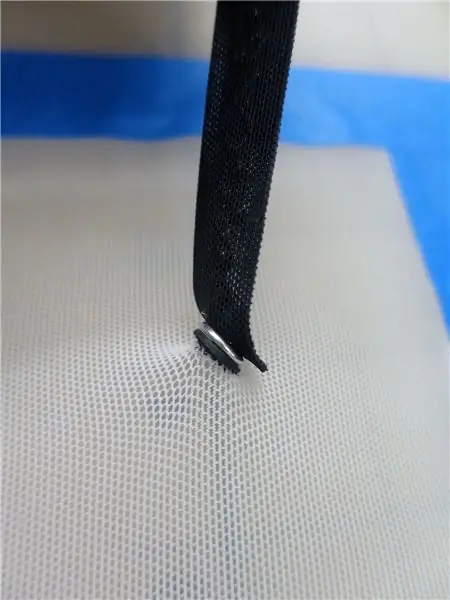
Dette første snapet ble skrevet ut av Lara Grant. Hun jobber med et lignende prosjekt med å lage et snap -stoff og har en flott instruksjon om 3D -utskrift på stoff. Du bør også sjekke ut hennes wearables -klasser
Det er Black Magic 3D -grafenfilament og ble skrevet ut på en Makerbot Rep 2 med utskriftstemperatur og ekstruder satt til 220 °
Vi har begge testet en teknikk der du skriver ut et grunnlag av filament, setter maskinen på pause for å sette inn stoff og deretter fortsetter utskriften. Dette betyr at filamentet vil smelte rundt stoffet og skape en tetning. Du kan se dette i det andre bildet; det er filament på undersiden av stoffet. Dette laget ble skrevet ut på sengen først, deretter ble skriveren satt på pause og stoffet ble satt inn. Skriveren ble deretter satt på pause og utskriften fortsatte.
Det fungerte fantastisk! Første forsøk på å bruke filen jeg hadde laget 10 minutter tidligere.. Og den knipset til og med veldig godt!
Denne snapsen du ser her ble skrevet ut på powernet. Det er et materiale jeg bruker mye og bruker for det relaterte prosjektet Second Skin som bruker strekkretser. Det er 4 -veis stretch og brukes til undertøy og danseklær. Det fungerer bra fordi det er et fint syntetisk nett. Den er vanligvis laget av polyamid, slik at filamentet smelter overflaten og fester seg godt til den. Filamentet kan også smelte inn i og rundt overflaten av selve mikrofinnet.
Powernet har god strekkfasthet, og hvis den strammes med tape når du legger den på sengen, blir den ikke klemt av ekstruderen.
Trinn 3: 3D -utskrift på et ledende stoffspor
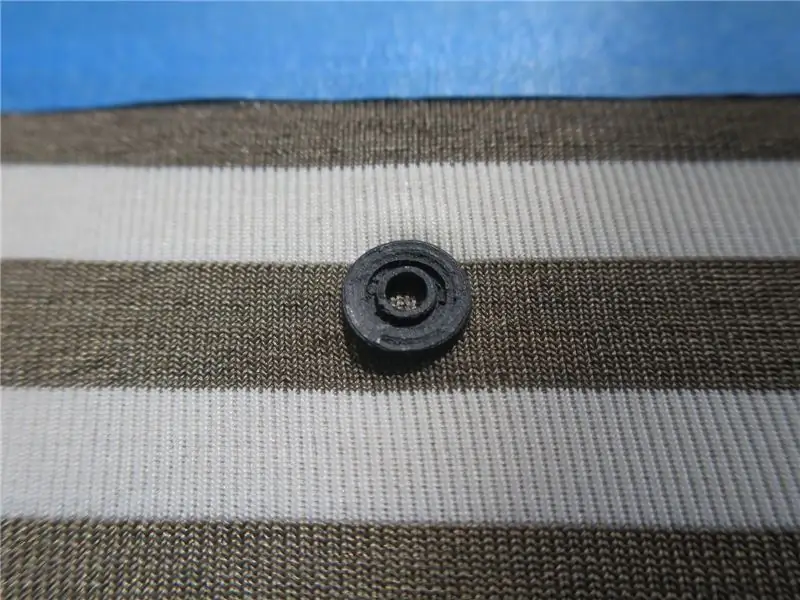
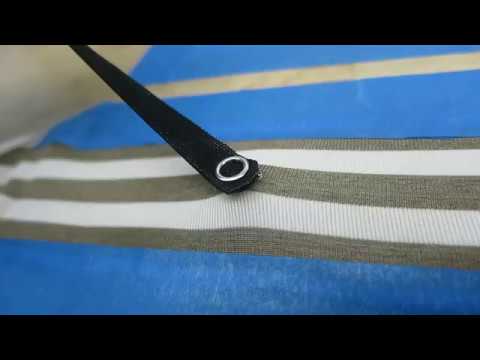
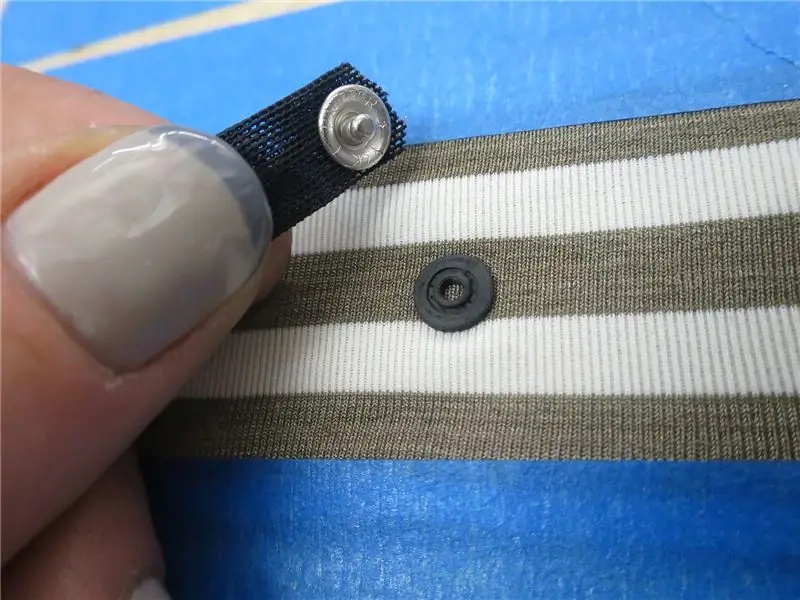
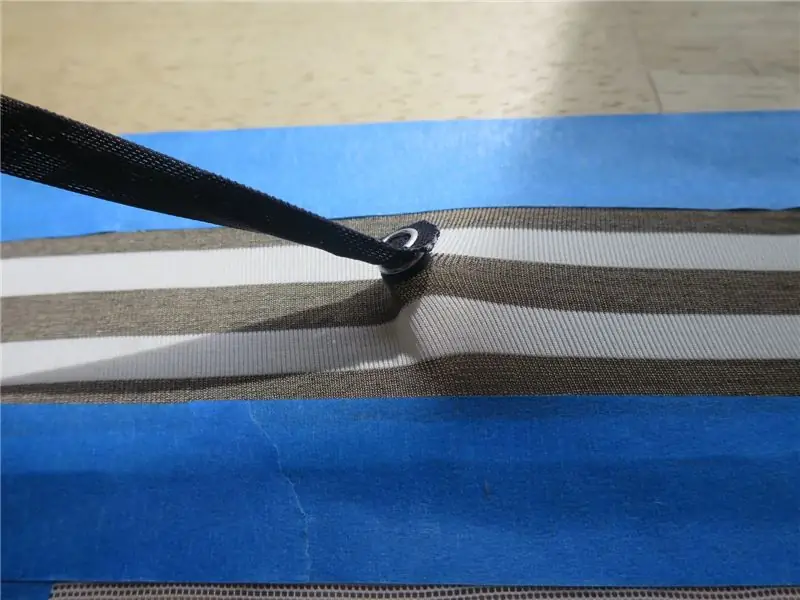
Dette strålende stoffet er en stretchjersey strikket med ledende spor. Jeg tror det er trolldom av Hannah Perner-Wilson og Mika Satomi fra Kobakant og ble skreddersydd. Jeg fikk noen på eTextiles sommercamp, og vi bestemte oss for at dette ville være en flott ting for å teste den elektriske forbindelsen mellom stoff og trykk.
Det er jerseymateriale, og det ser ut til at fibrene ble belagt før de ble vevd, i stedet for at det ledende belegget ble trykt på etter produksjon. Det er for tykt til å skrive ut gjennom overflaten (som i den tidligere testen) ettersom filamentet ikke ville koble seg til på samme måte som det gjør gjennom hullene i powernet.
Vi satte Makerbot til å skrive ut rett på stoffet. det du ser ovenfor er den første testutskriften på dette materialet.
Mange forskjellige mennesker har testet 3D -utskrift på stoff, og det ser ut til å variere avhengig av trykkets art, materialer og maskiner som brukes. De fleste suksesser ser ut til å involvere masker ettersom vevet er løst og filamentet kan synke gjennom stoffet for å skape en binding.
Noen senker munnstykket på skriveren. Dette knuser ekstruderen inn i stoffet og tvinger filament inn i fibrene, men kan trekke materialet. Et annet alternativ er å heve utgangspunktet for ekstruderen for å starte utskriften, noe som betyr at du kutter utskriften på en slik måte at den starter like over tykkelsen på stoffet. Jeg forestiller meg at dette ville fungert godt hvis stoffet ditt var tykt. Siden vår er ganske tynn og flat, trykte vi rett ut på materialet med standardinnstillingene, bare ved å slå av flåtene og eventuell støtte.
Det fungerte vakkert! Dette kan ha skyldes forskjellige faktorer:- Overflaten på dette stoffet var ideell for utskriften å feste- ekstruderen var akkurat ved den perfekte temperaturen på dette tidspunktet (dette filamentet kan være veldig inkonsekvent)- gudene av 3D -utskrift var i godt humør, og vi var super heldige
Tydeligvis trenger dette mer testing.
Trinn 4: Test konduktivitet

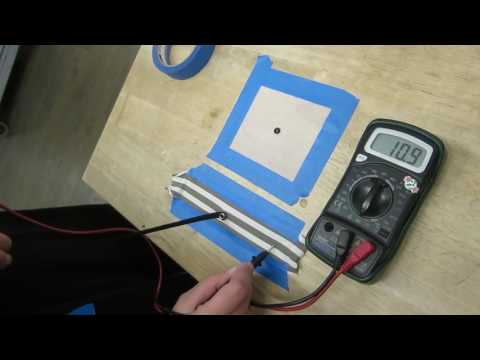
Denne testen brukte en stretch eTextile -kontakt laget med Karl Grimm ledende tråd. Inne i den svarte kontakten er det en sikksakk av ledende tråd isolert av stofflag på hver side. Hver ende har en hann snapet. Alle disse materialene har ganske lav motstand.
Motstanden over 30 cm -kontakten, gjennom snap og over 8 cm ledende stoff ser ut til å være omtrent 10 ohm. Dette var overraskende og så ut til å holde seg ganske stabilt selv når det var strukket. Jeg er ikke sikker på at dette er en nøyaktig og repeterbar lesning!
Trinn 5: Skrive ut på forskjellige overflater
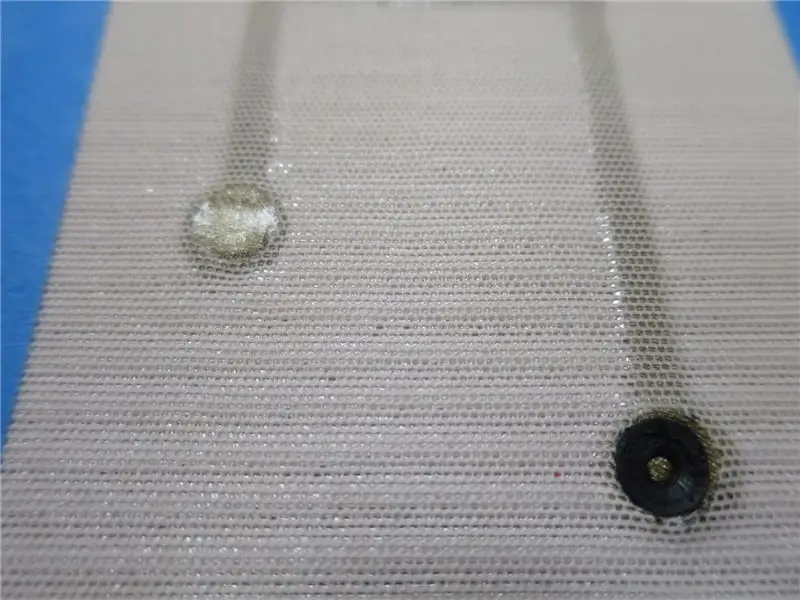
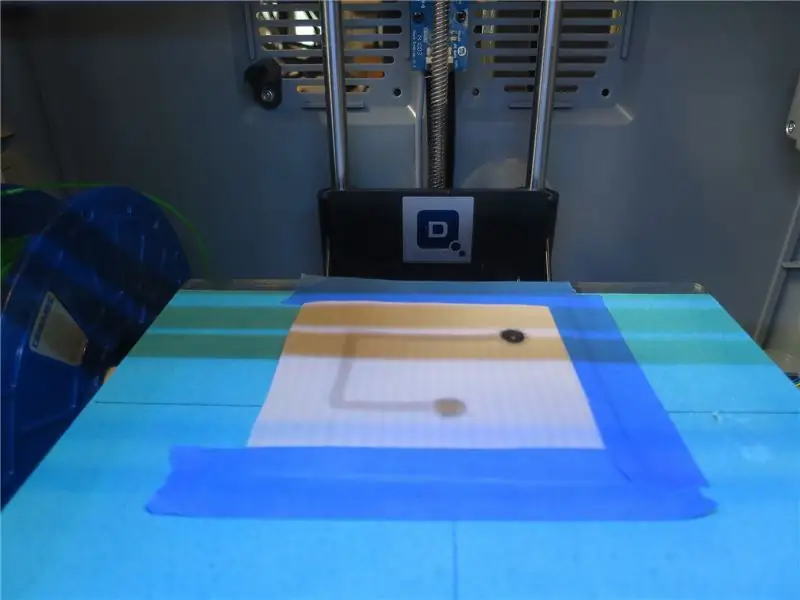
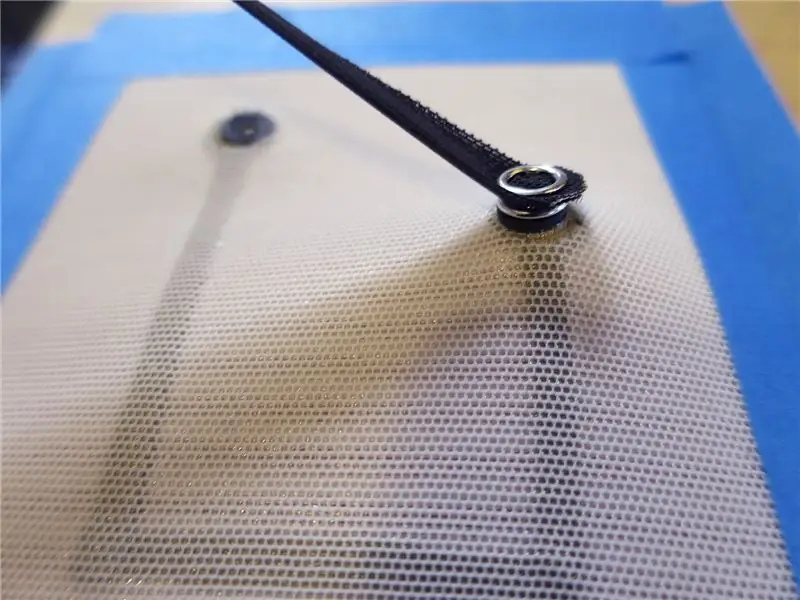
Deretter bestemte jeg meg for å prøve å skrive ut på en Dremel. Dette er hovedsakelig fordi Makerbot hadde en hvesende passform, men variasjon er alltid bra. Igjen ble utskriftstemperaturen og ekstruderen satt til 220 °
Jeg har jobbet med limte, isolerte, tøyelige ledende spor for eTextiles. Disse stoffene bruker limte tekstillag med Bemis SewFree fusing, en superfin varmebindende film. Dette betyr at stoffprøvene var tykkere enn de forrige testene. De ledende sporene er isolert inne i powernet -stoff og har bare endene eksponert som runde pads.
Da jeg først skrev ut filen med standardinnstillinger, smalt den inn i stoffets overflate og forvrengte utskriften. Du kan se resultatet i det første bildet. Snapen fungerte ikke denne gangen.
Jonathon viste meg hvordan jeg skjærer filen i Cura og hever startposisjonen til ekstruderen med 0,4 mm.
For den neste testen la jeg også til et lag med SewFree -liming på overflaten jeg skulle skrive ut på. Dette var for å se om dette gjorde noen forskjell for hvordan utskriften holdt seg.
Det fungerte i utgangspunktet veldig bra, som du kan se på det siste bildet. Dessverre etter et par snaps løsnet snapet fra stoffet og falt av.
Trinn 6: Flere utskriftstester
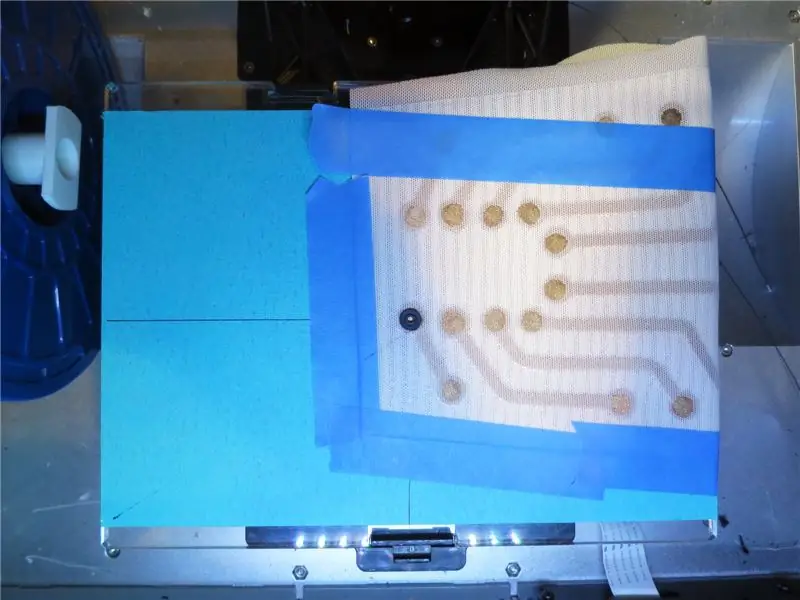
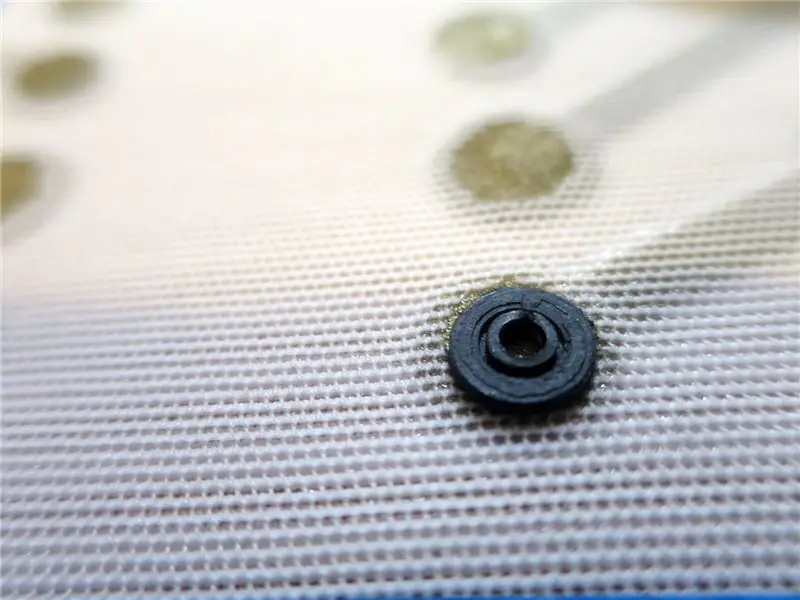
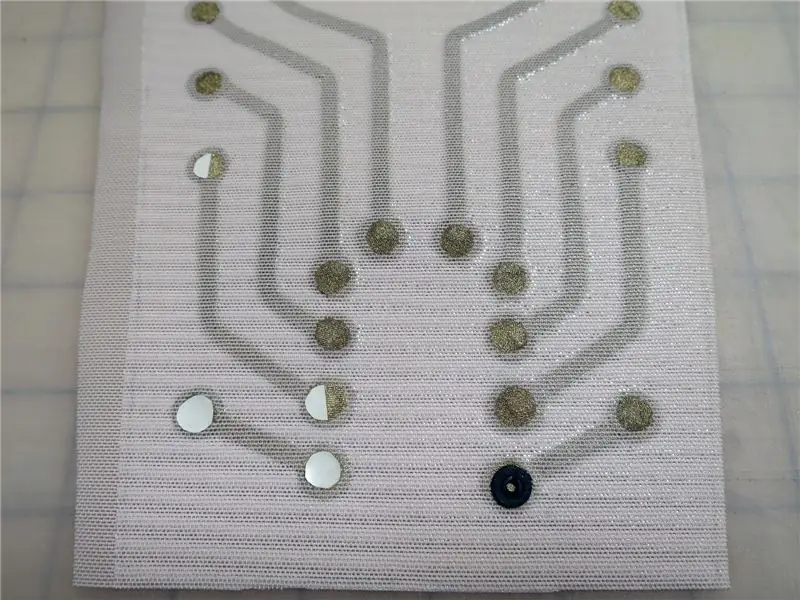
Jeg prøvde deretter å skrive ut flere snaps for å se hvordan strømmen strømmet gjennom to snaps i hver ende av et ledende spor. Siden jeg bare hadde en fungerende snap på den forrige testen, kunne jeg ikke sjekke. Kanskje utskriften Lara hadde laget tidligere var et tilfelle. Jeg lagde et raskt panel for å prøve flere utskrifter.
Siden dette var en test, bestemte jeg meg for at jeg skulle skrive ut hver snap individuelt, i stedet for å prøve å skrive ut flere snaps på ett stoffstykke.
Tre grunner: 1. Jeg ønsket ikke å investere tid i å lage en layoutfil da stoffkretsen jeg skrev ut på ble laget upresist2. Utskriftene mislykkes ofte 3. Jeg ville ikke at useriøs filament skulle dra over stoffet
Jeg stilte hver snap opp til et sentralisert punkt og skrev dem ut en etter en. Hver og en kom perfekt ut.
Jeg la til SewFree fusing til noen av de ledende putene. Du kan se dette på bildene som hvite sirkler og halvsirkler. Dette er papirunderlaget som skrelles bort. Jeg lot den stå på så det er lettere å se på bildene. Jeg tenkte at det ville være godt å se hvordan sammensmeltingen påvirket overholdelsen på tvers av det samme trykket. De viste seg ganske like. De fleste satt fast, og noen falt av. Ikke sikker på hvorfor, men jeg antar at det skyldes små forskjeller i tykkelsen på stofflaget. De ble alle skrevet ut raskt etter hverandre på samme skriver med de samme innstillingene.
motstanden over et 15 cm ledende spor gjennom to resistive snaps var rundt 50 ohm. Dette ble gjort umiddelbart etter utskrift og virket superledende, så vi trengte flere tester.
Trinn 7: Lesemotstand
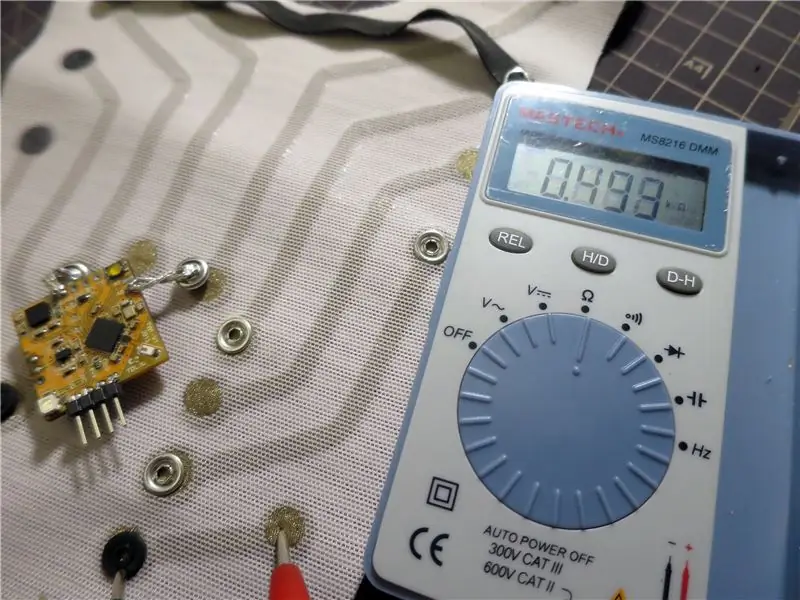
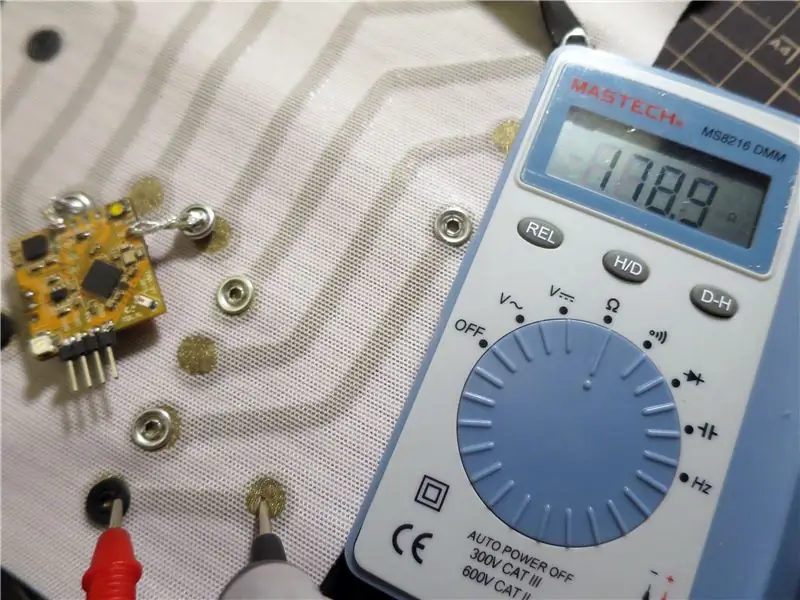
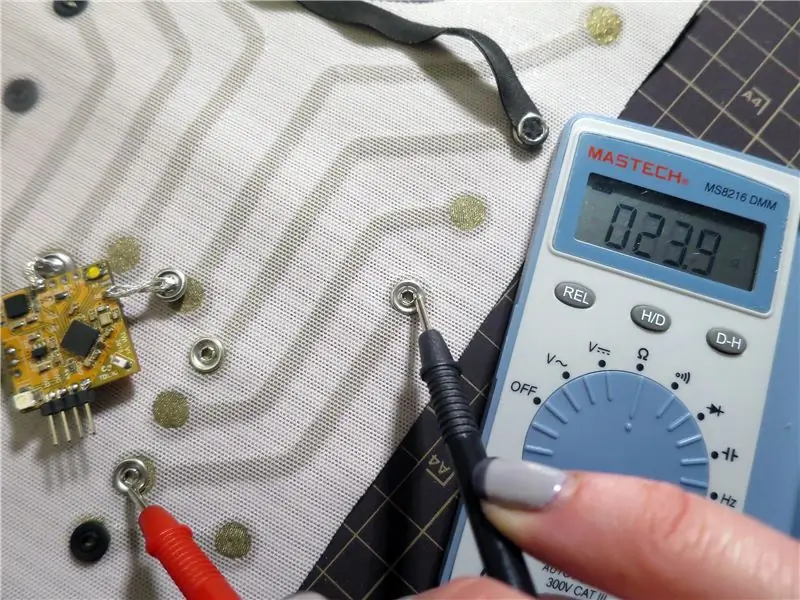
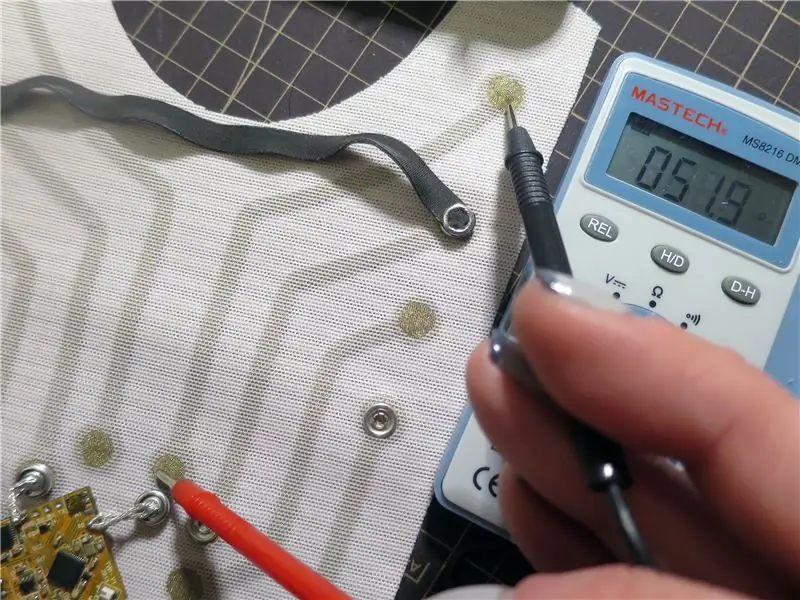
Avlesningene jeg tok fra snapsene syntes å variere mye. Dette endret seg også over tid.
Trinn 8: Fest festene på nytt med konduktiv epoxy
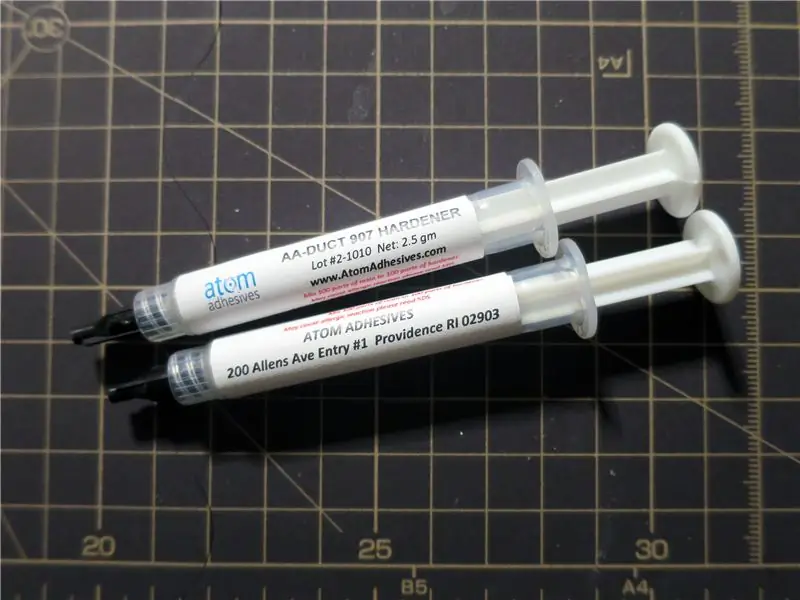
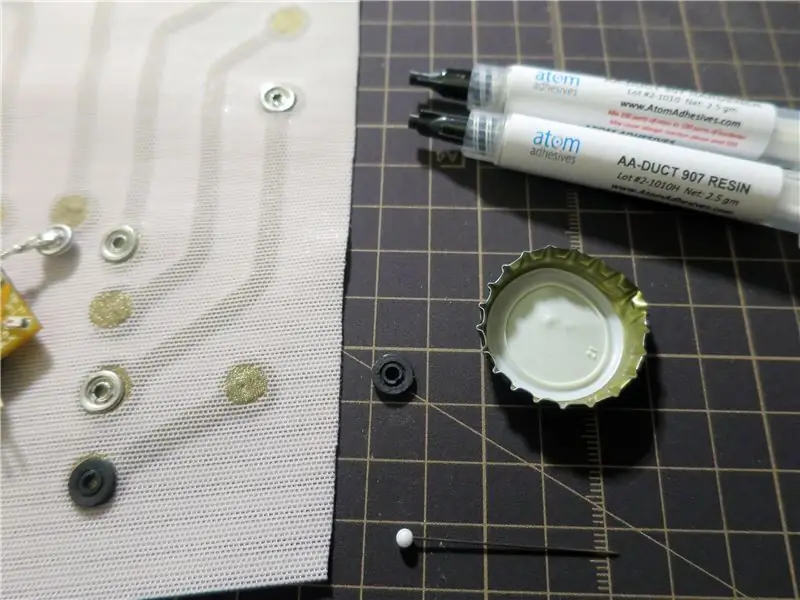
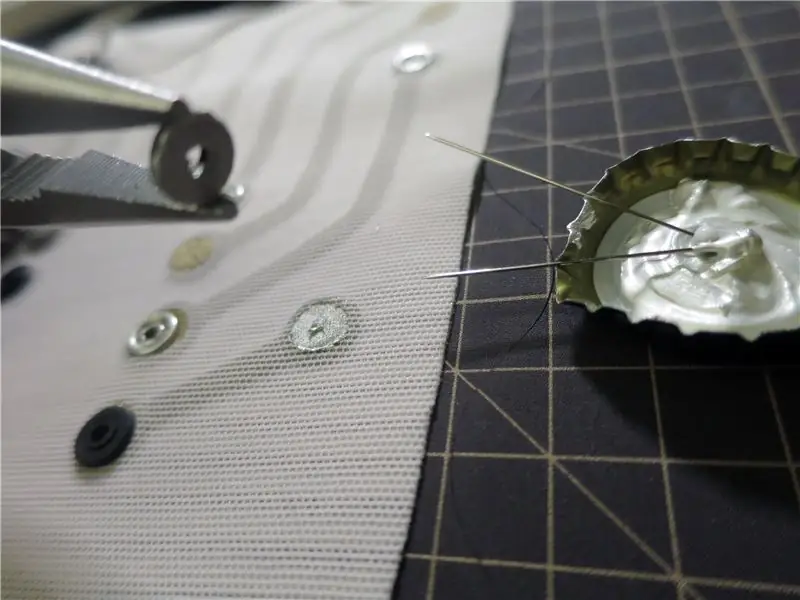
Noen av snappene falt av etter litt bruk. De holdt seg ikke så godt til det tette limte materialet som med de tidligere testene.
På dette tidspunktet er det verdt å undersøke et annet alternativ: kan snapene skrives ut og deretter festes til stoffet etterpå.
Det kan være sant at snaps kan skrives ut på visse stoffer, men må limes til andre. Dette kan fortsatt være et brukbart alternativ.
Jeg brukte ledende epoxy og limte to av snapsene tilbake på plass for å se om limet kan binde seg og lede pålitelig.
Dessverre fester dette ikke godt til stoffet i det hele tatt. Epoksyen er ganske krittaktig og liker ikke det tette syntetiske materialet. Selv om limet tillot en liten mengde strøm å strømme, falt snapsene av etter ett smekk.
Trinn 9: Konklusjon og neste trinn
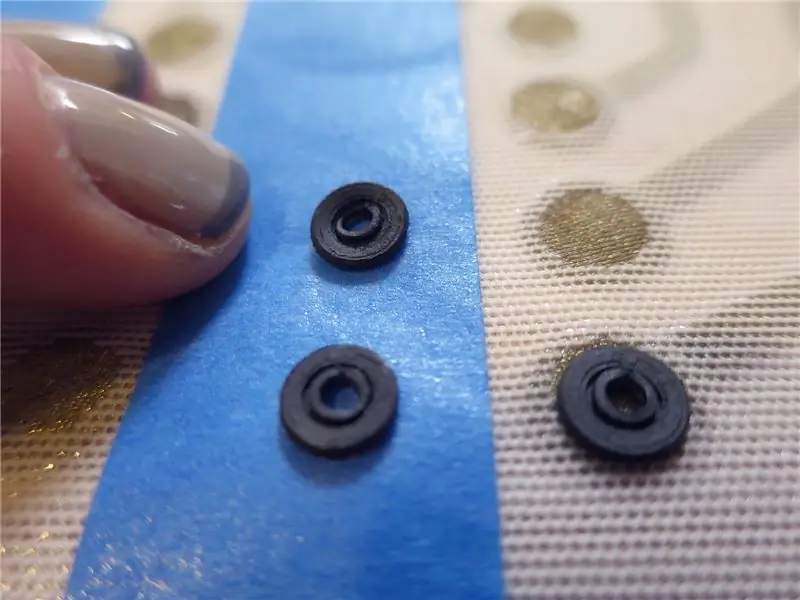
Denne snap -designen fungerte veldig bra for en første test. Den klikker trygt, kan lede en liten mengde strøm og er et godt bevis på konseptet.
Dessverre ga de ikke konsistent ledningsevne. Noen var ok og andre fungerte ikke i det hele tatt. Det ser ut til at det er et problem å bruke tettvevd stoff, så dette fungerer ikke så bra for mine limte stoffer. Å bruke mer åpen veving som trøya, og spesielt powernet virker som det beste alternativet. Problemet med det er at jo mindre tett et stoff er, desto dårligere er konduktiviteten for etekstiler.
Det er ganske mange praktiske problemer med PLA. Det har en tendens til å deformere og krympe. Noen av snapsene fungerte umiddelbart, noen trengte noen få første tvungne nedleggelser før de overholder det, tilsynelatende for å strekke utskriften litt. Noen virket for små til å snappe i det hele tatt.. Det hele var litt inkonsekvent.
Jeg har også lest at ledningsevnen til disse materialene kan endres over tid. I dette tilfellet vil jeg si at trykket i selve snapping kan påvirke dette. Kjøring av strøm gjennom snap kan også øke motstanden permanent. Dette vil definitivt innebære mer testing.
Det er en ganske god oversikt over Black Magic 3D -filamenter her
Jeg vil bruke denne snap -ideen i en hanskedesign. Jeg vil finne en måte å lage avtagbare kontakter for strekkfølere. Tanken ville være at denne snap -filen kan integreres direkte i en 3D -trykt sensor for å koble den til en krets.
I anmeldelsen fant jeg denne prosessen interessant og informativ. Det er ikke stabilt nok til å gi konsistente målbare resultater, og jeg vil gjerne utforske videre i mer kontrollerte eksperimenter.
Hvis du prøver noen av disse utskriftene, kan du legge igjen en kommentar!
Anbefalt:
DIY puste sensor med Arduino (ledende strikket stretch sensor): 7 trinn (med bilder)
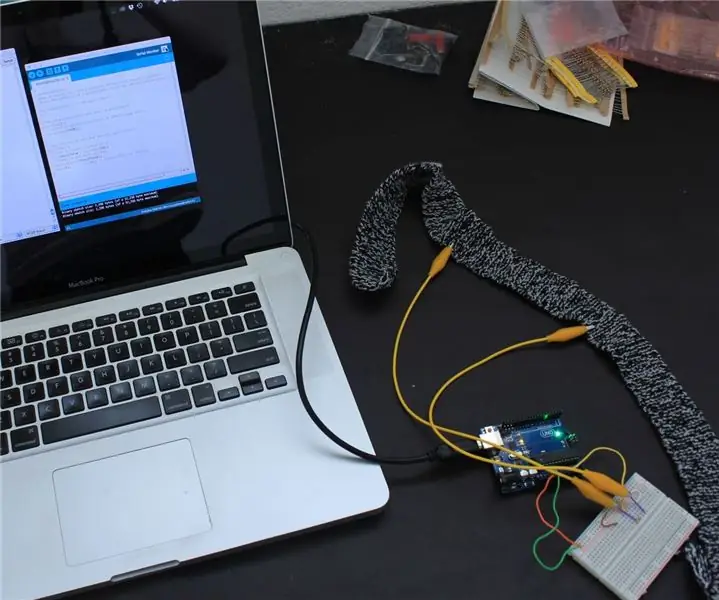
DIY Breath Sensor With Arduino (Conductive Knitted Stretch Sensor): Denne DIY -sensoren vil ha form av en ledende strikket stretch -sensor. Det vil vikle seg rundt brystet/magen, og når brystet/magen utvider seg og trekker seg sammen, vil også sensoren, og følgelig inndataene som mates til Arduino. Så
Lag elektronisk lyd med ledende gips: 9 trinn (med bilder)
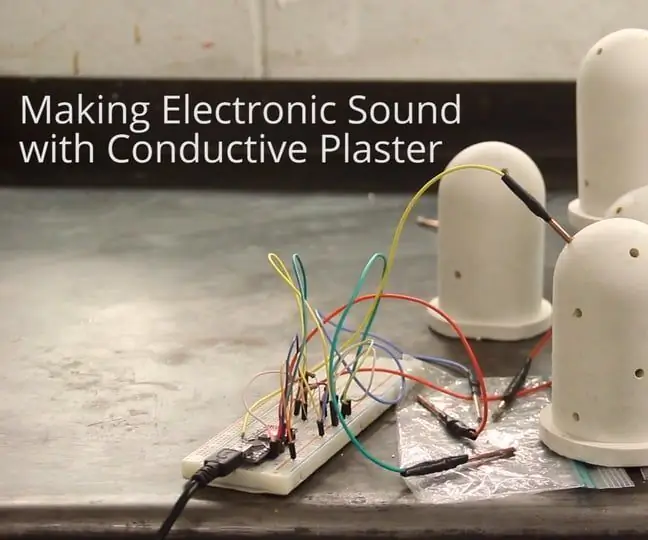
Lag elektronisk lyd med ledende gips: Etter blorggggs prosjekt om ledende silikonkrets bestemte jeg meg for å gå på mitt eget eksperiment med karbonfiber. Det viser seg at en form som er støpt ut av gips med karbonfiber, også kan brukes som en variabel motstand! Med noen få kobberstang og
Ledende lim og ledende tråd: Lag en LED -skjerm og stoffkrets som ruller sammen: 7 trinn (med bilder)
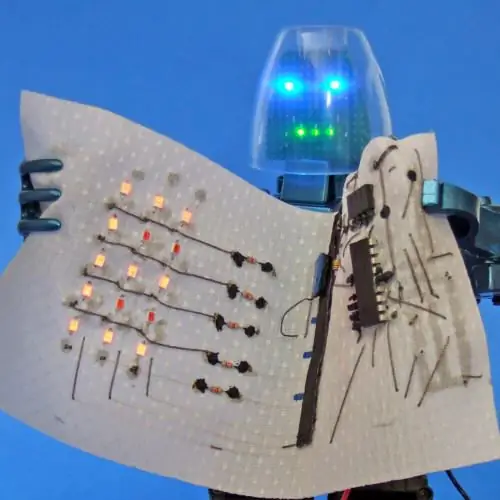
Ledende lim og ledende tråd: Lag en LED -skjerm og stoffkrets som ruller sammen. Lag dine egne ledende stoffer, tråd, lim og tape, og bruk dem til å lage potensiometre, motstander, brytere, LED -skjermer og kretser. Bruk ledende lim og ledende tråd kan du lage LED -skjermer og kretser på ethvert fleksibelt stoff
Ledende stoff: Lag fleksible kretser med en blekkskriver. 4 trinn (med bilder)

Ledende stoff: Lag fleksible kretser ved hjelp av en blekkskriver .: Ekstremt fleksible og nesten gjennomsiktige kretser kan lages med ledende stoffer. Her er noen av eksperimentene jeg har gjort med ledende stoffer. De kan males eller tegnes på med motstand og deretter etset som et standard kretskort. C
Hvordan sy med ledende tråd med Diana Eng: 10 trinn (med bilder)
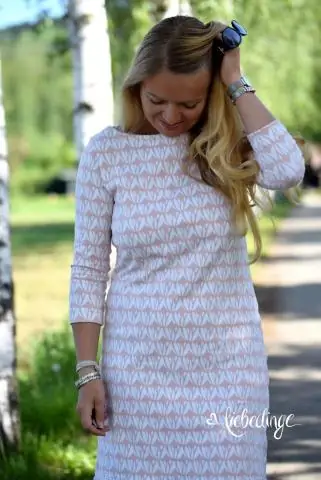
Hvordan sy med ledende tråd med Diana Eng: Kombinere elektrisitet og mote! Vanskelighetsgrad: Fremdeles læring Tidslengde: 45 minutter Materialer: syplagg, ledende tråd, saks, to lysdioder, CR2032 klokkebatteri, BS7 batteriholder, blekkpenn som forsvinner , nål-nese tang, r